by B.B. Pelletier
This posting was suggested by a reader who commented that Crosman Copperhead BBs don’t seem as uniform and well-finished as Daisy premium grade BBs. He wondered whether they would be as accurate, so I thought a little test was in order. Just for the record, I’m talking about steel BBs today.
First, the BBs
To most of us, all BBs look the same. I don’t suppose most shooters look at their BBs through a jeweler’s loupe, but that’s what I did to see what our reader was talking about. He said Crosman BBs are much rougher on the surface than Daisys, and that they had the flat spots left from the forming process. I was surprised to hear the latter, because I thought all BB-makers had gotten rid of the flat spots, so I looked at a brand new Crosman Copperhead BB with a loupe. Indeed, it had a flat spot, while the Daisys did not. Also, the surface was much rougher, just as our reader had said.
I also pulled out an Avanti precision ground shot to compare it to the modern Daisy Premium Grade BB. It appears to be no smoother than the standard Daisy BB and is still not a perfectly smooth sphere like a ball bearing.
How BBs are made
A BB starts out as a piece of steel wire that is chopped into rough chunks quite a bit larger than BB size. Those chunks are fed to two steel plates that have a long spiral tapering groove. One plate turns while the other remains stationary, which rolls the rough chunk into a sphere. From there, it goes on to grinding, where it is reduced in size to the desired caliber. Next, it gets a flash plating of some anti-oxidant, such as copper or zinc. Then, it’s sorted by centrifugal force in a long spiral slide. The good BBs go on to packaging and the rejects become scrap. I saw this process in the Crosman plant, where they produce 10 million BBs every workday.
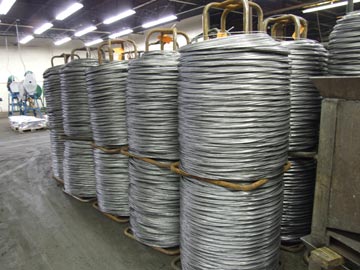
Each spool of steel wire (stacked in twos) in the Crosman plant weighs about a ton. About 100 spools await the wire cutter. Making 10 million BBs a day takes a lot of material!
Daisy made some upgrades
I haven’t see Daisy’s process; from articles others have written over the years, I know it’s essentially the same. Joe Murfin, their vice president of marketing, told me they installed a new sorting machine a few years ago, and it made a big difference in the quality of their BBs. According to him, it isn’t that their process is that much better, but their sorting is controlled very tightly. I haven’t seen it, as I said, so I can’t comment, but I’ve taken extreme closeup photos of all the BBs and I’ll let you be the judge.
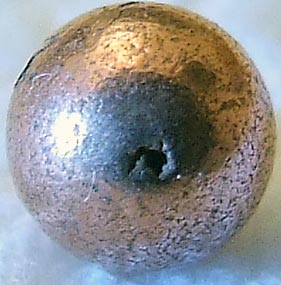
Crosman’s BB looks roughest, and is the only one that has the flat spot (looks like a crater in the center of the BB).
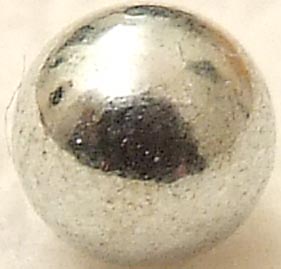
Daisy premium grade BB is smoother, but not without imperfections. The dark spots on the upper left are reflections.
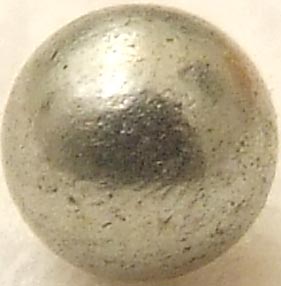
Avanti precison ground shot looks no smoother than the standard Daisy BB. It is unplated.
We’ll test them!
Following the first reader’s comments, there was some speculation about whether or not it mattered that a BB was more uniform. I really don’t know the answer myself, so I thought I would devise a little test to see if there is a noticeable difference. You airsoft guys should enjoy this, because you have the same situation with the BBs you shoot.
This is sort of BB related:
When buying some round balls to try in my Talon SS would you reccommend the black graphitized lead balls or the copper coated ones?
Thanks
Bob,
I haven’t paid much attention to round balls in rifles, other than to shoot some groups. I guess I use the graphited balls most because they are cheaper.
A few years ago I also discovered that the ones I had (Lobos) were also more round. That may just be a box-to-box thing and not really valid.
B.B.
Can you include Gamo steel BBs as well
i see the difference is not as dramatic as i thought. what promtped me to ask was one of the crosman bbs had a large copper flake protruding that stopped it from getting through the bore. i only noticed when i pushed the bolt forward and felt resistence. also, plated items only have a thin layer that is easily scraped off provided you use a hard material like corborundum. it took too much time, so i didnt get to the end of it, but it looked as if you could peel off the copper and be left with an undersized bb. one last thing, i belive the bb and ball bearing industry use the same machine. on “how its made” i watched a segment with how ball bearings were made. facinating machines. if there is a re-run i will be sure to record it.
BB,
Is 16x scope good enough for 1 inch target at 50 yard?
Gamo steel BBs,
I didn’t include Gamo because they are not a major supplier to the U.S. BBs are made in many countries that I didn’t mention, including Russia, which still makes them with old machinery. The come out looking like American BBs from the 1950s.
I would guess Gamo makesa a pretty good BB. I’ll have to try to locate some. Did you notice that Marksman also sells a BB under their name? I don’t know where they source them, but they might be interesting, as well. Remington BBs are made by Crosman.
B.B.
A 16 power scope is fine for one-inch targets at 50 yards, as long as the center of the reticles is thin enough. Thick reticles will cover most of the target, if it’s only one inch.
