by B.B. Pelletier
Reclaiming lead from used pellets
Part 1
Before we begin today, I want to alert you to a HUGE price drop on the RWS model 52 sidelever. If you’ve ever contemplated buying one of these, now might be a good time! The Striker Combo is an especially good deal at this time.
We began this report on casting bullets yesterday. Today, I’ll finish and show the results.
When the metal is ready, the cast iron bullet mold must be brought up to temperature. I start by sticking a corner of the mold into the molten metal for a minute, then I begin casting. It takes about 15 bullets before the mold is warm enough to cast a perfect bullet. From that point on, casting goes on continuously for as long as I care to work, or until the metal runs out.
The furnace I use has a spout on the bottom from which molten lead will pour when a valve is opened. With many molds, you can hold the mold up to the spout and fill it perfectly with little wastage. However, with the particular mold I’m using today–a 370-grain .439 caliber bullet for the .43 Spanish rifle cartridge–I have to pour the lead in from a distance. So, the mold is held below the spout about a half-inch, and the lead is allowed to pour in until it puddles on top of the sprue plate. Every mold will be unique in this respect, though I often encounter this characteristic.
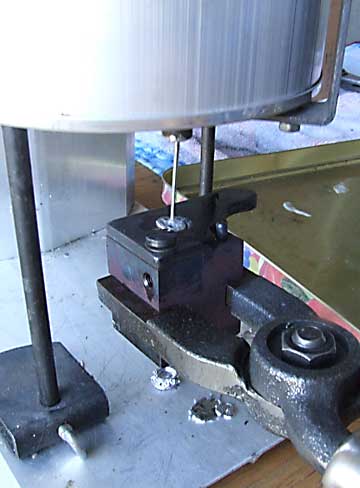
Safety first!
Though I want to move through the steps rapidly, the newly cast bullet is still hundreds of degrees and cannot be touched. I have to do things to avoid touching it. When the metal has hardened in the mold, which takes 5-10 seconds per cast, I cut off the sprue by striking the sprue plate with a plastic hammer. Then, I open the mold and strike the handle joint with a plastic hammer to dislodge the new bullet.
Once perfect bullets start coming, the rhythm of casting allows for 3-4 bullets a minute. After that, I stir the pot every 5 minutes and flux with more beeswax every 15 minutes throughout the casting session. If I’m motivated, it’s possible to cast several hundred perfect bullets this way in a couple of hours.
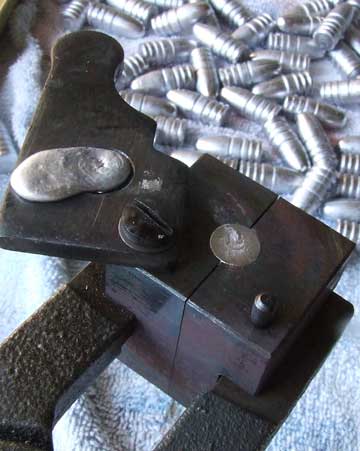
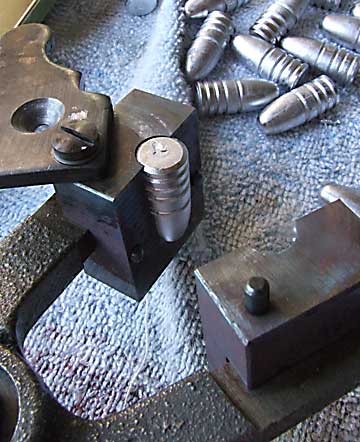
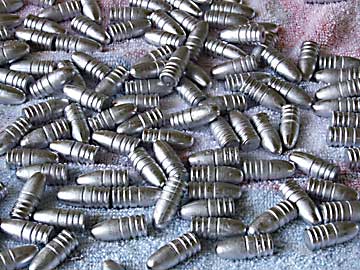
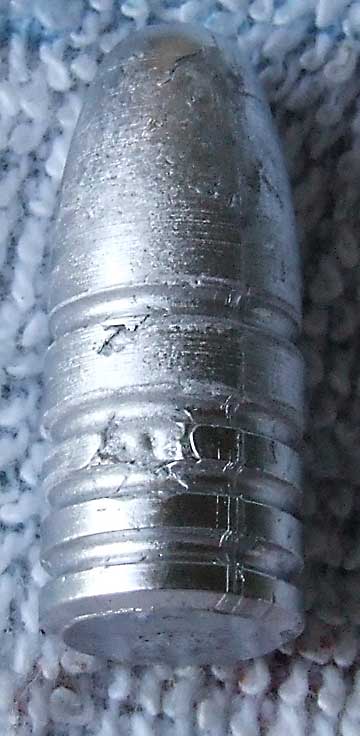
Afterward
I always put the mold away with a bullet in it. That way, the inside of the mold will never rust.
