by B.B. Pelletier
A reader asked for this information, and I expect that many of you are curious. I’ll talk about the basic design of a pneumatic valve, and everything I’ll cover applies to CO2, with a few modifications I’ll mention
This is a knock-open valve
The most commonly used air valve in airguns today is the knock-open valve. To operate it, a valve stem is struck by a weight called a hammer that is driven by a spring. The inertia of the impact moves the valve stem in the same direction. There is a synthetic valve face on the valve stem that holds the high-pressure air (or CO2) inside a reservoir until the valve is open. A valve-return spring behind the valve face starts the valve moving back toward the closed position after the valve has opened as far as it can. Once the valve stem starts to return to the closed position, the pressure of the air or gas in the reservoir also pushes on it. That’s because the pressure inside the channel of the valve body is always a little lower than the pressure in the reservoir. If it weren’t, the valve would remain open longer, dumping a lot of the air in one shot. The little valve-return spring exerts a huge controlling force over the valve because of this pressure differential.
Let me illustrate…with gross exaggerations!
The following illustrations show huge clearances inside the valves, when, in fact, they’re really quite small. Clearances are one place where pneumatic and CO2 valves differ. CO2 gas is a molecule of two oxygen atoms bonded to one carbon atom. It is relatively large compared to the size of oxygen, nitrogen and other gas atoms found in air. CO2 flows slower than air and needs a larger passage to go through. Let me put that a different way. If you were to shoot a CO2 gun filled with air that’s pressurized to the same pressure as CO2 (about 853 psi at 70 degrees F), it would be significantly more powerful.
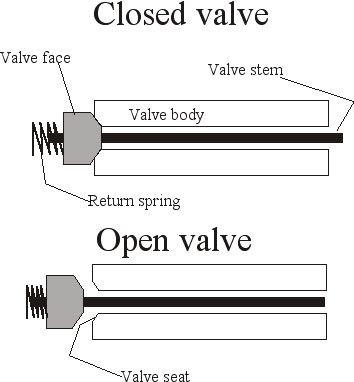
These two illustrations of the cross-section of a pneumatic valve illustrate how the valve works. The other parts of the gun (reservoir, barrel, hammer, etc.) were left out for the sake of clarity.
Many variations of valves
The illustration is of no specific valve. It is just a representation. AirForce Airguns valves, for example, have a hollow valve stem through which the air flows. Rather than attempt to show all the different styles of air valves, I wanted to show just one simple style to give you the general idea of how they work. I left out the hammer and hammer spring, which would be on the right side of the valves shown above, and the reservoir, which would be on the left side. I didn’t show how air gets from the right side of a valve into the barrel, but it is done through a passage called an air transfer port. Any other places where the air might go are sealed with O-rings.
How the valve is designed and set up determines performance
Looking at the illustration, you should realize that the longer the valve remains open, the more air will flow through it. You can affect how long a valve remains open by the strength of the return spring, the pressure inside the reservoir, the length of travel of the valve stem and the inertia of the hammer. There are limits, however, which is why you don’t get an increase in power beyond a certain point when you install a heavier hammer or a stronger hammer spring.
On the other hand, Tim McMurray still makes a rifle called the US-FT that gets filled to only 1,800 psi at the most and still delivers 60 Crosman Premier 10.5-grain .177 pellets at nearly 900 f.p.s. before the pressure drops by only a small amount and the gun needs to be refilled. The secret with this gun is a well-balanced valve that doesn’t require raw pressure in order to function. McMurray substituted dwell time for the extra pressure, to extract all the performance the air has to offer.
So there you have it, sports fans – the design of a valve. They all differ somewhat, but the underlying principles are the same.
It would be interesting to know exactly what is involved in re-sealing a pneumatic air rifle or pistol.
Will it damage a pneumatic gun like the Gamo Compact or Baikal IZH-46M if they are fired without a pellet? I know that spring air guns can be damaged, what about pneumatics?
Dennis,
I can talk about seals in general, but each gun is different, with different sealing needs.
B.B.
You can shoot the IZH 46M without a pellet and not damage the gun, but why do you need to? The gun has a dry-fire capability built in and does not have to be pressurized to shoot. Simply lift the top breech cover until the gun cocks, then press it down until it latches again. There does not need to be air in the gun for the trigger to work.
B.B.
So how does a Daisy valve work? I noticed you can hear air hissing out the muzzle if you pump it uncocked. I have a 22SG.
BTW do you think they may throat both ends of the barrel to speed assembly? I don’t know if it’s a defect and don’t want to pay shipping costs to find out.
