by B.B. Pelletier
When I was whining about how busy I am on Wednesday, a couple of you got the idea that Pyramyd AIR was somehow to blame. Please understand, my friends, that they have never been anything but kind and generous to me. I’m entirely responsible for creating the situation I find myself in, and they would be only too happy to bail me out if I would just tell them how.
And Wayne, on the S200 testing deal, again it was my decision not to get the same rifle in two different calibers. Pyramyd AIR bends over backwards to keep me in blogging guns, pellets and equipment. I’m just too much of a cheapskate to run a test like that, because of what it does to their inventory.
Well, today I want to pay them back just a little for all their support. As America’s largest airgun dealer, they also get their share of unfavorable customer comments, and perhaps pellet orders lead the list of topics. There are two big complaints that I will address:
Damaged pellet tins and customers who receive only three tins of pellets when they believe they deserve four.
Damaged pellet tins are the bane of all companies selling pellets in tins. Crosman was so wise to sell their Premier pellet line in cardboard boxes for many years. They’re still packed that way, but no others are. Whenever pellets are packed in metal tins, they’ll show the results of impact suffered during shipment.
And, though it may go without saying, I do want to say that the reason people don’t like dented tins is because it’s obvious the soft lead pellets inside will be damaged at the same time. The tins don’t have to be dented for the pellets to be damaged, but it’s pretty certain they will be damaged when the tins get dents.
Damaged pellet tins – part 1
There are two times when a pellet tin is in jeopardy. The first is when it’s shipped to Pyramyd AIR from the manufacturer. Tinned pellets come packed in cardboard sleeves that are usually packed inside cardboard boxes. These boxes are then secured to pallets by shrink wrap and sometimes by banding. If a pallet of pellets falls off the forks of a forklift during handling, or if the forks hit the pallet too high, or if the pallet catches on something in the warehouse as it passes by, there can be impacts that dent tins. The pallets arrive at Pyramyd AIR and are inspected. They contain perfect tins, slightly dented tins and heavily dented tins. There are also tins that have been destroyed, with loose pellets scattered everywhere.
One thing about pellets is that they’re generally made of lead. Being heavy, you only want to send them one time. That’s anywhere! So you can forget returning a bad shipment of pellets; it doesn’t happen! Pictures are taken and sent to the manufacturer and invoices are reworked when something bad happens–all of which takes time. Then, there’s the time taken by management and the warehouse staff to sort pellet tins and segregate them in inventory. Next, there’s more time to conduct special sales of dented tins. When all is said and done, nobody makes anything on a dented tin.
Damaged pellet tins – part 2
The other times pellet tins can get damaged is when they’re shipped to the customer. Here, Pyramyd AIR has more control. They can pack those pellets better and get more of them to the customer in perfect shape. The question is: Better than what? There are not a lot of solutions to shipping low numbers of pellet tins.
Over the years, Pyramyd AIR has simply put the tins in small boxes stuffed with peanuts. That turned out to not to work very well. Then, they tried wrapping them in bubble wrap. That worked better, but was more time-consuming to pack. When you’re trying to package an order as fast as possible, anything that takes extra time stands out like a sore thumb. Cling wrap works even better to keep the tins closed during shipment, but does little about crush and dent protection.
So, they’ve very recently come up with a new way to pack pellets for shipment. That’s what I’d like to show you now.
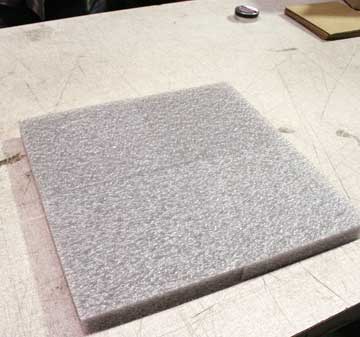
It begins with a sheet of high-density foam.
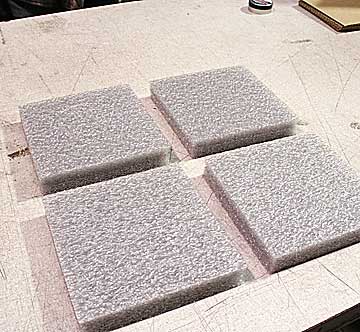
The sheet is cut into quarters.
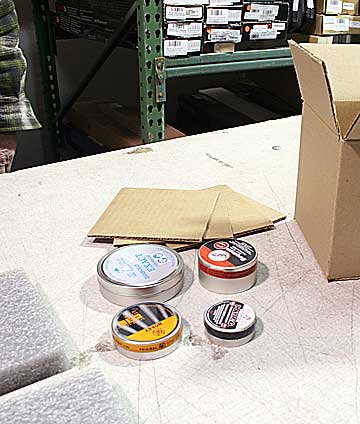
Here is a typical order. Note that the tins are different sizes and heights. They are also different calibers. This is a common order, with the “Get the 4th tin free” promotion.
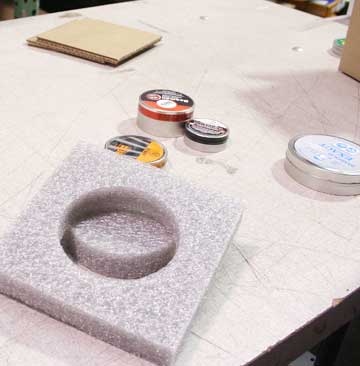
The first foam square is cut to fit the largest-diameter tin.
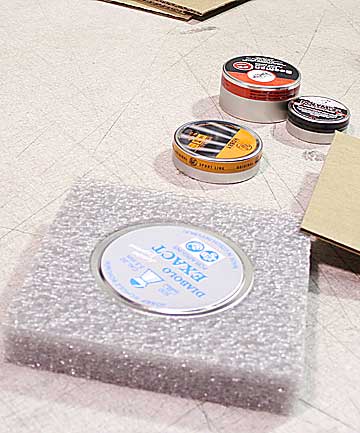
The first tin is placed in the foam square.
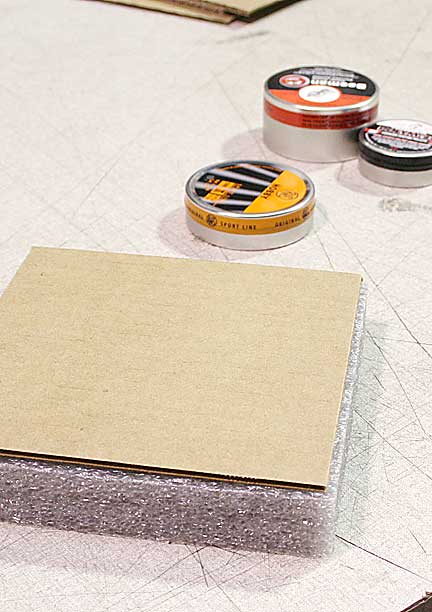
And covered by a cardboard square. These squares have to be cut and warehoused, too.
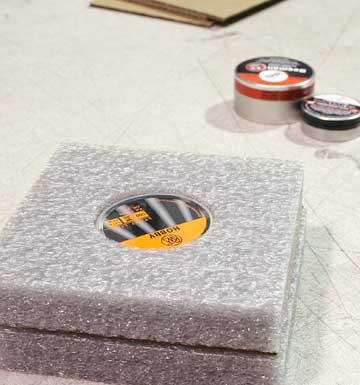
Then the next tin is packed on top and so on.
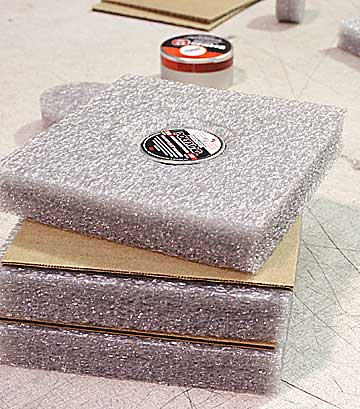
Foam with tin, cardboard square, foam with tin, cardboard square until the entire order is packed.
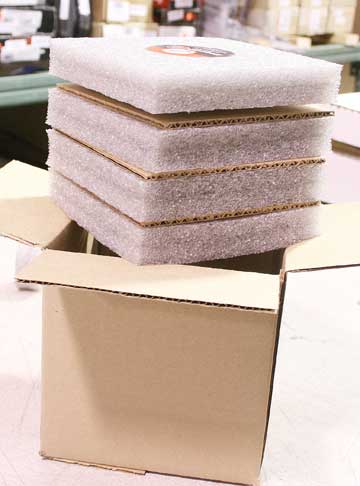
The stack goes into a box.

The cutouts go in the box to pad the stack. Nothing is wasted.
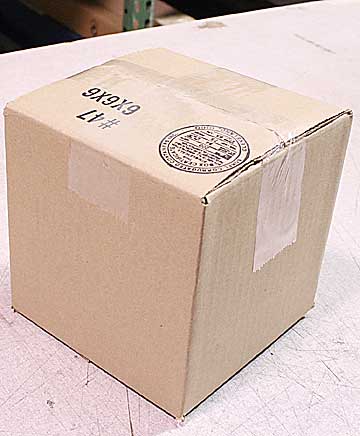
The box is sealed.