Inspect every bullet ruthlessly. They should be as close to perfect as you can make them. Look for voids in the base of the bullet and also look for driving bands that are not filled out perfectly.
This is the one thing I can’t teach, because every cast bullet will have imperfections, if you look hard enough. An anal person is going to reject most of the lot, while the slacker will wind up shooting fishing sinkers.
As for me, after I am finished with my rejections, the bullets you have seen me cast here will shoot into a 1.5-inch group at 100 yards when I shoot off a rest with military open sights. That’s all I am after. I rejected about 25 percent of the bullets seen here.
Video article
Because this process isn’t easy to explain, Edith also filmed me casting. I’ll write an article about casting bullets and include a narrated video that should explain things clearly. I’ll try to get it out this month.
B.B.
You do a good job of keeping the process clean.
Everything gets pretty dirty when I pour.
twotalon
Twotalon,
I'd say that is due more to tight shots and a careful selection of photos. I'm messy, too. But I try to keep the sprue in one place and under control. That helps with the cleanliness and I occasionally dump it back into the pot.
That large flat metal tin that shows in Part 1 is the top of a cookie tin. I knock the sprue into it, so it's in one place.
B.B.
B.B. said, "anal person"
Hello,BB
Is there i type of test i can perform
to see if my Diana Panther 34 has
barrel droop or not?
(I dont want to buy the wrong Leapers base.)
Sorry for all the questions about the Diana 34 Panther.
Cougar94
Cougar94, that's a tough one. Do you have an airgun scope with regular mounts to try it with? Do you already have a scope w. mounts (even cheap ones) that you can try it with?
I would think that you should be able to establish the severity of any droop with only a few shots… set the scope in the center of its elevation adjustment range and see where it hits relative to your point of aim.
Not sure of the best distance to test it at, but I'm thinking 10 yards would suffice.
B.B.,
I'm not trying to be an anal person but in your third paragraph you say,
"It takes about 15 bullets before the mold is warm enough to cast a perfect bullet."
I think you meant to say "15 minutes".
Since a novice could misconstrue this to mean start pouring into a cold mold for 15 bullets to heat it could be a safety issue. Don't pour into a cold mold.
kevin
Kevin,
No, I did mean 15 bullets. After 15 bullets have been cast, the mold will have absorbed enough heat to cast a good bullet. That is with this particular mold. With others, the number of bullets you have to cast varies.
As for preheating the mold, I did mention sticking a corner of it into the lead before starting to cast. The video will show that as well.
B.B.
Cougar94 ,
Barrel droop is the angle of the barrel relative to the angle of the scope base on top of the gun. I know of no way to determine the amount of barrel droop without mounting a scope.
Sorry,
B.B.
B.B.,
Sorry.
I'll get another cup of coffee.
kevin
Wow, what a process,
Thanks B.B. for the tip about lengthening the base of the pump for my discovery. What a difference in pumping ease!
All the information on lead pellets was really helpful. I am going to try some and will post some results as compared with the Dynamics PCP2.
Just finished mounting a scope, thanks for the great articles and videos B.B.
This blog is an incredible resource and just plain interesting to read.
