by B.B. Pelletier
Guest blogger
Today, we’ll start a new tradition, where I periodically turn the reins over to a guest blogger. We have done similar things in the past, but it was never formal. Now it is. If you would like to write a post for this, please contact me at blogger@pyramydair.com.
Bloggers must be proficient in the simple html that Blogger software allows, know how to take clear photos and size them for the internet (if their post requires them) and they must use proper English. We will edit each submission, but we won’t work on any submission that contains gross spelling or grammatical errors.
Today’s guest blogger is Nick Carter. Nick has his own blog at The Mechanical Philosopher, where he talks about machining, airguns, making the jewelry that he and his wife sell, and his sons. This report was originally posted on his blog, and I asked him to share it with you as our first guest blogger. Now….
Making Plastic Front Aperture Sight Inserts
by Nick Carter
I recently bought a Diana 75 T-01 match air rifle. It came with only one front sight insert with an aperture of 3.5mm diameter. I was having a dickens of a time getting a good sight picture, so I noodled around on the internet for information and found that most shooters recommend around a 4mm aperture for 10m target shooting. I could have bought either metal inserts or a set of plastic inserts, but I figured I’d save some money and have some fun making my own plastic inserts.
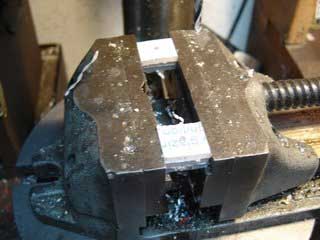
Some squares cut out of 1/8″ thick lexan. Acrylic might be slightly better optically, but Lexan is what I had. I used a drill press to drill a hole in the center of each blank with a #32 drill bit (.116″ – just under 3mm) for a #4-40 screw hole.
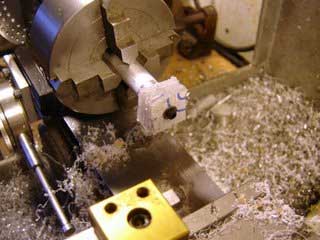
I mounted several on a mandrel held with a #4 screw, chucked in the lathe and running true.
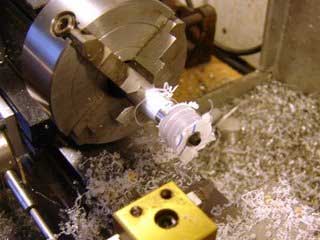
I turned them down to a few thousandths under 17.5mm (.689″) diameter, which is the size that fits the front sight mounted on the Diana. This gives a stack of round blanks.

While the blanks were on the mandrel, I chamfered the edges using a vee cutter, as seen above. This removes the sharp edge of the blank and makes it easier to insert in the front sight tube.
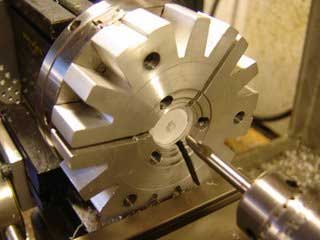
I removed the blanks from the mandrel and mounted one of the blank discs in the 3-jaw chuck, which was equipped with soft aluminum jaws bored out to hold the disc. I lightly chamfered one end of the hole to provide centering for the drilling operation and to deburr the edge of the hole.
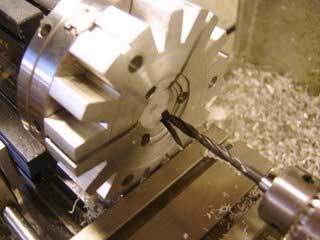
Then, I drilled with a 4mm bit at relatively high speed to get a round hole, which is hard sometimes with a drill bit, as they want to make a Reuleaux triangle. It’s better to use a reamer if you have one in the correct size. I’ve made them with different hole diameters for different lighting situations.