Kudos to Pyramyd Air
The forums are buzzing about this new pellet-packing method. Long-time customers are saying this is the way they want their pellets packed from now on. But there’s more.
Get the 4th tin free!
Some customers are grumbling about not getting the 4th tin of pellets for free, the way the promotion states.
Well, actually this used to be a bigger problem than it is now. In the past, if the 4th tin wasn’t picked by the customer, it wasn’t shipped. Some customers didn’t understand how the software worked and assumed it was going to select the 4th tin for them, so they didn’t pick a 4th tin.
That was in the past
Pyramyd AIR now has a prompt in the ordering program that reminds the customer to select the 4th tin. That has fixed the problem.
However, there will always be a few scattered cases where the customer really does order 4 tins and gets only 3. That is a packing mistake, and has to be corrected by calling Pyramyd AIR when the shipment arrives.
I tell you this because of the old software problem and some people who haven’t ordered pellets from Pyramyd AIR in several months are not aware that it’s been fixed.
The 4th (free) tin cannot cost more than the lowest-priced tin of the other three tins.
Wow, a long one today, and I’m sorry that I didn’t give you grist for the weekend gabfest. Well, you guys will just have to get that one going yourselves. See you Monday!
BB,
I’ve found a glitch (sort of) in the shopping cart software when ordering pellets from Pyramyd AIR. If I place expensive tins of pellets in my shopping cart first, followed by less expensive tins, sooner or later, one of the less expensive tins shows the price at $0.00. That’s as it should be when you reach multiples of four tins. However, if I want to update to more than one tin of that less expensive pellet, or if I place multiple tins of the less expensive pellets in the cart after the expensive ones, the shopping cart will not update. It will only place one tin in the cart at the price of $0.00. I understand the glitch. You can only get one free tin per four purchased. I’ve figured a way around the glitch by deciding beforehand which pellets, and how many of each I’ll be ordering, and then placing the least expensive pellets in the shopping cart first, and progressively adding the more expensive tins afterwards. As I reach multiples of four tins, the cart updates the least expensive prices to $0.00 accordingly. When I buy pellets from Pyramyd, I like to take advantage of the free shipping offer for orders over $150.00. Even though this is not a true glitch, I hope this makes sense to your readers who place large orders for pellets online.
Kind regards,
Michael in Florida
Success is not an entitlement.
Of course I’m all for improvement and the new packing process for pellets. Just can’t see how the new process is “less time-consuming to pack” than “wrapping them in bubble wrap”.
Looking forward to receiving my next batch of pellets. Nothing worse than opening your order to find 500 “soft lead” JSB exacts scattered in the packing box.
I wish that Pyramyd carried the Pellet Tin Safety Boxes like these. They're very handy. I do nearly all of my business with Pyramyd. They've never let me down.
http://ahg.anschuetz-sport.com/index.php5?menu=88&sprache=1&seite=83&produktID=447
Champions and a few other stores carry these in one form or another.
B.B. Tell P.A. to look at the possibility of offering a small monetary incentive to select Beeman “5 packs” (or other bulk packed brands) So that the packer has a box to deal with instead of tins. Also I would like to see a special called the $150.00 special where if you order $150.00 dollars worth of pellets you get a special deal. This would have to be a very specific deal, such as, “ALL pellets must be of the same brand, type and caliber” in order to save on pulling and shipping times. Prime example…. Order 19 tins of Beeman Kodiaks in .22 and you get 6 tins free, which equals 25 tins which equals five “five packs” Which equals $151.81. NOW, on top of the 6 free tins AND the free shipping and handling P.A. knocks off another $1.81 makeing it the $150.00 deal!! My buddy and I will be ordering $150.00 worth of .22 cal. Beeman Kodiaks some time this year. If P.A. had a couple of their most popular pellets already boxed and ready, all they would need to do is slap a label on it and BLAM. What do you readers of this blog think? From SavageSam
Kudos to them for making such an effort. This blog post makes me more likely to order pellets from them.
Yep, I’m on the defense bandwagon too. I have purchased guns and supplies almost exclusively from PA since I jumped back into airguning about 2 years ago. Whats the problem? None for me so far. Any issues that I had were resolved to my satisfaction. The worst was a Super Streak that would not shoot after 3 shots. A stuck sear, I guess, kept this bad boy cocked. A simple exchange of guns by mail fixed the problem. I also stay loyal to PA for providing a forum for this blog which, fortunately, I am hopelessly addicted to. I mean where else can you learn as much about airguns as you do here. And if loyalty does not count,then the $150 free shipping and 4th tin free can’t be beat. Who else offers it?? Anyway, I’m off to host a meeting on a beautiful morning in NC, a meeting, that is, of sqirrels and high speed lead. Happy airguning everyone!
Rich
Michael,
Yes, PA is aware of that glitch and is working on it.
B.B.
Fantastic. Continuous improvement is what defines good customer support.
Herb
Love the packing idea. Should help. Have received damaged tins. One time had the pellets crushed a plastic bottle of oil… what a mess in the box.
Do not like the lowest price pellets being picked. I’d like to order (4) $15 tins and (4) $4 tins and get one of each price free. Would allow me to order all my pellets on one order instead of breaking them up into many orders to save money.
DB
SavageSam,
Great idea. I like it.
DB
Excellent point DB. I have often put off pellet orders for that same reason. Don’t know if PA can do anything about it though.
I always buy sets of (4, or multiples of 4) at/around the same price. Doesn’t make much sense to order (3) tins at $15 each, and (1) at $4.
I’ve been sure I wasn’t the only one.
. . . Airsoft Adventures. . …(Part I)
. . .To better understand this review it is helpful for the reader to be aware of my gun background. I agree with other contributors that personal information is generally not eagerly embraced here, especially since many of us are in witness protection. However, since my opinions/judgments are colored by my experiences, it is necessary for you to know that…
I clearly remember shooting toy guns of all manner from ages 5 through about 12. In the 1960s, these guns used brass colored cases with spring inside the case, into which a gray plastic bullet was snapped via two small prongs at the bullet’s rear. A single cap could be stuck onto the back of the case, and then loaded into a single shot rifle or even into a revolver. As I recall, they were strong and accurate enough to hit a person at 30 ft., yet the bullet at that point was falling fast. These bullets also never hurt, and they never left marks, let alone dents, on the furniture.
As I recall, toy machine guns for children in the 1960s could employ a roll of caps, yet I also recall how often the paper roll tore apart and had to be reset.
There were “realistic sounding” battery operated machine guns and repeaters, but I never encountered one that shot anything other than sound.
I shot light-powered Sears (?) rifle and remember that through the years I owned several types of targets. Some were even moving targets, using a bicycle type chain drive and housed in real metal.
At the age of 12 I left ” children’s toys” (which are defined here as having little inherint hazard, such as small choking parts, hot spots, sharp edges, or high speeds) and began playing with what I was told by my Dad was “grown up” toys, viz. those that had to be treated with safety/respect (e.g., air guns, power tools, internal combustion driven toys).
From childhood I played with several $30 – $ 60 CO2 rifles and pistols, later followed by .22 and .357 firearms.
The Airsoft Guns and targets that I experienced a few weeks ago with the children over different times and conditions are clearly closer to Adult Toys then they are to Children’s Toys. They do pose an Inherint Hazard.
Note though that I wrote “…are closer to adult toys.” I cannot put them in the same hazardous class as bb or pellet guns (which I put in the same class as firearms, when using the dichotomous classes of either adult or children’s toys), and yet they are clearly more hazardous than any toy that I ever played with in childhood.
So, Airsoft Guns are a sort of “Adolescent Toy,” although I am hard pressed to find any other toys to fit this category.
The Good adult airguns experience that I have undergone that are closest to the Good Airsoft gun experience are the Drozd bb machine guns. I have owned about 5, since they sometimes break and since I have modded most of them.
The Bad adult airguns experience that I have had that is similar to the Bad Airsoft experiences that I encountered would include the lousy Chinese Tech Force spring rifle. I will explain later. Suffice to say that I have shot lots of $30 – $ 130 gun toys, and understand that there are limitations having to do with accuracy, reliablity, and ease of shooting. Part II later today…
– Dr G.
Michael,
Like you I work out my pelet order in advance. Put together an Excel worksheet with all my favorites.
Just make my selections and it calculates the total price and just for fun the price per pellet. When tins ship in various quantities it is difficult to measure which it the better value without crunching the per each shot price. My pellet orders generally include several free tins.
It helps me.
DB
B.B.
A suggestion for future blog.
Consider pellet lead recycling. My thought is using it to cast large bore slugs for big bore air guns or black powder guns. Would need to include an overview about how easy it is to cast your own slugs.
