by B.B. Pelletier
First, the rifling broach
Before we begin, let me explain something I left out of Part 1, where I talked about cut-rifling. I explained how cut-rifling works, but I didn’t include the high-speed modern way of doing it, which is the rifling broach. Instead of just one cutting surface, a broach has cutters for every rifling groove, so it cuts them all at the same time. And, a gang broach, like the one shown, has progressively deeper (higher) cutters behind one another, so the entire barrel can be fully rifled in a single pass. Broach rifling is the modern, cheaper way of doing cut-rifling, however, the cutting broach takes a long time to make and must be sharpened often on all cutting surfaces. A small shop making all different calibers still cuts the grooves one at a time.
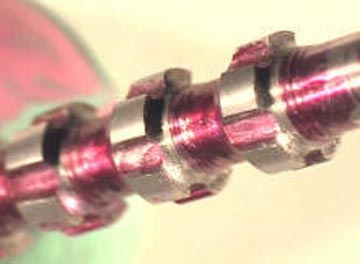
This gang broach can rifle a barrel in one pass. It is a chore to make and keep sharp.
Button rifling – faster and cheaper
Another way to rifle barrels is the most popular method used today. The button rifling method doesn’t cut the rifling pattern – it irons it into the barrel! A carbide tool called a button is either pushed (most common) or pulled through the barrel. As it moves, the hydraulic head also turns at the desired rifling twist rate. It is correct to say the button engraves a reverse of itself inside the bore, but it doesn’t do it by cutting. Instead, it displaces metal, actually hardening and smoothing the inside of the barrel as it goes.
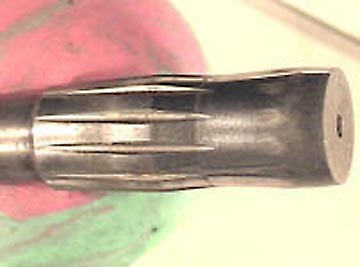
A rifling button irons the bore into shape. This one is for microgroove rifling.
Rifling buttons wear just as broaches do, but because of how they are shaped and how they work, the wear is slower. Also, they leave a mirror surface behind them. Many of today’s custom barrelmakers use the button method, as do many high-volume barrelmakers.
Metal stresses
Unlike the cut-rifling method, the button method sets up stresses in the barrel. These have to be dealt with, or the barrel will “walk” as it heats up during firing. You can always tell a cheap barrel; as it heats up, it starts spraying shots in an ever-expanding pattern. A good button-rifled barrel has been properly stress-relieved and can group as well as a cut-rifled barrel. While it may take an hour to cut-rifle a barrel with a modern barrelmaking machine, a button-rifled barrel can be rifled in about a minute. More time will then be spent on relieving stress (or not), but the total doesn’t add up to the manhour that’s invested in a cut-rifled barrel. And, remember, if the man running the machine makes $20/hour, the barrel will have to include $100 just to cover his cost. The cost of the blank, of drilling the hole and of reaming and lapping are all extra. A good cut-rifled barrel will retail for $400 and up, while quality button-rifled barrels may start at $150.
Longer life
As the button irons the bore, it hardens the steel, resulting in a barrel that can outlast a cut-rifled barrel. Further steps, such as cryogenic treatment and plating with hard chrome, will add even more wear resistance. That’s a strong sales point, as long as the stresses have been properly relieved. In airguns, there are no hot combustion gases to worry about; but, in a firearm, the gases actually vaporize the steel of the bore over time. Button-rifled bores are more resistant to this. Also, they usually do not need to be lapped after rifling, though the top custom makers (e.g., Lilja) still do.
We’ve looked at two of the three popular rifling methods. Next time, we’ll look at hammer-forging, which is the fastest method of all and also the most troublesome.
B.B.
Do you know what rifle process Anschutz (Germany) uses for their smallbore rifle and air rifle barrels?
No, I don’t. Why don’t you contact them and ask?
B.B.
Would it be the same techniques for brass barrels like the sheridans?
Also, I cannot yet imagine how to make the choke.
Yes, the brass barrels are rifled the same way.
You can choke a barrel by rolling it under pressure after it is rifled.
B.B.