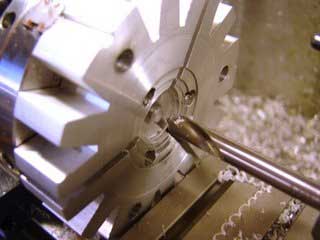
I flipped the disc in the chuck and put in a 90-degree countersink with a 90-degree center drill. This is what gives you the dark circle of the sight. The thickness of the ring, assuming that you use a 90-degree countersink/center drill for making the conical countersink, is equal to the depth that you drill with the countersink minus the diameter of the aperture hole.
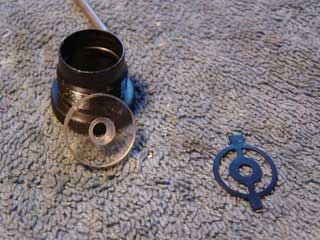
The finished insert with the old metal insert beside it.
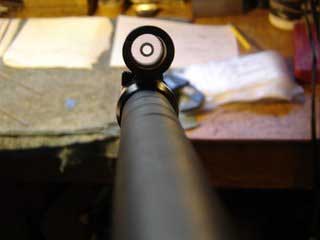
As you can see, I get a nice dark ring without the added distraction of the little arms on the metal insert sight. I snapped off a quick 5 shots to test and shot the smallest group thus far. It works! All told, it took about 20 minutes to make the one from start to finish, and I had several blanks left over.
Interesting…I always enjoy this post. I have 1 question off the subject. Is it unadvisable to shoot round balls fron a springer? It doesnt seem like they seat correctly. Thanks
VERY nice work BB!
OOPS, i was meaning to say Very nice work Nick Carter.
Round balls,
I shoot round balls from every springer I own – even the Webley Patriot. As long as they are full-sized, they seal properly and will work. And they are usually in the medium-weight range for a given caliber.
B.B.
BB,
Ammo question: do those round balls you shoot tend to group ok on average, at least on an average rifle? Also, remembering my different type ammo question a few days back, I’m thinking of looking around to see what I find (though most would probably be referenced from firearm and artillary pieces). JP
JP,
Yes, at close range round balls can be quite accurate. If you are seriously interested, read Sam Fadala’s works in the Black Powder Digest. Sam did the best round-ball work I have read.
B.B.
Hey B.B.
The Supreme Court is reviewing a major case this that will set a precedence on our Second Ammendment rights. I’m surprised that you haven’t brought this up as a blog topic. Even though your blog is about airguns instead of “real” fireams, the decisions made by the Supreme Court could eventually impact the rights of airgunners.
John,
Although I haven’t mentioned it, I am watching this case. It involves the right of states (or territories) to make laws that take precedence over federal law and even the constitution.
I hope the Supremes are not guided by politics, like the Mississippi Supremes in John Grisham’s The Appeal.
B.B.
B.B.
Thanks everyone on the Round ball tips. i use the gamo 177 and have only checked the accuracy at aprox 30ft but so far I am satistied. Also I will check out the Black powder digest on the subject. I saw that Crosman is coming out with 2 new CO2 bb repeaters;any dates known as to when they can be purchased? Love your reports. Thank you b.b.
Round ball,
Are you referring to the Crosman T4 Opts? If so, what is the other pistol?
I would guess in about 2 months or less for the T4 Opts.
B.B.
Nick,
Thanks for reminding me about aperture sights and globe inserts. Aperture sights are the one thing missing from my arsenal ever since the two I ordered didn’t fit my gun. There may be a future for a real target gun some day.
You technical folks impress me no end.
Matt61
henry
Thanks for the green compound link yesterday. I’m good to go.
B.B., now that you mention it, I didn’t even know that frogs have hair; this sounds like hen’s teeth. Anyway, I will settle for shaving any hair for the time being.
Matt61
Hey BB,
Glad to see the post here. I had read it on the origional website. I am intrigued with turning lexan on the lathe. One of my other hobbys is turning wood, however i have no experience with machine lathes.
Nate in Mass
Nate,
All my experience is with metal! Go figure.
Be sure to visit Nick’s website, as it has a good amount of machine talk.
B.B.
Though I’ll probably not blog here, it’s great to let some people show us things for a different perspective; the new tradition fits this blog’s quite liberal environment and tone.