Then also include a green approved method of disposal. Do not like the idea of tons of lead being dumped in the trash. We as responsible shooters are better than that.
DB
Solution to the problem of being able to order (4) $15 tins and (4) $4 tins on the same order and getting one of each free…
Create part numbers for a sleeve of four that is priced like three tins. Then PA could pre-pack them and then just pick and ship. And more important to use customers we could blend our pellet orders.
Maybe even sleeves of five or eight or ten; whatever works to save packing costs. The big spenders will buy the bulk part numbers.
DB
You can use a coupon code with the 4th tin free feature. You cannot combine a coupon and free shipping. This is nice if you don’t want to invest $150 in pellets all at once. The coupons codes are normally for 10% off. The new packing may explain why my pellets have not shipped yet. I ordered some just to see the pretty packing, like many others are probably doing.
Volvo
Dr G,
Could you please reveal a favorite full auto airsoft rifle? I would like to pick one up and have no idea on the differences in quality, etc.
Thanks,
Volvo
B.B. & All,
Good Morning! & Gi'Day, down under,
The solid foam is great for another reason. It's much more re-usable by the consumer.. The loose bubbles are a nightmare… the bubble wrap is ok to reuse if you ship stuff.. but I find uses for the solid stuff all the time..
Tom,
Let me help you feel better about taking TWO new rifles from the PA inventory and testing them, and returning them as used..
1.) Google.. Our raised garden bed website is our only source of sales.. and we have grown our business using paid adds with Google. Those results on the top and down the sidebar are paid for..
When you click on ours, it costs us $.75 and takes you to our site.. If you scroll down you'll find us also, and if you click on the unpaid results. it cost us nothing..
Google wants to list the best sites first.. whether they are paid or not.. The way they measure who is best, is by how long people stay on a site when they arrive.. and how often they come back..
For the advertisers, they provide an analyst site, where they show you all this.. and much, much more.. (you think the government knows about you, they probably get their info from google)..
So, a blog brings people to the site, keeps them there, brings them back many times per day to read, make, or check on comments..
For a retailer dependent on their website for sales.. there is NO amount of money that can replace the traffic generated and the benefits to your google page rank.
I say NO amount, because if I bid $.75 per hit for top billing and someone else bids $1.50 and they have a "click through rate" of say 4% and I have a click through rate of 10%.. google will give me top billing.. They are good at math.. they can figure the odds of making a sale..
So, one can buy top billing, but if you don't quickly make a high click through rate, keeping that spot will cost you a lot more than your competitors..
And all the paid for traffic also raises your unpaid result ranking..so eventually you don't have to buy the add, except to keep others from being there..
The bottom line is Tom, this blog saves PA 3/4 of there add budget.. not to mention the increased sales.
So, I would think, they can take a 25% loss on two guns, instead of one.. and who is to say they have to do that.. I would pay full retail for a gun that's been through your hands… or better still I bet they could be auctioned off for more than retail..
Wacky Wayne
Ashland Air Rifle Range
supported by naturalyards.com
Is this the new secret to accurate long rage shooting? Quite a few guys on the forums are using it.
http://today.msnbc.msn.com/id/28527841?gt1=43001
Good afternoon B.B.. Open blog Weekends. Yes!
Kevin, I’m going to have to hunt for your required reading material, ie, Gaylord and Cardew. Thanks for reminding me.
A question please: what is the rule of thumb for how thick a layer of plumbers putty is needed to stop say a Beeman Kodiack at say 900fps? Thanks
When it comes to pellets, I would like to see PA put a description of lead consistency on each pellet tin web page.
The gimmicky “hyper-velocity” pellets overtly mention being lead free. It would be nice to know the ones that are of a hard (higher level of antimony; Crosman Premiers) consistency, soft (like JSB’s), and moderate/medium.
I wouldn’t be expecting a compound breakdown. Just a designation that lets me know I’m buying something closer to “pure” lead (knowing that no pellet is truely “pure” lead).
Volvo,
Patience is a virtue. Seeing as how you are Volvo, and not BMW, you obviously already know this at some level.
I will write as soon as I cure a few more patients. Yes, I am a real doctor.
– Dr. G.
Mr B.
Among others, I use a Gamo trap that I simply fill to the brim with the Duct Seal that PA sells. It is not nearly as stiff as the ballistic putty I received from Beemans years ago.
A couple inches of that stuff will stop any normal pellet. The nice part about the duct seal is it is easier to work with, but you’ll need at least twice as much.
Volvo
I have never had a problem with PA, and the 4th tin free is why I buy all of my pellets there. I have received a few dented tins but the pellets inside are usually fine, and for the ones with a damaged skirt, the cap off a tube of Pellgun oil makes a good pellmil.
Dr G,
No rush, I just wanted to make sure a clear winner was chosen. I always thought you were an actual Dr. even though your writing is fairly easy to understand. On the other side of the coin, I look like the RCA dog when I read Jane’s stuff. Jane,no offense intended, and please don’t dumb it down for me. I smile when I see you and Herb conversing even if I have no idea of what is being said.
Volvo
BB’s Big Announcement:
5 Days
19 Hours
30 Minutes
J. Hansen,
Did you get the Kel oil info posted a few days ago? Probably last Fri or Sat night.
I wish only the manufacturer can pack their tins like that. I really enjoy the cardboard box that premiers come in.
B.B.
Excellent post B.B.!! Two Thumbs up for PA’s service…
Cheers,
Jony
Wayne,
I agree – I would pay more for a gun that B.B. has tested. If we are willing to pay $10 for 10 shots how much for a gun massaged by Tom himself?
Al Pellet
Mr. B,
What you want is duct seal, not plumber’s putty. Pyramyd carries it, but so do some Home Depots. It is in the electrical section of Home Depot, “Gardner Bender 1 Pound, 10Pack Plugs Duct Seal Compound,” Model DS-110.
.22 multi-shot
DB,
In just over a week I can show you what I do with recycled pellets.
Ask again next Friday.
B.B.
I’ve ordered pellets several times from PA at this point, and every order came in perfect — no spilled pellets or dented tins. Had this been different I’m not sure my first recourse would have been to rush to the blog or the Yellow Forum to whine about how PA is going down in flames. My quality of life does not depend that heavily on a pellet shipment. Nevertheless, it seems like they take criticism constructively.
I do resent the expedited order option, but that’s just my Jacksonian bent. The 10 shots for $10, I’m neutral on, since a lot can happen in shipping. I wish they would carry the Industry guns (esp. the ’78 variants), FX, and continue the directly-imported HW line, but they have to make decisions that make sense for the business.
All in all, its hard to find a vendor that takes a hobby as seriously and conducts itself as professionally as PA. In addition to supporting BB’s blog and other articles and BB’s and Paul’s videos, there are some other very helpful people there, particularly Sharon.
awwww…BG_Farmer and Sharon sittin’ in a tree…
B.B.
I can’t recall any systematic problems with pellets other than the odd deformed one. RWS Hobbys in the the tins have all worked great for me. I actually dislike the cardboard boxes for the Crosman Premiers because pellets would inevitably get wedged into the cracks and under tape.
I’m not sure if you got my email a couple of weeks ago explaining that I had some trouble loading pictures for my guest blog. I will resend to the same address.
Hello all and Happy New Year. I have been on long range reconnaissance of shooting ranges in Hawaii. As I’m sure Joe B. will agree, the weather was fabulous as usual. But would you believe that the only public shooting range on the island of Oahu requires you to build your own target frame? I’ve never heard of such a thing. The carpentry and tools were all new to me, but thanks to my experience working with airguns, there was no problem. Now, I am the proud owner of a new drill, and I will be looking for things to drill holes in. I’m also starting to think that any range with a distance over 100 yards is a rare thing. That was the farthest distance like my range back home, but they also had gongs set up at 230 and 300 yards. Anyone know of an online ballistic table or calculator? I only hit one of the gongs at 230 yards with my police rifle while estimating holdover and would like to be more systematic next time.
And I have another chronicle for the annals of shooting conversions. I took my Dad out to shoot my 1911, and it was mayhem. He forgot everything I told him and was trying to put both right and left index fingers through the triggerguard before shooting. With his thumbs waving around and looking generally shaky, he had the range master crouched over one shoulder looking ready to spring in an instant if there was trouble. However, all went well, and in the process of spraying the target at 25 yards (the minimum distance at the range) he landed two right on the bullseye. One was almost certainly luck. Two probably was as well although I’m at a loss to explain it. Anyway, it all made him fairly insufferable and he went up to the range master with his target and told him about getting a bullseye on his first time out with a .45. The range master smiled and patted his shoulder.