Daisy has designed their valve so that it’s necessary to first cock the gun. The air comes out because the hammer holds the valve open.
B.B.
Throated barrels,
What are we talking about?
B.B.
BB,
I like your discription of the pressure difference affecting the valve. Maybe this is the explanation why some guns deliver less shots when a (legal) silencer is installed.
Do ancient airguns have the same kind of valve construction?
Markus
Markus,
The old big bore airguns from the 1600s to the 1900s used both impact valves like the one shown above and timed valves that employ a cam to positively hold the valve open for a long period of time. I have seen a gun pressurized with only 800 psi, yet it shot 28-grain pellets at nearly 800 f.p.s.! The secrets were a timed valve and a very long (36″) barrel.
B.B.
B.B.
I was wondering, can you dry fire an Airforce Condor? Thanks,
lama
BB,
Am I correct in assumming that there must be some form of seal on the valve stem at the hammer end?In a typical pneumatic valve does the valve stem pass through an o-ring or is there some other form of seal(eg a rubber gaiter)? If the stem passes through an o-ring are there problems with friction and wear as the stem moves through the o-ring.
I have been following your blog for some weeks now and it brings back happy memories of my boyhood air-guns. Many thanks.
Terence
BB, you said. “Let me put that a different way. If you were to shoot a CO2 gun filled with air that’s pressurized to the same pressure as CO2 (about 853 psi at 70 degrees F), it would be significantly more powerful.”
This makes me wonder if it is conceivable that a company could manufacture 12 gram sized powerlettes filled with compressed air rather than co2 and give shooters more bang for their bucks. Probably unrealistic but I wonder…
Lama,
You can dry-fire a Condor, biut AirForce recommends that you always have a tank that has air in it attached to the gun.
B.B.
Terence,
No, the valve stem is not sealed in any valve of which I am aware. AirForce tried to use a seal in their stem and they found it caused too much velocity variation from the friction.
As a result, ALL airguns do puff air from the valve seat. Because of the exposed valve stem, you can actually feel this in an AirForce rifle, while most of the others have their valves tucked inside the receiver, where the air blast gets redirected.
B.B.
jim,
The problem with doing what you suggest is that air flows so fast that you would only get a single shot from a 12-gram powerlet. And if the air were pressurized much higher, say to 2000 psi, the valve wouldn’t work – it would be locked.
CO2 works so well because it is stored in the powerlet as a liquid that flashes to gas, increasing in volume by almost 900 times. So it acts as a pressure regulator, because when the pressure reaches the max for the temperature, the remainder stays liquid. When the next shot removes some gas, more liquid converts.
B.B.
Don’t you risk shooting any air pistol without a pellet when you are testing and adjusting the trigger pull? The dry fire is not a valid test for the 500 gram ISSF test.
I do not dry-fire any gun that doesn’t have that feature.
I have only competed at the national level, so I haven’t shot under ISSF rules, but if that is true, one shot, while loud, isn’t going to hurt anything, as long as the gun is empty.
At the national level, the dry-fire device has been used at every match I’ve attended.
B.B.
I know this is off topic but could you do a review of the RWS c225/ Reck police pistol. I would be interested in your opinion
BB,
Without having to impose to reveal any trade secrets, will you please discuss how do Mr. Tim’s valve differ from the rest? How can his USFT valve be so efficient at such low fill of air?
Dave
RWS C225,
I used to own one so, yes, I can review it for you.
B.B.
Dave,
I won’t reveal any secrets because I don’t know them. But I do know that to get the performance he gets on low air pressure requires a valve staying open longer. It has to allow more air to pass, but since the pressure is lower, that means the valve has to stay open longer. And it has to continue to adjust to longer and longer as the reservoir pressure drops.
There is no real name for such a valve, but I’ve been calling it a balanced valve.
Annother performance secret is a long barrel. It’s more efficient with air.
B.B.
B.B.
BB,
If USFT valves open for a longer dwell time, how does it account for 55 shots for a loss of just 400 psi of air( you mentioned this in a previous post? Does it follow that the air reservoir tank is huge by normal standards? If so, the rifle could then be heavy too.
If dwell time is longer, it follows that the volume of air let out per shot is more, however, at lesser pressure.
It seems to me that there is a certain volume of air at certain pressure that could consistently provide accurate and repeatable shot each time. I wonder what is this figure.
Dave
There have been several questions about using air instead of CO2 on this blog. Here are the results of an experiment I did with HPA (High Pressure Air).