B.B.
Just responding about the GAMO bbs. They are the most accurate in cheaper Daisy BB/ pellet combo. This is my knock about, play with gun. Crosman were last, and daisy second. I usually shoot pellets but tried bbs.
-hb
yup,that flat spot is what i would call as pitted in my posting.Some of my bbs hace circular indents like a fingernail indent,almost like an arc..
Could anyone offer a sugggestion for this? I have the 6000 BB Copperhead “New Easy Pour Container”. It is the 2nd one I’ve had. No matter how I cut the tips, they are anything BUT “Easy Pour”; in fact, just the opposite! Am I doing something wrong, or is this just false advertising on Crosman’s part?
Any help appreciated, and thanks, because it takes quite a bit of shaking effort to get even a small amount of BBs to come out of the container.
-Joe
Joe,
Isn’t it amazing that round spheres will jam together like that? In industry, they vibrate the containers to prevent the jamming. Crosman isn’t to blame – the laws of nature are. Compared to other kinds of BB containers, these really are easier!
Maybe the 6,000 size is just too large to manipulate in one hand like the smaller ones,
B.B.
BB,
It was just as hard with the smaller size container. I miss the pint-size milk carton containers Crosman used to sell their BBs in. And those straw things you could jam into them to pick up the BBs in a single collumn that could then be easily transferred to various loading ports. That was back when I had 25 students, and none of us wanted to waste time loading that could be spent shooting.
I’ve cut the plastic tip back to the lip that holds the cap closed but I still have to shake the container like mad onto a washcloth, from where I can load the BBs into the ports by hand (right now, into PPK/S magazines mostly…they’re my current passion).
Anyway, thanks for the commiseration.
-Joe
BB, 6-14-08
I have a 30X microscope. I compared the new Daisy Ultra Smooth BBs to a new box of Crossman premium BBs. The new Daisy BBs are vastly improved over your image and the Crossman BBs show no improvement. Daisy needs to be applauded, because their BBs are as smooth as ball bearings and their heavy, soft, zinc coating, is even easy on rifled barrels. No other manufacturer even comes close to the quality of a Daisy BB.
Greg Drozd
Greg,
I will take a Jeweler’s Loupe to Wal-Mart and examine the latest Daisy BBs. If they are as nice as you say, I will blog them.
B.B.
When I bought my s&w mp airgun, there was a bb inside the hole up of the trigger. It seems funny but i dont know how it got in there, gun was first-hand, then i pull it out by shaking the gun and that was the best bb Ive seen and Im still keeping it, I rubbed it to wall and there is no even a scratch. Surely its not plated and its steel. I used crosman and daisy bbs but there is no bb like that. I dont know what brand it is but I realized that there is perfect bbs on earth 🙂 and if I find I surely will order a 6000 pack
Anonymous
Sounds to me like a ball bearing the same size as a .177 BB. Ball bearings are made to very close tolerances, BBs are not.
are crosman copperhead bbs better than daisy steel bbs?
Julian,
No. It's just the opposite. This blog contains at least 50 BB-gun tests in which Daisy zinc-plated BBs are shown to be more uniform, faster and more accurate than Crosman Copperheads BBs.
B.B.
It’s the end of 2014. Are BBs still made the same way or are they more refined? I would have figured “precision” BBs would be made to more exacting standards than just metal wire made into a ball and coated. That’s downright caveman technology! 😀
Jared,
And how would you make them? Yes, they are “still” being made the same way they always were and yes, they are more refined. To make it clear, wire is cut into chunks that are then rolled until they are perfectly spherical. The way they get them so incredibly uniform is through a high rejection rate.
BBs are made by the millions during each 8-hour shift. So there aren’t many opportunities to use high technology to make them better.
Today’s steel BB-shot is extremely refined. It is almost to the standards of ball bearings, which is where the steel BB started, back in the 1920s.
I will be testing a new type of BB beginning very soon — maybe next week. That will give me a chance to discuss BB production and advancement.
B.B.
Flight of Fancy
A tungsten core with a teflon coating… coating thick enough to be safe to even a rifled barrel. Soon to be followed by a BB gun with rifled barrel designed just for this new BB (and with a warranty voided if used with regular steel BBs)
Not sure if magnetic probe tip on a repeater bolt would be functional — but if designed just for these BBs, one doesn’t need the open receiver of, say, a duel ammo 953.
I have several BB and pellet rifles and pistols but I enjoy shooting my Red Ryder the most because it is so simple to load and shoot, shoot, shoot! However, I seem to have “over-oiled” it, because the BBs are having a hard time getting into the doflatchie that lines them up to shoot. What’s the best way to clean this mechanism out? Can I pour gasoline or gun solvent into the oil hole? Any other suggestions? Thanks!
Fred,
Welcome to the blog.
Don’t put solvent into your gun!
Take the shot tube out by unscrewing it and dry it off. The dooflatchie is a gravity-feed channel that’s in the base of the shots tube.
The oil you put through the oil hole shouldn’t cause any more problems.
B.B.
BB Thanks,
But how do you “unscrew” the shot tube? It’s a fairly new Red Ryder and the end of the barrel is indented rather than capped like the old ones. There appears to be a square “button” near the top but I’ve tried to push it in but it doesn’t seem to budge. If I can poke something hard against it, it might move. Then what, try to turn it or try to pry it out? Thanks,
Michael
Michael,
Press in on the loading door firmly and slide it towards the bottom of the barrel and when you get it open just start dumping in BB’ s
Fred,
Okay. You didn’t t6ell me that in your first post.
On the new Red Ryder the shot tube doesn’t unscrew. So your only alternative other than complete disassembly is to shoot the gun dry. It will take time, but there are no shortcuts with that kind of gun.
B.B.