Off to the rifle range and what a circus that was. He couldn’t get himself adjusted to the scoped police rifle and for the M1 he forgot to look through the rear sight and missed everything. The tour through memory lane didn’t work out at all, and he says he can’t believe that he ever fired the Garand as a young man with all of its weight and recoil. Finally, he quit because he said that the muffs were hurting his ears. The rifles didn’t work too well, but he is definitely a convert to the pistol. I’m mostly glad that my target frames fit in the mounts.
Matt61
I recycle or reuse everything I can from lead pellets, paper/cardboard, CO2 cartridges, plastics, tin ,aluminum, glass and firearm brass etc….
I’ve worked in a lot of factories when I was younger. Now I work in the transportation industry. One of our competitors had a return on 3 truck loads of parts worth about $200,000. The parts were rejected because they were damaged and were not transported properly.
So you never know how things are going to be handled, so every little extra bit of protection helps.
I have had no problems from PA, but I’ve seen some big box stores mangle some of their tins of pellets and had to significantly reduce the price on them or toss them out.
BB’s Lead Recycling Countdown:
6 Days
16 hours
15 Minutes
DoWayne,
Here is a term for you to google. SEO (Search Engine Optimization). There are firms you can pay to keep your company at the top of the free google list.
People often trust the free search more than the paid results. You might even get to stop paying Google.
I’m not one of those contractors but I know several and can recommend some names.
DB
BB
I read your article “Scuba tank testing – hydrostatic and visual inspection (Feb 15, 2006)” and found it very informative. Did you ever do one on co2 tanks? Because some of us airgunners have bulk filled co2 tanks for our airguns. What are the regulations governing them? Also if they are below a certain size, are they exempt from rules and regulations?
Thanks,
Joe
ajvenom,
You are the official event tracker. Congrats.
DB
Matt61,
Never heard of a gun called the scoped police rifle. But anyhow, since you mentioned police, I was considering buying a Ruger PCF police carbine in .40S&W for 447$. Have you any experience with these? I would never have heard of them if not for an add in shotgun news (the edition with the GSG mp5 on the cover).
Shadow express dude
DB’s Next Post Countdown:
5 Seconds
LOL!!!!
Just kiddding around.
For those of you who want to buy the Cardew’s book, from Trigger to Target, here’s the UK website:
http://www.cardew-watches.co.uk/Airgun-Book.htm
I don’t think you’ll find this in the USA yet. You might be able to get a hard cover copy and even have the son sign the book – extra collector’s value!
Yesterday, someone gave the wrong definition of flash point as the ignition point. Flash point is when a flammable liquid changes it’s state from liquid to vapor or “flashes” to vapor. Ignition point is the temperature it ignites. So speaketh the one time electrical engineer who became a fire protection engineer.
As for buy three tins and get the 4th free, I’m still waiting for JSB to ship those 22 cal pellets to PA so they can complete my order!!!!!!!!!!!!!!
Anyone read the news about the moron who shot his wife in the back with a pellet pistol here in NJ and she died?!! On top of that, the leading NJ paper had an editorial about how dangerous pellet guns are and to keep the law the way it is – a pellet gun is considered a firearm. What a state I live in. Every time I think I’ve come across a candidate for the Darwin award, someone else tops it.
Fred from NJ
Wait a minute…B.B.’s big announcement in in Approx 6 days and his recycled lead announcement is in approx 6 days…I think he’s found a way to make super accurate airguns out of recycled lead!
-C
Dr. G.- My 13 year old nephew wants me to get an Airsoft pistol. I think that it is because he wants to be able to shoot me. He has a replica of the shortened AR-15 (can’t remember the exact nomenclature) that REALLY looks like the real thing, and I saw plenty of them in the Army.
BB – One good thing about dented tins from PA – I picked up eight of them at Roanoke for $5 each. Haven’t noticed any dented pellets yet. Eun Jins, Cro-Mags, and a few that I can’t figure out.
I too do most of my on-line shopping at PA. I’ve only bought elsewhere when PA didn’t have what I was looking for. Never had any problems with them.
Lastly, I have an off-the-wall question for the group at large – Is it insane to want to put a GRT-III trigger into a Crosman G1 Xtreme? It’s only $32. I want to….because I can. I’m thinking of getting a gun that’s a little higher end in the future and I could always transfer it.
Joe,
All pressure vessels over 2″ diameter are required to be hydrostatically tested. That means CO2 tanks do get tested.
B.B.
Do any of you know if PA would ever consider adding .25 caliber Beeman FTS to their inventory. My medium powered .25’s love them but PA doesn’t sell em.
I’m glad that PA chose to change their shipping methods for pellets. It should cut costs in many different areas, all of which affects “the bottom line” in a positive way. Somebody actually listened at PA, and now you see the positive outcome.
I was not so lucky where I used to work. There was a lot of shipping damage because the proper materials/methods were not used, resulting in thousands of dollars in lost inventory and downhill customer satisfaction.
No one would listen to the guy that wanted to spend a little more money in the shipping process. For a few dollars more, they would have still been in business today…but oh well.
I did recieve some dented tins from PA when they were using the other methods, but none of the pellets were damaged to the point where I couldn’t use them.
Such was not the case from other companies. I can remember calling them, complaining, getting more dented tins as replacements…
I have always felt that PA has a great way of doing business.
Randy in VA
My first high powered springer was a Crosman G1 Extreme (an early production model with the higher end scope), I have to ask what kind of pellets you have put through it? Mine lasted well over 4000shots, I actually sold it for a new Storm XT. I traded it for the Storm because of the wood stock (I’ve worked with wood all my life and wanted to make something special, the Quest variant design was very smooth, and with a little tweaking, accurate). As you may know, the power plants are the same. Using nothing under 8.2gr, my current storm Xt has lasted 1400-1600 shots. The decision is up to you, is it worth the extra $$ for a rifle that will last 4000+ rounds?
Shadow express dude
Hello ajvenom,
You said in your post that you reuse/recycle CO2 cartridges. Is there a way to refill them? or do you just recycle them in your recycling bin? I’ve been keeping my used CO2 cartridges, and wonder if there was a way to recycle them. I’ve been collecting all the lead used pellets that I shot and plan to get into casting bullets sometime in the future so I can shoot lead bullets in my firearm. I’m trying to recycle and reuse as much of the stuff as I can. Also wondering.. do you know what material is Co2 cartridges made of? Aluminum? Steel?
Thanks for your tips.
Walther P99 fan
ajvenom, CJr. and anybody else to whom this pertains,
Regarding the lead recycling blog, I was just planning on showing you something I do with used pellets, and I’ll still do that, but after giving the subject some more thought, I have decided to expand it and go for the whole enchilada. I will show you how to reduce a pile of lead waste collected from the bullet trap to lead ingots that can be used any way you want.
Whoever I asked to keep the clock on this, please treat this seriously. I will be showing you all how to handle your used pellets.
Please remind me after next week, because next week is the SHOT Show and I will not be able to think about this.
B.B.
DB.,
We can talk about that, email me. We are on page one now for all the important search terms, without a blog mind you. Like I said, we pay for the top or second spot just so we keep others out, and insure we get a chance at the sale.. but let’s talk, we are bringing out another product that needs your service.
wayne.burns@naturalyards.com
Wayne
Ashland Air Rifle Range
Fabulous!
I’ll be ordering my pellets from PA again!
BTW, is PA going to offer the new JSB 18 gr. heavies anytime soon?
Duncan Idaho
Kudos to PA. I don’t know how many orders they normally get, but they just shipped one out for me while dealing with 1100 orders. It stayed in “Ready for shipping” a little later than normal so I asked.
We’ll see if this one comes with the new packaging. I got my previous pellet order with the saran wrap type packaging and that was padded within the bigger box of the shipment. I wonder if the new approach is only for separate pellet orders or we’ll start seeing multiple boxes.
JC
PS – That 4 tin pricing approach gets my vote also, I too don’t order different price pellets in the same order due to the PA pricing algorithm that assigns the free tin (s)based on the lowest priced tin (s)
BB,
Alright then, I’ll start saving bullets. Will lead alloys, like premiers, be able to be recycled? How about mixing soft cast with hard cast lead?
Shadow express dude
To Anonymous:
Yes, I did get the info on Kel spray, I found some locally, and have been using it. Many thanks.
To all airgunners:
Two things you might wish to try. A) Kel Spray – this is great stuff for cleaning and lubing pellets, barrels, bluing, etc. It CLEANS, the solvent evaporates FAST, and the residual is PURE silicone lubricant. It can replace virtually all that “other stuff” you keep for your guns. (O-ring lubricant excepted). And its cheap.
B) LE Targets rubber panels. Forget the messy pellet traps, forget the noise, the lead dust, the duct-seal goo….
These 2-inch thick rubber panels stop any pellet I throw at them – silently, cleanly. You can set in in your China cabinet if you like.
Nice weekend all..
Jane Hansen
Fred from NJ-
“Yesterday, someone gave the wrong definition of flash point as the ignition point. Flash point is when a flammable liquid changes it’s state from liquid to vapor or “flashes” to vapor. Ignition point is the temperature it ignites. So speaketh the one time electrical engineer who became a fire protection engineer.”