14 in Fla
P.S
Those sights are REALLY good, and he goes into great detail about the making of the sights. Kudos, Nick.
Hello b.b., The 2 Crosman models (new) are a C21 and a C31. Both CO2 BB repeaters. I emailed Crosman about the date they would be for sale. I saw them on the Crosman Website in the top banner for new items.
Thank you and take care
Nick,
Thanks for the blog. It was enlightening and insightful. As is your personal blog site. Henry looks like a great helper.
If you every find you need to buff out minor scratches or machine marks on the lexan… try toothpaste. It is low cost, easy to find, and actually works very well.
For all you audio/airgun-video people – you can salvage scratched DVD & CD disks using toothpaste and a washcloth. Just keep it moistened with water while polishing then wash with water and pat it dry with a soft cloth. So far I’ve never had one that could not be recovered.
If you’re into power tools a new buffing pad in a variable speed drill makes the buffing job faster… and more dangerous to you and the disk.
DB
JP,
Just another opinion on using round balls. I shoot them a bit – they are very handy when letting the kids plink. The kids do not have to worry about which end goes in first.
They are light so like any light pellet they are best used at close range. Not a concern for the kiddies they are going to shoot at close range anyway.
The lead BB’s find their way into my Crosman 1377 and provide acceptable results when can popping. Also shoot them through my Crosman Auto Air AAII instead of steel BB’s. Again it is for the kiddies. Lead BB’s do not bounce back quite as bad as steel. The AAII is really a 15 to 20 foot shooter… rapid fire though so it is cool.
The only real drawback is the lead BB’s ($1.65/100) cost slightly more than a CP light pellets ($1.172/100) and a whole lot more than steel BB’s ($0.27/100).
DB
BB
i have a few small scratches on the butt of my rifle. The wood is a nice walnut and is otherwise perfect. How woould i go about fixing these? Im not at all ‘handy’ so any laymans tips would be appreciated.
Thanks
Paul
B.B. Not on subject. Can the Gamo Compact pellet velocity be adjusted up or down? I’m using Gamo Match pellets and the best I get is 350fps. The gun has less than 500 shots on it.
THANK YOU !!
This is the kind of “hand on” article I like to see.
This blog is a wonderful resource, keep up the good work!
BB,
Just read in prior entry where you mention that your not an employee of pyramid arms. Sure hope
P.A compensates you in some way.It’s because of your writing and the comments from your readers that I started ordering from P.A. It would be my guess that you make P.A. alot of money. As far as customer service goes I have not been to impressed with P.A.. I had a problem with a scope mount that know one seemed to want to resolve. My wife ordered a Tx200 for my birthday around Feb.1. The gun was suppose to be in 2/28 then told that it wouldn’t be in until 3/28. Around 3/10 P.A. calls saying gun is in ready to ship needs cc info. My wife asks if they will cover overnighting since being so late and that it was a gift. Never hurts to ask! Was told no and that was fine. Five days later my wife checks on order and see that it still hasn’t shipped. After contacting P.A. she gets so frustrated with thier service she just cancels the order. To make along story short I never got my new rifle. Looking for someone to buy it from, really don’t want to buy a gun made outside the US from someone that dosn’t want to go out of their way to please their customer. Maybe I just expect to much for my hard earned money. This whole situation puzzles me P.A. seemed to be such a stand up company from everything that I read in your blog. will definitely keep reading.
Nick,
Nice blog! I think using Lexan (also known as polycarbonate, or bullet proof glass) is an appropriate choice. It should resist scratching better than acrylic (Plexiglass). A guy can make an unlimited amount of different sizes if he wants for next to nothing this way. I have a lathe, but not everyone has one. I wonder if someone can come up with a way to make these with just a hand drill and a vise. Most everyone at least has access to one of these. Great Job!
/Shooter
Paul,
You can just leave the scratches and put some Old English walnut furniture polish on them to seal them up if they’re into the wood itself and the stock is oil finished (or even if it’s finished with polyurethane). The scratches are honest and give it some character. This would be my preference if it were my rifle.