Wayne, I am in Portland, is your range visible from I-5 (I think it used to be a golf driving range?)?
Beth
Beth,
I'm glad the bigger pump base worked for you! We all would be interested in a third party report on Wacky Wayne, MD. :).
Take care,
Mr B.
Wayne,
Congradulations on your 3rd place tie in Washington.
B.B.,
Congradulations to you also. Your student has done very well in just two(?) years.
Mr B.
Have you casted pellets? What would be the reason not to make your our pellets?
B.B.
Does jacketing bullets in various alloys like we see in factory ammunition just control expansion upon impact or does it affect flight characteristics?
Herb, an image search on Google for "normal distribution curve" turns up many with definite boundaries. There may be versions of such curves that go on to infinite, but in place of a terminus, they have inflection points that drop the value to almost zero, and these regions seem irrelevant to any practical shooting situation.
You're right that all the causes you mention could make someone miss a garbage can lid after 85 years, but those are all physical causes that we know from the outset are not described by probability anymore than the behavior of weighted dice. I take it that all the advanced mathematical techniques are designed to get a higher sense of probability so that one can discriminate what behavior is due to probability and what is "statistically significant" or due to physical causes. But the physical world is so complex that you can't know all the forces. So, after a certain point it seems to me, complicating the statistical model becomes reminiscent of Alice in Wonderland where the faster you run the further behind you fall. It's good statistics, but the practical returns diminish.
The radial standard deviation is an application of the bell curve where the mean is the center of the group and the extremes are the outside edges. It is the model used by the Aberdeen Proving Ground which has access to all sorts of high level tools–the Calculus of Residues, complex series approximations…. It's intense. Their idea makes sense; they pack heavy gear; and they have me persuaded.
For the 30 shot group, you're right that an average of such is not the "real" average if there is such a thing, but it's close enough for me.
Alan, bring on your ideas. I suspect that my goal is much more modest than yours. I just want a practical rule for relating groups of different numbers of shots other things being equal. This particular question removes most physical causes automatically since, for example, a loose sight for a 5 shot group will be loose for a 10 shot group. It should have no effect on the expansion between the two. Just about the only thing that does is the normal distribution. Looking at the bell curve, the shape suggests that growth between the mean and the extremes is mostly linear from which I conclude that for all but the very small and the very large groups up to 30 (or thereabouts), the growth in group size is mostly linear. But I would be interested in significant changes to this picture.
Matt61
Beth,
I would like to take the credit for helping you with the pump, but I think someone else told you that tip.
B.B.
Mr. B.,
I consider Wayne my Padoin learner.
B.B.
Matt,
Please contact me off line at my yahoo.com e-mail address hcacree
I'll be glad to try to explain the statistics to you. I'd be willing to arrange placing a phone call to you and discussing it interactively, which I think would be a lot more fruitful for you.
If you just want relative factors, I think Table 1 in the following article will give you the corrections. The absolute correction factors are adjusted for 1 MOA, but if you take ratios, the adjustment cancels out.
http://www.the-long-family.com/Group%20size%20statistical%20analysis.pdf
Regards,
Herb
PS – If anyone else wants to work through this, I'll be happy to discuss it. Contact me at my e-mail address.
Andy,
No, I haven't cast pellets, but here is the reason to not try. Casting works well enough for bullets at the scale I am casting. But down at the pellet size casting isn't precise enough. At that small a size, the metal should be forced into a die and extruded out a weep hole–something called swaging. There are far fewer voids and balance problems with swaging.
B.B.
On the subject of the natural shooter, I have been wondering if part of their capability lies not in shooting talent per se but in attitude. Namely, they don't care about the result so they don't get uptight. I suspect women generally do not have the baggage of most men of being crack shots etc. so they can relax. The individual from my Dad's army experience was considered a wimp and couldn't have cared less about his score so long as he qualified. All the more infuriating when he broke the range record. But his pose of indifference was not the sign of genius. He really did not care. He he.