That was me. And I’m afraid I have to take issue with you on this one.
I’ll refine my definitions:
Flash point: the temperature at which a flammable liquid’s vapor pressure is high enough that its vapors are of flammable concentration immediately above the liquid’s surface. The vapor will not spontaneously combust at the flash point, but when an external source of ignition is present the vapor will burn, but the burning will deplete that vapor concentration rapidly enough that the flame dies out.
Fire point: the same as the flash point, except the higher temperature of the liquid in addition to the heat of the vapor combustion will continually produce enough vapor to sustain the flame.
Autoignition temperature: the temperature at which the the vapors above the liquid will ignite spontaneously in the absence of an external ignition source.
The temperature at which a liquid will spontaneously “flash” into vapor at atmospheric pressure is the temperature at which its vapor pressure exceeds atmospheric pressure- it’s standard (or sometimes “normal”) boiling point.
example: ethanol
flash point: 14° C (57.2° F)
fire point: ~15.5 °C (~60° F)
autoignition temperature: 363° C (658.4° F)
another example: gasoline (@ roughly 90 octane rating)
flash point: -43° C (-45.4° F)
fire point: ~-42° C (-43.6° F)
autoignition temperature: 210° C (410° F)
I suspect your usage of the term ‘ignition point’ is an industrial jargon term that is a conflation of the flash point and fire points. Note the explicit presence of an external ignition source is the above definitions.
As for the temperature at which a liquid will “flash” into a vapor under atmospheric pressure, that is any temperature above its standard (sometimes called “normal”) boiling point.
So as I said previously, whether you’re referring to a true flash point, fire point, or using the term “ignition point” for either or both of the former terms, you’re still not talking about something relevant to combustion of lubricating oils unless it has a spark plug in there to light the vapors.
It’s the autoignition temperature- the temperature at which the vapor will spontaneously ignite- that is relevant here.
Oh, I almost forgot: I didn’t get around to any further indexing yesterday; a minor emergency came up. Nor have I done it today, as I’ve been dragged around by my family for some reason apparently having to do with it being my 21st birthday.
My apologies for the tardiness of the indexing work; I should have plenty of time over the weekend barring freak happenstance of some other incident.
. . . Airsoft Adventures (part II)
The airsoft guns that I selected as gifts for my boy were a result of reading this blog (and asking BB questions) and about 3-4 hours of additional internet reading (reviews, including those on Pyramyd Airs site, and whatever else Google kicked up relevant about airsoft).
I wanted to keep the cost of each gun under $50, and while quality (reliability and ease of use, along with accuracy) was important, I always went for a $20 or $30 gun rather than $40 when possible. There are many hundreds of guns from which to choose, and so even with keeping costs down I had over a hundred guns to look at.
I also wished to get representative guns from each power source…1.)spring 2.) CO2 3.) electric motor as I was curious about these guns myself. My kid didn’t know nothin’ from nothin’ about this stuff…his friends have some spring airsoft pistols (about $5 from Ebay) and rifles (about $20 and $100), and that was what they knew.
Now to the part that you’ve been waiting for…the guns themselves….
The first one I gave to him was a $40 (reduced from $60) TSD M14 Airsoft Sniper spring rifle. Visually to a kid it looked wonderful, very real, very cool, heavy.
To me, I was thinking, “If the company spent this much money on the outside, then how much could they possibly have left for the all-important inside of the gun?”
The gun was cocked by pulling a lever (actually a small paddle) straight back, so there was actually no “leverage” in the full sense of the word. This was Bad. It was hard for the children to cock in the beginning, and sometime during the week I tore a peice of skin off my hand from the darn thing when my hand slipped off the small peice of metallic real estate. This gun started making me think of the Horrible Tech Force pellet gun that I once owned.
This gun was fun and used in the beginning of the Hollidays. It was accurate enough (note that I use the past tense…you know what is coming up as sure as you knew what was coming up for Tony Soprano) and strong enough to knock over empty plastic vitamin bottles at 15 -20 feet, and sometimes even beyond. It was strong enough to leave a red welt on my back when shot at 20 feet while wearing one layer of shirt (it hurt like a bad bee sting for 5 seconds, and then after a minute was fine re. pain).
This rifle had a “speed loader,” which is a plastic cigarrette sized box with a spring and plunger, into which the plastic bbs are poured and then from which the bbs are loaded into the gun. My kid thought it was really cool.
I thought, “this speed loader appartatus, which seems needlesly complicated, must cost $10…that leaves even less money to make the gun work…and what happens if this fragile speed loader breaks…no, what happens WHEN it breaks?)… (Part 3 later)
– Dr. G.
Randy – how well does your G1 Extreme shoot? If it’s accurate for you, there’s no reason not to do it.
The Quest guns can last for quite a long time, especially since Crosman sells very reasonably priced replacement parts for it. New springs are about $6, and seals about $4. A new trigger group is only $13.
They’re not made as well as Gamo’s, but they are still very serviceable guns.
Shadow express dude – I’ve put maybe 1500 pellets through my G1. A lot of Premiers – HPs and Ultra Mags. It likes heavier pellets, but it’s hard to tell what flies best without a chrony (next on my PA wish list).
Vince – I actually got some 3/8″ groups (10 pellets @5 meters, elbows on table)with it today. I’m thinking that this will be a good first step into serious tinkering. Heck, I only paid $80 for it in the first place. If I turn it into a box of parts, I’ll just have to buy something better to put the trigger in.
BB, as you know I’m working on an old Markham Model D (all steel, 1890-1900, I believe) for Wayne. He wants it functioning, and I want to get it working well with minimal impact as a collector’s gun.
The leather piston seal started disintegrating, so I had to tear the powerplant down. I found that the ‘piston’ (a piece of square tubing about 4 inches long) has an ear busted off. The ear is supposed to hold the piston head on to the piston.
If I braze (not weld) the piston head to the piston, it will be usable again – but from a collector’s standpoint, is this a permissible repair? Frankly, I don’t see any other way of salvaging it and making the parts functional, so I can’t imagine we’ve got anything to loose.
What do you think?
Hi Jane. Nice to talk with you again. Thanks for the info on LE Targets rubber panels. Their web page made for an interesting read. Stopping a 9mm makes a pellet a piece of cake.
A general question please–are Lead Dust Colectors, barrel weights, or possibly barrel shrouds more efficient with alot of little chambers, a couple of large ones or a combination of the two? Thanks much
Randy in VA
Whats up the the measurements in meters? Don’t you know us self respecting Virginians use pickup truck lengths! Anyhow, my old G1 really started to shine at 2000+rounds, smoother trigger, smoother cycle and cocking. I believe I was hitting around an inch at 20-25yards (2 pickup trucks) with Gamo Rockets. That rifle seemed particularly slow (always did seem to have a better lock time though), my more currant Storm Xt does 780-800fps with kodiaks at the muzzle and easily gets one clean hole at 15 yards with premier ultra magnums (using a bipod).
Shadow express dude
Dr. G,
I was into airsoft well before I had an airgun. I was attracted by the low cost and realism, I just used them for target practice. I had many pistols and a few rifles, enough to know that every single one has broken (somewhere in the low 40s). The only working airsoft gun I still have is a crosman R74 (the really short G3A3), but thats fairly new. Good luck and stick with airguns (or the some of the blowback metal 1911s in the $100 range).
Shadow express dude
CJr,
You might be right. Take it one step further though. Consider all you do is poor in the lead dust and old pellets into the gun. It then presses fresh new 15.432 gr 22cal pellets and spits them out exactly 900fps every time.
Ajvenom,
Sorry my post was late on my next post. Working on my Disco instead of reading blogs.
Wayne,
Will send you something this weekend. Waiting for a call back from my contacts.
There was a great internet radio cast a couple years back on the subject. I’ll try to find that too. Hope it is still available as a pod cast.
I’m thinking one of your raised gardens would be valuable for just raising fishing worms. Everything else is a bonus. I actually built one of those about 30-years back because the soil was so bad you could grow anything. I no longer own that house but the darn thing is still there. I would have thought the wood would have rotted… but it didn’t.
I love this stuff –
First: To EJ and the flashpoint guys – you’ve now got it right. Flashpoint is not only a scientific term, it is a legal one, used by the DOT, NFPA and International Air Transportation Association. “Ignition Point” is non-descript. The one we care about is “auto-ignition point”. Any oil in the chamber will detonate when the pressure raises the temperature to this point. Air-gunners call it “detonation”. Most engineers call it “dieseling”. It is exactly how diesel engines ignite fuel – by compressing the air in the cylinder to this temperature.
To Mr. B:
These panels are amazing. I have been shooting into one for over a year – and it just keeps sucking up the pellets. What is really nice, (if I can ever post a picture), is what a carpenter did for me. Built into the wall, in a finished game room, he put 2 of these panels – giving me 4″ of rubber. Behind it is 1/4inch steel. In front, a hinged mirror.