If it’s just scratched into the polyurethane coating, this can be lightly sanded (inside of scratch only) and new urethane dabbed into the scratch with a toothpick. Then sand flush and polish to match the rest of the stock. You’ll still see the scratch, but it will be much less noticeable.
If you really want to refinish the whole stock back to perfect, that’s more involved. You’ll need to completely sand out the scratch, blending it with the level of the wood around it (don’t leave a dent), and remove the rest of the stock’s finish (I’m not much for trying to match new finishes to old, although there are some people who do a great job at it). Then you’ll pick the stain and finish combo that you like and reapply according to the directions for what you chose. Different stains and finishes require too many different techniques to go into here, but if you google wood stains and finishes, you’ll find out what’s compatible with what (again too much to list here).
Hope that helps.
/Shooter
I’m glad you guys enjoyed it!
Nick
Shooter
thanks, thats an excellent and detailed reply. Kinda scary for someone like me with 2 left hands so i think ill maybe polish it as you mention and leave the scratch looking honest 🙂
paul
Gamo Compact,
No, there is no easy way to adjust the velocity of a Gamo Compact. The most you can do is keep the mechanism properly lubricated to keep the power up to spec.
I used to own a Compact, and I’ll soon test one head-to-head against an IZH 46. When I do, I’ll discuss how to maintain the Compact and how to adjust the trigger.
B.B.
TX 200,
Here is the scoop on why the TX 200 is backordered. Air Arms cannot keep up with the demands of Pyramyd AIR.
Pyramyd AIR has out-sold the production capacity of Air Arms spring gun manufacturing capability, which is a good thing and a bad thing. It’s bad for customers who now have to wait for their guns, but it’s also good, because it means that Air Arms is not willing to speed up the production cycle of their TX 200.
Until a year ago, TX 200s were brought into the U.S. by smaller dealers who might order 10-20 rifles at one time. So when Pyramyd AIR hit them with much larger orders they were dancing in the streets – until they realized they couldn’t keep up.
You may be able to locate a TX at one of the smaller dealers, because they don’t move their guns as fast. If you do, buy it with confidence, because Air Arms never let their quality suffer for improved delivery.
I’m sorry this experience worked out this way, but it is not uncommon when the product you desire is in so much demand. A local Best Buy has a wait list for the Wii boxes, and people have to go to the store on the days when they arrive, if they want to get one.
I will end with this. Just because you’ve had a bad experience, don’t let that put you off the TX 200. It’s well worth the effort to get one.
B./B.
TX200
I had the same experience when I bought my TX200. I waited about as long as your wife and fianlly did like BB said and went to a smaller dealer. No more complaints. It is a great gun. As for PA, if you think about it, it is really BB’s fault for telling the whole world what a great gun it is :).
Thanks BB
MCA
TX 200 and everyone,
I just learned that Air Arms is trying to catch up with their shipments to PA. They have sent a large shipment of rifles that will hopefully wipe out the backorders.
B.B.
How do I find part 2 of “RWS Diana Schutze –
New youth breakbarrel rifle?” No link I can see here either???
Is it just my computer or does every one have the same problem?
Not familiar with your site and blogs in general so if this is posted in the wrong spot, forgive me. I have a PPK/S that leaks severely. I am looking for a complete seal kit and an exploded parts diagram. I have extensive experience in repairing/ modifying paintball guns and have my airsmith’s certificate from Airgun Designs (automag). Can you please, please help me. PPK/S works great when it works, but it doesn’t work anymore. Sorry if this is not the right way to do this, we visited umarex’s site but it is useless. Thank you.
Diana Schutze,
You asked about Part 2 of an article ON THE DAY PART 1 WAS PUBLISHED.
Unless you own a time machine, there is no way to see Part 2 before it has been written.
B.B.
As far as I know, there are no parts diagrams available for Umarex airguns. The design is straightforward, so with your experience it should not present a challenge.
I don’t think parts are generally available from anyone but Umarex USA.
B.B.