Nancy Tompkins says that you must cultivate a modest level of excitement that is not too extreme, and that correlates with a psychology lecture I heard in medical school where a professor said that optimum behavior is correlated with a medium level of anxiety–not too much, not too little. This is sort of common sense, but it was graphed and explained in a memorable way–alas one of the few things I took away from that experience.
Otherwise, Nancy Tompkins' mental advice correlates very well with David Tubb. Visualization is a very big deal. Also important is focusing on each shot without worrying about anything else. Here, I think, lies the answer to B.B.'s question about how to go from 15 good shots in a match to all 60. There is no 15 shots and no 60; there's just the one you're shooting. It's like the zen koan:
Q. If a goose is in a bottle, how do you get it out without killing the goose or breaking the bottle.
A. There. It's out.
Ha ha ha. Obviously, this is easier said than done.
One point of her's that is new is that one concentrates on slowing down the shot process. For standing, she claimed that at first she could barely hold the black, but by slowing down every part of the shot process, she was able to shoot 10s.
I think David Tubb is doing the same thing by focusing on the details of his shooting routine and repeating them exactly. It's like a saying from another context that I like very much: Subdivision increases productivity. By concentrating on simple parts of a routine, you end up pouring more mental intensity into a shot than a single heroic effort at the whole. It worked well for me last night.
Matt61
Matt,
Bullet jackets do several things. First, they resist heat from the burning powder. Second, they hold the rifling at higher speeds. Third, they lend themselves to high-speed production.
Lead bullets can be nearly as accurate as jacketed bullets, but to be so they must be handled with kid gloves. Jacketed bullets are armored, so they will work through repeating mechanisms without damage.
B.B.
Beth,
Wow, how cool your in Portland… My son and daughter live there in the big city too.
The golf course is still there, it's on the other side of the freeway.
As your going south, we are on the right, but there is no exit getting off going south at exit 11, (take 14), you can only getting on to go south or get off going north, which is when you can see our range by looking to the left as you get off..
So, come on down on Sunday! We have two new Marauders with beautiful custom field target stocks to try out.
Come take my Oregon state champ hat from me!
Wacky Wayne, MD
Ashland Air Rifle Range
Cougar94,
click on this link to take you to the Yellow Forum and a fix for RWS34 barrel droop. I'm not telling or suggesting you try to fix your barrel droop in this manner as I don't know your skill set, but you will be able to see in the photos the author posted how you can determine if your rifle has barrel droop. Perhaps mounting a straightedge ruler on the receiver of your rifle will give you some indication?
http://www.network54.com/Forum/419052/message/1203813573/Barrel+droop+fix+by+Scottg%2C
I personally have three RWS' and have mounted the Leapers scope mount to two of them (Model 52 and 350) and was very satisfied with the results. I just ordered the mounts suggested on PA's website.
Good Luck!
Fred
Wayne, I had posted a congratulatory message to you this morning but unfortunately it went on yesterday's comment section. So as you are monitoring this comment section currently, let me say again congratulations on your third place showing!
I'm sure I speak for most of the blog when I say we're all proud of how you did.
Fred
B.B.
Interesting about bullet jackets. I can see how the cast lead is mostly for the single shot crowd and probably lower velocities.
My Walther CP99Sport (part of the Walther Nighthawk package) broke last night! After a shot, it felt like the trigger didn't return entirely to the original position. I can't push it any further forward, but there is no engagement and no tension when I pull. I tried dry firing with and without an empty magazine; removing the powerlet and replacing; rapidly pulling the trigger and nothing. All I can think to do is dump a bunch of Ballistol down the trigger mechanism and see if that does anything. How is the Umarex repair service?
Matt61
matt, hmmm, this has me a bit worried. I have the CP99 and every once and a while after pulling the trigger it doesn't return on it's own, but I've always been able to get it back to normal by jiggling it…hope it's not a portent of things to come.
On the other hand I had a jamming problem with my Umarex PPK a month or so ago. Sent it to their repair depot and it was back within two weeks, good as new. The fix (it was off warranty) and shipping charges came to less than $35.