All you see is a nice, framed mirror. I open it, shoot pellets, AND 22LRs. (It will stop a 9mm, but they blow a few bits around). The pellets just disappear into the rubber. (needs to be at least 500FPS)
For LDC’s – the more chambers, (baffles), that the pellet passes, the greater will be the effect of damping the high-pressure air behind the pellet.
Shrouded barrels are a bit different. There, a void, (chamber), at the barrel-end “buys time” for the pressure wave to enter the shroud space before the pellet leaves the exit hole. That void, (I’ve seen them from 1 to 2 inches), is tricky. If it’s too large or too long, air can get around and in front of the pellet, and the effect is diminished.
In both cases, diameter is the next most important variable.
Does anyone know where I can get an LDC?
DB,
Great, look forward to hearing from you.. We use port orford cedar in our garden bed kits, and it can last 30 years..
Wayne
“Anyone read the news about the moron who shot his wife in the back with a pellet pistol here in NJ and she died?!! On top of that, the leading NJ paper had an editorial about how dangerous pellet guns are and to keep the law the way it is – a pellet gun is considered a firearm. What a state I live in. Every time I think I’ve come across a candidate for the Darwin award, someone else tops it.”
The story is here:
http://www.nj.com/news/index.ssf/2009/01/passaic_county_woman_killed_by.html
What’s really interesting are the Comments at the bottom of the article.
. . .Airsoft Adventures (part 3)…
The 2nd airsoft gun I presented to my son was the “Tactical M92 CO2 Version, Black Non-Blowback Pistol” (that is actually how PA lists it) for $50. This realistic looking pistol came in its own little briefcase with a very impressive (viz., it worked reliably and intuitively) sliding mechanism which closed it quite securely. The strong, attractive (as far as a toy case goes) case was very nicely foamed inside, similar to the cases that I use for my $1,000 airguns. This case reminded me of the case that my James Bond kit came in when I was about 10 years old. A big difference was that my James Bond suitcase could fire a plastic bullet out the back if someone was following me…certainly, not 350 fps like the modern airsoft toy, but clever nonetheless.
This pistol was also very well received, as it looked very real and had a good feel to it, not like plastic but more like metal.
This gun, as with all the rest of the airsoft pistols we came to experience (both spring and CO2), loads about 15 bbs very easily into a magazine that is held in the handle. The loading was really easy, even easier than in the original $250 Drozd bb machine gun (the new Drozd is easy to load).
The trigger was fine for the kids to accurately shoot each other and to reliably shoot small plastic bottles (e.g., vitamin bottles) up to about 20 feet away.
Something that impressed me to no end was how many shots the pistol effectively dealt per CO2 cartridge. One has to remember that these .12, .2, and .25 grain bbs are on the order of 1/25th as heavy as a real steel bb (which weighs about 5 grains) or about 100th as heavy as a .22 pellet (weighing about 16 grains). So, it should have come as no surprise that instead of getting about 50 shots per cartridge, you get about 150 shots per cartridge. For me, that makes a huge difference in fun.
One of the reasons that I have used my .177 Beretta CO2 pistol infrequently and my original (single 12.5 CO2 model) Drozd infrequently is that one has to change the CO2 cartridge after 50 shots. For me, because both these pistols are so much fun to shoot and shoot 50 shots so quickly, it becomes a chore to change the CO2 two or three times in the middle of having so much excitement. Sort of like the restauarant that became so busy because it is so good that nobody goes there anymore…
So, I really like how long CO2 works when it is used to shoot little plastic balls.
Along with the pistol I gave the boy a Crossman Auto Reset Electric Airsoft Target for $15. This black plastic target is composed of three plastic paddles of difffering size which can be knocked down and then rise again on their own. That is what it is supposed to do.
It worked really well (at 20 ft.) and everyone had fun. The target started to develop holes in its plastic base from stray shots, and the paper covering the paddles flew off (as the reviewers said it would) and simply needed to be taped on.
It kept working. The rifle kept working. The CO2 pistol kept working. When we used heavier bbs (.25) the target developed more holes, and when we used the light bbs (.12), we missed more often. So, the best bbs to use are the .20 grain, and as you will see if you have the patience to read through all the parts of this review, this suggestion pertains to all the types of airsoft guns (spring, electric motor, CO2).
The .25 grain bbs hurt much more than the lighter bbs. If one wears 2 (or especially 3) layers of loose clothing which hangs on the body like a curtain, with air between the layers, then the bbs causes absolutely no pain. Sometimes, at 40 or more feet, a boy hit by a bb may not know it. But I pity the poor fool who dares to be hit within 50 feet by any of the airsoft armamentarium whilst wearing only 1 layer of clothing…or, heaven forbid, gets smacked on his naked skin!
All of the boys wore woolen stocking caps and eyewear whenever shooting each other, and after 12 intense days and many nights, there were only two very small accidents…and I already told you about mine with the spring rifle.
The third gun I gave him was the Tanfoglio Witness 1911 Pistol packaged together with a Sticky Target for a mere $25. This gun was packaged in that hard clear plastic that, when you are finally able to cut or rip it, leaves razor sharp edges and sends people to the emergency room with deep gashes in their hands and fingers.
This packaging, which I encountered later when I gave him the electric airsoft rifle and also the other spring pistol, was the worst part of the entire experience. If I had known when I was ordering the guns that some of them came with this packaging and others, similarly featured and priced, came without this packaging, you can be sure that my decision making would have been a lot easier in terms of eliminating a whole bunch of airsoft guns.
This spring pistol was crude compared to the other two guns, which is to be expected based on the price and the fact that a $12 target is thrown in as well…leaving the company with about $13 to spend on the gun. For $13, you get a lot. But $13 these days is a little.
The gun was easy enough for everyone to cock, but compared to the semi auto CO2 pistol, this gun seemed like one was shooting in slow motion. It looked like plastic, the trigger was not as good as that on the CO2 pistol, and it did not shoot as accurately nor hit as hard. It also sounded like a toy, whereas the CO2 pistol sounded cool, like one thinks a silenced firearm might sound.
After some more experiences shooting the different airsoft guns and some of the boy’s spring guns, I became more impressed with the CO2 pistol. I was so impressed and curious about the accuracy of this airsoft gun that I decided to scope it and see what it was capable of…(Part 4 Later..)
– Dr. G.
. . . . Airsoft Adventures (part 4)…
Scoping these airsoft guns was challenging. I had all manner of airgun scopes and different size rings at my disposal, and even had some “Tacticall XX-Treme Laser Scope” and Weaver attachment hardware from the Beretta pistol that I was able to employ in my attempts to fit scopes onto these pistols and rifles.
Nevertheless, in part because of the sliding cocking mechanism that some of the CO2 pistols and spring guns employed, I was able to scope only 2 guns…the CO2 pistol and the electric automatic rifle (to be discussed in a later installment).
The CO2 pistol was able to shoot 5 shot 2″ groups at 20 feet, which opened up to about 4″ at 30 feet. The sniper rifle, unscoped, was able to shoot 5 shot 2″ groups as well at 20 feet.
The 4th gun I gave the lad, a spring pistol, was a “Air soft 904 Government air sot pistol” for $19, and at the same time I gave him a “Daisy Airsoft Electronic scoring Target” for $25.
The pistol, although a different brand and name, was virtually identical to the other spring pistol, right down to the plastic hardshell wrap that had become my nemesis. The target was supposed to count down 10 seconds of shooting by each shooter, and also add up the number of hits and show this in a digital color display. It also made cool noises depending on where it was hit (4 different noises), sounds like a ricochet or something breaking. It had 4 different settings for games like “horse” and other odd combinations of electronics that offered unusual scoring and counting. All for only $25. Yeah, right.
The target sort of did what it was supposed to some of the time with some of its 4 settings, enough so that the boys were entertained by it. After a few days it didn’t really keep proper score in any sense of the word. The cool noises stopped as well.
By this time the floor had about 3,000 bbs on it. I did not know what was coming next… (Part 5 Later)..
– Dr. G.
. . . . Airsoft Adventures (Part 5)…..
The 5th gun that I gave to my son was the “Air Mag CO2 Blow Back sub machine gun Hop-up, Semi-Auto” for $75, along with what proved to be the Best of the 4 Targets, the UHC Deluxe Airsoft Mesh Target Trap for only $10.
I should begin by pointing out that both the sticky target and the noise/scoring target effectively collected shot bbs in trays. The paddle target did not collect bbs, and also by this time (after 6 days of use) it had begun to show wear and tear…
…it was full of holes, and one of the paddles was permanently down for the count. This caused the machine to make a constant whirring noise, which went on non-stop for several more days (kids are oblivious to the annoying nature of noises) as the machine had no on/off switch.