Say, BB…
Do you know if a button leads itself? Or in other words, does it turn by itself? Those are some great pictures btw.
I always thought that a button screwed itself through the bore, but apparently that’s incorrect. According to the research I conducted, a button can be used for any twist rate (I suppose within limits) and the pushing ram turns according to the desired twist.
B.B.
RU saying the same button can be used for various twists?
Yes, within limits. I’m not just saying it, that’s what the barrelmakers say on their websites.
B.B.
I made thousands of .22 .25 and 9mm barrels back in the day when I worked for a now former gun manufacturer. We used the button rifling method, and the button was pulled through the barrel, with a straight pull. The barrel butted against a thrust bearing allowing the barrel to rotate as the button was pulled.Lots of special high pressure lube to prevent sticking. The button you show in your picture is interesting, as the “coke” bottle shape, with the second bulge after the grooves irons the tops of the lands for a better finish. We used this on the .22 barrels and later on the 9mm as well. Interesting thing is how you can feel the button going through the barrel if you put your hand on the outside during the forming process.
ken1911,
Thanks for that insight. I didn’t mention the springy-ness of the steel, and I bet it would suprise people how much it moves.
Thanks,
B.B.
Hello BB,
I’m new in the air gun hobby and I am so glad that I stumbled onto this site. Anyway, I have a question regarding free floating barrel i.e. what is it and what are the advantages. They look kinda strange on PCP’s. Also, is the air tank of the Talon SS in direct contact with the barrel and if so, wouldn’t it affect the accuracy as pressure in the tank drops ?
Thanks and regards,
DKY
DKY,
Free-floated barrels are supposed to have repeatable vibration patterns, so the bullet exits the muzzle at the same point in its vibration. This is similar to the reason for hlding spring rifles loosely when shooting them.
The AirForce rifle have free-floated barrels suspended by two bushings. The Talon SS barrel only extends half an inch or so past the front bushing. The longer 18 and 24-inch barrel extend much farther past the front bushing.
However free-floated barrels are not the cure-all for accuracy. The Logun Dominator and Gladiator are both free-floated, yet they are not as accurate as any of the AirForce rifles, despite costing twice as much. I have noted in my testing that the Loguns are only capable of one-inch groups at 50 yards, where the AirForce guns will shoot a half-inch on a perfectly windless day.
In answer to your other question, the air tank of an AirForce rifle does not contact the barrel at all.
B.B.
BB,
Thx for the prompt reply. I have heard of the artillary hold for springers before but never understood the concept and your response on the free floated barrel some how just made every thing clicked in my mind. I’ve seen high speed footage of arrows just as they were shot and they don’t go “straight as an arrow” either. They wiggle at their natural frequencies as they travel toward the target.
Funny that you used the two PCP’s for illustration that I happened to be considering. You definitely helped me making up my mind on which one to buy. Eagerly awaiting Pyramyd Air’s Christmas flyer.
Btw, I made a quick search on barrel harmonics and read your blog. Unfortunately, I also read the “comments” from that critic of yours. I’m a senior citizen and have met my share of “experts”. I can only count those that can WRITE as well as being able to relate to young and old with the fingers of one hand. I really appreciate your sharing of your knowledge and looking forward to reading more from you. Sorry for the long winded note.
DKY
DKY,
Thanks for your kind comments. Your arrow comparison is a good one that I have never thoughyt of. Most people have seen an arrow vibrating at slow motion in flight and should be able to make the comparison to a rifle barrel from that.
B.B.
F
can a bb gun barrel be rifled?
F,
Yes a BB gun barrel can be rifled. Rifling offers no advantage to BBs, but it does make it possible to also shoot pellets more accurately through ght same barrel.
B.B.
Hello,
Can anyone point me in the direction of rifling button manufacturers?
Thanks,
Mike K
American Mfg
Dear B.B. Pelletier,
I am a Photo Researcher for a publishing company and I am currently working on an educational textbook. The author would like to use your image of a ‘Gang Broach cutter’ , that was posted on Oct. 20, 2006, ‘How are Barrels Rifled?’. If you could contact me at athos2001@gmail.com, that would be great. I look forward to hearing from you.
All the best,
Christine
Christine,
I can tell you here that the photo isn’t available at print quality resolution.
B.B.