CowBoyStar Dad
Matt,
Umarex has a great reputation for good service. I would trust them.
B.B.
B.B.,
hey, i have a pressing concern for my Beeman SS1000-S that i always mention. i was shooting for a while the other day, and just as a test to see how the rifle was performing, i ran 1-2 of my old Gamo PBA pellets that we all try when we're new airgunners because we were misled by the manufacturer to believe they were useful (mine are the 5.0 grain ammo that ACTUALLY worked…. sometimes…) and i knew that when i first bought the rifle, these pellets always cracked with that supersonic sound we all know. well, when i shot them through this past time, to my disappointment… no crack…
i am worried that the gun is losing power. i checked the breech seal for nicks, and i figured it was a bit dry, and i saw on your SS1000-H review that the guns have leather seals and i should coat it with corn oil. i have yet to try this but i may soon depending on what you think. i flipped the breech seal over to find a clean other side of the breech seal, that still has some oil on it from the factory, but otherwise was identical to the other side. i fear that it is not the breech seal that is the problem. i fear either my spring is losing power, or my spring head is losing its seal, because i remember very well the old crack of Gamo PBA pellets, and it is no longer there. i really need a Chrony and i'm thinking about getting one soon, but for right now, i think the PBA pellet test is good enough to tell that this rifle IS losing power.
on to the main question… what should i do? i'm thinking about sending it to Beeman to get a supertune or something to that nature. but is there anything else i should do? i do not have the proper tools to take the spring out of the gun.
and finally, does removing the stock on your gun void the warranty? i know it says to send it to Beeman for major maintenance operations, but simply taking the stock off to wipe the parts clean doesn't void the warranty… right?
oh, i just remembered. i forgot to post my name. the comment above me is from John W., as is this one.
John,
Slow down and take a deep breath.
I wouldn't recommend getting a Beeman Supertune on this model rifle. If it were a Weihrauch, then perhaps, but not this one.
Let's not use corn oil on this rifle just yet. Do you have any silicone chamber oil? That's what you should use.
You may either need a breech seal or you may need a new mainspring. It sounds like you have lost power–BUT!
The speed of sounds changes with temperature, barometric pressure and humidity. Maybe your gun is still shooting the same, but today maybe the sound barrier is 40 f.p.s. faster than it usually is where you live.
This is why you really need a chronograph. Because without one you can't tell much.
However, how does the rifle shoot? Is it still accurate? Has it become easier to cock recently? Is it smoother shooting?
Vince, you know this rifle. What have I forgotten to ask?
B.B.
Mr.B, Fred & All,
Thank you very much. I'm doing it for the "gipper" or was the kipper?
anyway, I'm having loads of fun…
and that's what counts.
Wacky Wayne,
Ashland Air Rifle Range
Wayne,
LOL, I think the championship hat is where it belongs. I am actually in Molalla on 40 acres… I do travel south for the winter, which is why I remember the spot so well. I got tired of the i-5 drive and now go through the high Sierras, it take me 21 hours instead of 19 but well worth the extra two hours.
I hope someday to make a stop at your range.
Beth
B.B.,
well, right after i posted my comment, i went out shooting, to pass some time and to see where i've gotten. as far as the rifle shoots, aside from being very sensitive to hold (i sight in, shoot my Gamo Rocker pellet trap to see if i can hit it, and when i miss, i go back to paper to find i had changed hold from the sight-in… i'm still, even after almost a year, getting used to keeping a steady cheekweld and a good grip.), it shoots great. when i do my part and don't deviate on my hold, i can make groups covering a nickel. as for cocking, it really hasn't been any different since i first got it, other than a type of callas on my thigh from setting the butt on it to cock, and the stronger arm. it is smooth to cock, and it is quite easy, but it was from the beginning. so cocking hasn't really changed either.