This new CO2 gun (which is called a submachine gun but does not feature automatic fire…go figure)held many more than 15 bbs, making it a lot of fun right there. By holding 50 bbs, it reduces the frustration of reloading, which is a major hassle in the world of airsoft. It had blowback action, and so it felt very impressive. The trigger was very easy, easier than on any of the other guns so far, and so this was seen as a lot of fun.
However, it just was not as accurate as the other CO2 pistol, and it was absolutely impossible to fit a scope on it. It also shot about 120 shots before needing a new CO2 cartrigde, probably because it needed some CO2 to blowback.
By this time the speed loader to the spring rifle broke, and it was impossible to load it or shoot it. No big deal, as the boys had decided that it was too big, too heavy, and not fast enough in cocking to be of any use in the forest. It was also deemed to be of little fun at the indoor range, and so when one of the boys brought a replacement speedloader, the rifle continued to languish against the wall.
I was impressed with the last target system, which was an 9″ square (big for airsoft targets) platic frame with a sheer net behind to catch bbs. It allowed paper target to be easily placed in its frame, which was simple and effective to open and close. This never broke, and is my current favorite target system for the airsoft gun.
The last gun I gave to the kid, and the gun which stands out as two levels above all the rest of the guns, the gun which I personally found really fun to shoot and was so impressed with it on so many levels, will be disclosed in the final segment (I have learned to do this from BB),..(Part 6, Later)..
– Dr. G.
Randy-from-VA,
I highly recommended the GRT III trigger. I’ve had a G1 Extreme for two years, and other than a spring replacement, have had no problems with it. I have to say that I easily have over 10,000 pellets through it and it’s still a great shooter. The GRTIII trigger is an outstanding investment. It is truly an eye opener.
Kind regards
Michael in Florida
Success is not an entitlement.
Shadow express dude – Where in VA are you? I'm in Chesterfield.
Sorry about the metric reference. I have a short garage so I bought some 5 met…(excuse me)…16 & a half foot targets for my bullet box.
Michael in Fla – Thanks for the feedback – now I HAVE to get one.
SED,
Lead alloys? I will address it.
B.B.
Vince,
When it comes to the really old BB guns, any repair removes a lot of the collector value, but what you propose is exactly what one of the top airgun restorers would do. It’s the best way to fix it and I say okay.
That gun doesn’t have much of its collector value left either way, and by fixing it, I think you actually give it more value than if it were just left alone.
B.B.
Thanks, BB… that’s the conclusion that Wayne and I came to. Wifey is going off to Walmart soon, and she’ll be looking for a nice, cheap leather belt to make new seals from. I’m also going to try to find a new spring for it since the old one is, well, old…
One interesting thing about this BB gun is the way it’s constructed. The attention to detail and care in manufacturing is… well, let’s just say that it was obviously considered a toy.
I hope to get it running again today, if I do I’ll post the results.
Dr G,
Since you are a Medical doctor I feel obligated to let you know about my high blood pressure. Leaving me hanging on the airsoft gun could possible put it over the top; don’t you take some sort of oath?
Volvo
Dr. Dr. Dr.
Help fast, I need the perfect air soft gun!!!
Your worse than B.B.!!!
you tease..
Wayne
Matt,
Sounds like you had a good trip. Congratulations on the drill. I’ve had a dozen or so over the years, but some of them you don’t forget, especially the first:).
230 yards is a good range; probably about 15 inches of drop, and a lot can happen b/t muzzle and target. Remington has online ballistics and comparisons, plus a free software download for their c/f ammo that can’t be beat for the price:).
Did you get the sister-in-law to join the NRA?
Dr.G.
Don’t forget the clean up!!!
Or do you have a permanent Air Soft room?
Wayne,
Ashland Air Rifle Range
RE: Index
EJ,
Before you spend an awful lot of time on this:
(1) How is it going to be posted?
(2) How can it be updated?
Herb
Randy in Va,
No way, I’m in chesterfield too. My neighborhood is the Highlands. Which part, chesterfields kind of big. Were actually down beach road.
Small world eh.
Don’t tell me your in woodland pond!
Shadow express dude
Special Announcement:
4 Days
21 Hours
30 Minutes
Lead Recycling:
Keep in Mind
Wayne’s next airgun purchase:
2 seconds (he he)
I hope the next big thing doesn’t come with a long waiting list like the Discovery. I was on the list until I decided to by a .22LR rifle. Yeah I said it. I bought a firearm. oh well.
I do have a bullet trap which I did not line with anything this time and it’s getting full of lead. Although, I did shoot some crosman non lead pellets in there too. I wonder if I have to sperate those out? They really did suck to be honest. I wont be buying those again. BBs would have been more accurate.
Morning Jane Hanson. The LDC that I am using for my Talon SS came from Van at Air Hog. Works well very very well, esp the one for the 24″ barrel.
Wayne, can you help Jane also? If my three exisiting brain cells are all firing properly I am remembering that you had some LDC’s made for you by Anthony. Thanks
ajvenom,
One of the first things I’m going to tell you to do is get rid of all the non-lead pellets in your waste. So I hope you can see them and I hope they’re not more than a few.
As for the next Crosman PCP, which may or may not be called a Discovery, I plan to photograph it the first day of the SHOT Show and show pictures and specs in the next morning’s blog. So that would be next Friday.
B.B.
Thank you Dr. G,
Your multi-part comments are an easy read and entertaining as well. I feel a small window opening up in my airsoft void. Your forthcoming Part 6 might just loosen my purse strings again (no I don’t carry a purse that’s just a euphemism).
What’s really going to cost me is Jane’s recommendation of LE rubber. The 2’x 2’x 2″ sheets weigh 37lb and cost $43. I wonder what the shipping cost will be? But I must have one (or two). Thanks for the tip Jane. I’m just about to reach dirt on the other side of my basement wall:) Actually I have 4′ x 6′ x 3/4″ plywood covered with two layers of thick carpeting.
-C
. . . . . Interim Airsoft Note . . .
There is currently a snowstorm arriving here, both in the form of outdoor precipitation and in the form of my son and his crew of 4 inhabiting the basement (which is a huge finished area totally devoted to play, including guns and whatever else) since too early this morning.
They are shooting all the airsoft guns, and so while I was doing the usual Sat. a.m. chores I bought them some “gun soap” (Neutrogena, the translucent gelatin soap for the discerning face) to shoot into and test the power of the guns.
When I went by one of the boys was shooting the BEST airsoft gun, the one that I will be reporting on in Part 6. I could not resist but request a quick turn…
I took my seat, aimed at the target which was about 15′ away, [the BEST airsoft target, as described in Part 5, above], and blasted about 25 shots into it. The 25 shots created a slightly oval shaped hole about 1/2″ above the bullseye where there had been paper seconds before…
…It had hit 1/2″ high because I had forgotten that this gun was sighted in for 20′, and the target was at 15.’
Anyway, the gun continues to perform flawlessly after more than 7,000 shots by a combined 6 different users. I find that the fact that the gun works with so many users to be particularly telling.
In my experience, machines and users work together ove time, and the idiosyncracies of each work themselves out. When a new user begins with a machine, it stresses it in new areas (sometimes due to ignorance of the new user) and this is where many malfunctions occur.
As I said, this wonderfully accurate (1″ group at 20 feet) and amazingly reliable airsoft gun will be revealed and described as soon as I have time to complete the series, hopefully later today.
– Dr. G.
Shadow express dude – I’m in Hampton Park (the last light on 360) I have friends in Woodland Pond. Small world. BTW, I ordered the GRT-III this morning.
Dr. G – You should shape your basement floor so that all of the plastic BBs collect in a sump. It would save a lot of vacuuming, and the boys (of all ages) can keep shooting them over and over.
That idea about machines and users is so true. My daughter proved it with the transmission in my SUV. That sure cut into the airgun budget.
“That idea about machines and users is so true. My daughter proved it with the transmission in my SUV. That sure cut into the airgun budget.”
Lol– I’m glad I learned to drive a manual transmission from my dad. My grandfather on my mom’s side had a ’66 or ’67 (I can’t remember which) Mustang. My mom is one of three sisters, and he had to replace the clutch three times. Incidentally, those clutch replacements were all about the time that each of them graduated from high school, but never again after that. Draw your own conclusions.
This morning my wife & I were discussing the NJ woman who died after being shot with a pump-up airgun. We wish there'd been more info about the gun and circumstances. The pellet (.177, .22, .25?) would have had to go through clothing. Did it collapse the woman's lung, what? Did he shoot her out of irritation, thinking the pellet would be relatively harmless? Was it really just an accident? We've all seen discussions on this blog of airguns whose sears were filed down too much; could it have been this, or did he think the gun was unloaded? So many questions.
One thing for certain, it makes me even more mindful of airgun safety (and I'm already anal on that score).
Vince et al,
Re: Fixing part on Markham Model D
Of course if you fix it now you can shoot and enjoy it. Not sure what it may be worth as collector’s gun, but you may be able to find a “parts” gun from which you could salvage the repaired piece. If its working now and you can play with it, who cares if it takes a while to find a parts gun.