The basic setup was a 48ci, 3000PSI tank with an 850-950PSI output fed into an RWS 850 AirMagnum (.22 caliber). Eight JSB Exact Jumbos (15.8 gr) and eight Beeman Crow Magnums (18.2 gr) were shot at a target with a dual backstop to get an idea of the power with medium pellets. The range was 20 yards.
The air setup provided plenty of power for the JSB Exacts and seemingly plenty for the Crow Magnums (I will have to pick up a chronograph for a more objective test). All the pellets penetrated the first backstop further than when it was powered with an AirSource CO2 tank. In fact, most of the pellets went clear through (the first backstop was weathered 1/2″ plywood). The pressure in the air tank went from about 2500PSI down to 2300PSI (16 shots per 200PSI drop). Assuming the drop stays linear and pressure stays good down to 1000PSI, a 48ci tank filled to 3000PSI would give you about 160 shots per fill.
DISCLAIMER – High pressure air is dangerous. People have been killed from improper handling of high pressure air. You are responsible for any damage, injury or death cause by your use of high pressure air. It can kill! This report does not to teach you how to convert to high pressure air or use high pressure air. This is just a report of experimental results.
Dave,
Yes, the US FT air reservoir is huge. Because it’s mostly air, the rifle isn’t too heavy, however in field target, most shooters want a gun that weighs more than 10 pounds.
As for you “certain volum at a certain pressure” pondering, that’s what a balanced valve does. There are many sweet spots, and the valve can be built to use only one of them.
B.B.
BB,
As a natural born tinkerer and airgunner, can I adapt this idea of lengthening balancing dwell time in a co2 knock-open valve? Any suggestions how I may do it pls? Is it ok to approach this by adjusting valve spring to lesser compressive force so the valve opens more?
Dave
Dave,
Yes, that is the way to do it. You’ll have to lighten the springs on both sides of the valve.
B.B.
BB,
With a box of springs, I have experimented and found a combination that produced two sets of 0.35 inch groups at 20 yards with 6 shots. At this point, I thought all my dremelling, buffing, and spring search did good. Then I ran low on CO2.
I recharged co2 and resumed testing, but then I was disappointed. My group opened up wide.
What could be wrong? I hope to read your reply before I open my rifle up again.
Dave
Dave,
Maybe you were running on lower pressure before. I don’t know how many times you shot the gun, but if it only had CO2 gas inside the pressure could have been down around 400-600 psi.
I would increase the return spring pressure just a little.
B.B.
BB,
It looks like my best group occured when my rifle had lower CO2. When I recharged, the increased CO2 widened my group.
I shot about 30 pellets for my first test when I got my best group at the end of the run.
I am using a used clutch cylinder spring as my valve spring. Since I do not have a pressure gauge on my CO2 rifle, I think I will just have to count shots as guide for my best group.
Dave
Everyone on this blog seems to know a lot about air pressures and capacities so maybe you could answer a question for me. Besides CO2 are there even more efficient gases a person could use specific to delivery speeds and capacity at a given volume? You say CO2 is a large molecule and good for air guns right? Can you elaborate on how that gas affects the operation of ejecting a projectile vs other gases? And finally, what is the thicknness of a high pressure cylinder and do all air guns use high pressure or can some operate on lower pressures. How small could a cylinder be built and still contain about a cubic foot of gas? Say a cylinder has about a tablespoon of volume and we want to end up with a gallon of gas after releasing it at normal air pressure (15psi) or one atmosphere. And since a gallon represents about 256 times the volume of a tablepoon, would we multiply 256 times one atmosphere to get 3763 psi? So the question is: if we started with a cylinder small enough to have the volume of only a teaspoon, how thick would the walls of the cylinder need to be to contain a gallon of volume at one atmosphere using aluminum as the tank material? Any discussion or comments regarding this would be well recieved at Robhoski@yahoo.com
P.S. – I know it’s somewhat silly to talk about volume in tablespoons vs gallons but it’s just a standard I can relate to as opposed to milliliters or cubic centimeters.
Robhoski,
Have your read the latest blog series Tom Gaylord did on the USFT rifle? It only needs to be pressurized to 1,650 psi, yet it gets over 50 shots of .177 Beeman Kodiaks going 938 f.p.s. That’s pretty efficient.
The rest of your question (s) I will need at least one post to answer. However, the answers are pretty interesting, so I’ll do it.
And don’t think that everyone on this blog understands a lot about air pressure and capacity. I don’t, for one. We’re just stumbling along, here, and happy to help people learn what little we do know.
B.B.
where can a person go to find a puncture valve for a 12g disposible cartridge ?
Puncture valve,
I don’t know what you are asking for. What is a “puncture valve?”
B.B.