and as far as the sound barrier goes, that just may be it!!! when i last tested the PBA Raptors it was 60 degrees at most, and right now it's about 85 degrees and very humid. i think you may be right. i think i will be getting myself a chronograph very soon for the record. however, i kinda feel that this rifle still isn't as powerful as it should be. as a 1000 FPS rifle, it still kinda seems like an underdog in power, putting .22 pellets barely through a 3/4 inch board. (ok maybe not barely… but they struggle to pass through 1 inch of solid wood, which i expect a rifle with 1000 fps in .177 caliber, and 800 fps in .22 caliber with light pellets, which i'm almost certain is possible with a good gun and RWS hobbies, i kinda expect a bit more power.)
as far as RWS chamber oil, i do have some laying around from my .177 shooter's kit. so should i take my breech seal out and soak it in chamber oil, or should i wait for Vince to answer?
Cheers,
John W.
John W, it's tough judging power by wood penetration. And a .22 is not going to penetrate as well as a .177 out of the same type of gun. Really wish you had a chrony…
In any event I'm more inclined to believe it's the piston seal if not the spring. For some reason the piston seals in some of these guns sometimes tend to be a bit loose. I really don't think it's got a leather seal, Shanghai (the manufacturer) uses basically the same seal as the Norica they copied. Soaking either it or the breech seal won't accomplish anything.
Sounds like you first really need to establish that you've got a problem. Let us know how you make out when you get a chrony. And forget those stupid Raptors in this gun.
B.B. and Vince,
yeah, i'll certainly buy a chrony soon, and i will update on my findings.
and thanks for putting up with me… i'm still kind of a noob to airguns and i'm learning, but sometimes i can make stupid calls. i'll be sure to update what i find with my Chrony when i get it, and hopefully, it'll just be me always wanting more out of my gun.
and one more thing… my Beeman is very sensitive to hold like all springers, but not in the way i'm used to hearing about. it does not change your group size if you change your hold (unless you try to rest it on a bench or something like that, which ruins accuracy in EVERY gun), but when you deviate even very slightly from the hold you originally sighted in with, your point of impact is lost and long gone. is there any faster way i can teach myself to hold the rifle the same way every time? it gets very frustrating to sight in on a dead bullseye on the target, then put a new target up to plink on (such as a silhouette trap or something), then start missing the targets completely because even though you aim center reticle, your cheekweld is different, or you're holding the gun a tad tighter than when you sighted in (happens when you switch from rested to offhand, to me.)
sometimes the difference is made just from cheek placement, because apparently i'm putting pressure on a slightly different part of the stock (it's not my scope… my Center Point scope has barely any, if any parallax), and it'll move the pellet as much as an inch. i need to know a way to pick a hold then repeat it, and i want to do it with as few pellets as possible, as Kodiak pellets are out of stock (i know from experience that when Beeman pellets go out of stock, they can stay out of stock for a while.) and i'm on my last tin. (that tin is 1/5 full)
thanks for all the help,
John W.
and P.S. i'm probably gonna buy my chronograph when the Kodiak pellets come back in stock, so i hope they come back in stock quickly!
John W,
I'll be a nudge and ask…
What kind of scope do you have?
I replaced the 4X scope that I had with a variable power, up to 12X with AO. Using higher mag and focusing with AO gives you a very narrow eye position behind the scope. It forces you to a better defined cheek weld. If you're off, the target is out of focus. You then have to move your eye position/check weld to get target back in focus, you don't readjust AO.
Herb,
yeah you do have a good point. i'm using a Center Point 4-16×40 scope and to make matters worse, i know Center Points have very picky eye relief to begin with. but yeah i didn't know that high magnification was the reason for that. i normally keep a good cheek weld, but it's never perfect. i normally adjust AO to where there's no reticle movement from head movement, then adjust my eye to the eye relief to the scope. but i think you have a point the 16 power may be playing games with my eye. i tried the 4x scope for one day just because i was curious (i bought the Center Point with the gun), and i didn't really have any problems with it, surprisingly. there was a little parallax, but not bad. probably because it barely magnifies, lol. i didn't keep it on for long at all, because i could not focus at 50 yards, which is often my range of plinking (i like a challenge.).
i expect to have further problems with magnification when i get my 6-24x50AO Leapers scope (for my Benji Marauder) for Christmas. i imagine you can barely move your head at all with that scope without running into pitch black.
but thanks for the tip and the eye-opener… if you will. i hadn't thought of that before. i'll watch for it next time i go out… but that'll have to be tomorrow because at this time it's pitch black at night.
John W.
HI all
I read a post on the Yellow the other day
that made me curious,so I tried it out
and now I want to share it with everyone.
The post was about an AO cheat on cheap
scopes (which is all I buy) that you all
may already know.If not here goes:
Once you get your scope pretty close to
sighted in,the poster said you can then
remove(or just loosen)the ring on the
front bell of the scope to get at the
threaded ring just inside the bell.
If you turn this ring it moves the lens
in or out to change focus.
What I did on my Daisy Powerline 3-9×32
was set it at 4x, and adjust the front
ring until I had a clear focus from ~10
to just past 30 yds.then still at 4x I
used the focus on the rear bell to
sharpen up the image to the point where
twigs and blades of grass were very
sharp and clear at min. to max. yds.
My intent was to not have to refocus
all the time but I found an extra bonus
that the I didn't notice the poster
mentioning.
What is neat is that with the 490 the
POI stayed the same if I used the mag.
at different distances.Starting at 3
below 10 yds.then 4 at 10 and so on up
to 8 at 30 yds. I'm zeroed at 30'then
POI is high to about 23/24 yds.where
it's back on then POI is low past that.
But,if I increase mag. with dist.then
POI is much less affected.To the point
that my usual targets(pop bottle caps)
are within POI by no more than the
height of the cap laying on it's side:)
I'm sure more powerful guns will react
different but for low power plinkers
this works great.I'm gonna try it on
my 953 that has same kind of scope next.
I guess some of you are thinkin:
Well no kidding Sherlock.But this was news to me and I hope it helps those
that are scope dummies like me.
To all of you with the really nice
scopes that don't need this kind of help
I'll just give ya the RASPBERRYS :^O/:)
HAPPY SNIPIN
JTinAL
John W.,
While Herb is right about a high-powered scope fixing the head placement problem, there is a cheap mechanical way to do it. Place a piece of rough tape on the stock where your cheek touches it and make certain that you always touch the tape the same way.. That will ensure your repeatable head placement.
B.B.
John W.,
While I agree with Vince that wood isn't a good substitute chronograph, something like duct seal can be pretty revealing. But only if you knew how deep your rifle penetrated when it was in good shape.
B.B.
B.B.,
ok, i'll try that! that may just work. sounds interesting. i'll try it on my next outing.
B.B. again,
alright. i'm not so worried about penetration, although it is an interesting subject, now, because i'm ordering a chronograph with my next order with Pyramyd.
thanks for all the help,
John W.
BB,
I am surprised you did not mention aluminum molds here.
They are:
1. Way cheaper.
2. Don't rust
3. Heat up quicker. Usually less than 5 bullets to get good ones.
4. FAR fewer rejects. Better than 95% of all the bullets I cast are good.
5. Lighter weight so much easier to hold and maneuver over long casting sessions.
I have cast more than 100,000 bullets in my life. During my early years there were nothing but steel molds available.
Once I bought and used my first LEE aluminum mold, I got rid of ALL the steel molds.
The only disadvantage to aluminum molds is they are slightly less durable than steel. But you will have to cast way more than 10,000 bullets with one before that becomes an issue.
And the price is SO low you can simply replace it.
The advantages of aluminum FAR out weigh having to replace a mold occasionally. I have only replaced two in my entire life.
pcp4me,
I didn't mention aluminum molds because this tutorial wasn't about molds. I use aluminum molds, too and I like them just like you. I don't find them to be better than cast iron, though. If I have a choice, I buy iron, but aluminum is more affordable and can be just as good.
As long as I store my molds with a bullet inside, rust isn't a problem.
B.B.