I’m assuming that if you use “original” parts from two guns to put together one working gun, then that working gun would be considered to be “original.” Correct?
Herb
BB said “As for the next Crosman PCP, which may or may not be called a Discovery, I plan to photograph it the first day of the SHOT Show and show pictures and specs in the next morning’s blog. So that would be next Friday.”
Is this true? Am I the last to hear of this? Jeesh,…even more money will be leaving my wallet unexpectedly.
Dr. G,…I would have expected you to be 1/2 inch low at 15′, if your guns was sighted at 20′. hummmm?
I read quite a few articles last night…I thought I saw a picture of a Crosman G1 Xtreme alongside one of the articles about the New Jersey wife that was shot accidentally by her husband.
http://wcbstv.com/local/nj.man.shoots.2.900521.html
All,
Get the new Outdoor Life. Two-page spread on airguns. The reviews themselves are worth much, but it gives credit to our sport.
Volvo
Dr G,
You are quite the tease. Those college girls “gone wild” have nothing on you.
The snow is bad here too; the girls are in the basement so my shooting area is on hold.
They are making up routines to Grease songs. I could join in and post it on you tube. Any takers?
Volvo
ps I forgot “not” before worth above
Volvo,
Wasn’t Grease choreography the thing for girls when we were kids? Better than what passes for entertainment these days, anyway. Rain here (wishing for snow), so the boy and I watched “Dodge City” — not bad at all, though Erol Flynn as a cowboy takes some getting used to. Something about your YouTube offer brought it to mind is all:).
Hello:
I have an unusual problem. I was refilling my Talon SS with the AirForce Handpump. Filled the tank up to 2900 psi, I bled the valve, and then unscrewed the tank off. I noticed that after bleeding the valve, the pump’s shaft was still raised as if air was still inside trapped even though the bleed valve AND the tank were unscrewed. What happened?? What can I do?? The pump is now useless because it won’t fill anything, it somehow has air trapped inside. The weirdest thing is that the manometer is not registering any pressure at all, it is at zero. And to top it all, I started pumping air w/out any tank attached, and now the shaft is completely raised. It is extremely hard for me to push it 1″ down. HELP!
Chris
Well, I brazed the busted Markham part, made new seals (simple discs) from a leather belt, and got it all back together.
It shoots steel BB’s at about 170fps, which is fine. I then tried shooting a group of 5 at about 16′. I got a ctc of about 1 1/4″, strung left to right – elevation was very consistent.
I’m pretty tickled with that. Especially since the gun has a barrel made for LEAD BB shot, which is bigger. So the steel stuff is gonna rattle around a bit. And ESPECIALLY especially since the gun doesn’t have a rear sight!
Vince,
Bravo!
I can’t wait for the 499 barrel.. then gradually add larger springs until the coil spring from the rear of the ford 1 1/2 ton truck…(isn’t that the size you figured for us Jane?).. that’s going to be one custom gun.. watch out gamo.. we can claim 10,000fps even if we only get 4,999 like Vince plans.. I don’t want to give too much away.. but when you fire it.. it becomes a large skate.. very fun.. too bad we missed this Christmas..
But I don’t know if it will match the photo we have in the catalog..
Vince are you sure we will be ready for the shot show?
If not just fake the proto-type.. no one will expect us to shoot it at the show… we’ll dub a video..
Whacky Wayne
Ashland Air Rifle Range
home of the fast b.b. gun on the planet.. and taking orders… prepaid orders.. that is..
Chris,
I cannot believe you are writing this! The exact same thing happened to me two weeks ago, after using my pump about weekly for 1 1/2 years with my Condor.
I was already on the phone with PA discussing warantees and costs of new pumps that afternoon, because it would have been hard for me to have been without the gun for very long.
Anyway, long story short, a day or two later I returned to the pump and it was working fine.
– Dr G.
Last week I bought a Crosman 2250B from PA. It arrived a few days ago. Here is what I think of it.
Crosman 2250B air rifle, carbine with 4×15 scope, .22 caliber, CO2
1/7/09, 2 PM:First impressions:
UNPACKING:
• Gun seems thinner, lighter than my old SSP 250, the trigger pull is heavier; trigger also seems a little thinner (I want the trigger shoe for it)
• Bolt seems to pull back against a spring. Takes getting used to but eventually becomes a non-issue
• Gun comes with cheap little 4x scope un-mounted (HOORAY!)
• Rear sight is too large for carbine use. It gets smaller as you hold the gun out at what would be pistol length, so that the front sight ‘fits’ tighter; best to reverse the rear sight to its peep configuration
SHOOTING:
• Quick read of instructions
• Load CO2 cyl with drop of Pellgunoil on its tip; the first test shot is a no go (thought I might have to tighten with a quarter on the slit at the end of the filler/charging cap) but then YES! The shot sounds the way it’s supposed to.
• I’m using .22 Copperhead Wadcutters, bought back when I first got my Gamo Viper Express several years ago.
• Fired first into backstop at end of garage; 2nd into 1’ diameter copper gong hung 35’ away (nice ring when hit). 3rd into a scrap of 2×6 redwood flooring, left over from building my last deck; it made an indent the length of the pellet but then bounced back out.
• Soda pop can from recycling, set at 20’ (on dirt so I could see when I missed but I didn’t); then back to 35’, then out to 40 paces where I used a combination of the sights and The Force to hit it. I was already getting into a rhythm of opening the bolt, loading, closing the bolt, then shooting. But cold rain and sunset were taking the fun out of it for me.
• Found fired pellet next to can; it was powerfully crumpled; can was history.
• Out of cussed curiosity, I tried firing the rifle with the bolt open and no pellet; the bolt shot home…there was no obvious damage but I won’t need to repeat the experiment.
• Pretty loud; last time with SSP 250 had 150 acres to shoot on, then 40 acres, now 3. Conscious of neighbor’s house near garage…otherwise fine. Wonder what 18” and 24” bbls would sound like. I read a PA review saying the 24” bbl was past the point of diminishing power returns, but I don’t know how scientific that was.
• Overjoyed to once again have a reliable ‘go-to’ air rifle! Like the ‘80s with my SSP 250, skeleton stock and inexpensive variable-power .22 rimfire scope. I had used that rifle so much that I knew what it would do at most any range and with any particular pellet.
I want to try it with the scope next time. Safety instead of prescription glasses make target difficult to acquire much beyond 50 paces for these old eyes.
-Joe B.
……..Airsoft Adventures…(Part 6)..
Although I thought that I had gotten a good deal when I bought the Crossman Air Mag M50 for $70 marked down from $100, I was starting to wonder after shooting all of the other airsoft guns that were starting to accumulate in the basement and after having observed the boys through the weeks.
Based on how often the boys (or me) for whatever reason chose to pick up and use the various guns that have been discussed, the CO2 TSD Tactical M92 pistol, (I see marked down to $40 from $80 now by PA), was definitely the best value (in the Wal Mart sense of good product for less than one would expect to pay) of all of the guns.
However, the gun that was shot more than twice as often as any other, and because it was often fired in automatic fire bursts probably ended up responsible for about 10 times as many shots as any other gun, is the clear winner as far as I am concerned, and I think that you will be rewarded for sticking with me this long with an opportunity to buy this airsoft gun yourself.
The gun that I am about to name was marked down from $130 to $80, and so it is not in the same ball park as a $20 or $40 gun. That is why the $40 (or $50 when I bought it) Tactical M92 pistol wins the “Value Award.”
The $40 M92 was, because of its accuracy, trigger, ease of use (changing the CO2 and loading bbs), and reliability, about 4X as valuable as any of the spring pistols or rifles. That is to say, if the M92 is valued at $40, then any of the spring guns are worth, to my observations, about $10.
Using this scale, I would say that the $70 M50 blow back CO2 was actually worth about $30. Probably due to it being less accurate than the M92 (mebbe cause of blowback, who knows?), it was used less often (but more often than any of the spring guns).
Using the above financial judgment scale, the $80 gun that I am about to tell you about is worth in reality about $120. That is, if I were offered one of these or 3 of the M92 CO2 pistols, I would say that the offer is equal in value.
Before I give you my full endorsement (I have a reputation of sorts here) of this airsoft fun gun, I am curious about something.
One of the anon. posters noted that if the gun was sighted in at 20′ then it should have shot low, not high, at 15.’ So, before further ado, I am going to shoot the gun right now to see what is happening with this phenomenon, and try to continue Part 6 before the evening is out, so that I can tell you all about this amazing, accurate airsoft bb machine gun that never needs refilling with CO2 and is as easy to load as fillng your mouth with pie.
– Dr. G.
Dr.G.
Just testing us aren’t you?
This is some kind of experiment, right?.. Tom, doesn’t tease us this bad..
I don’t really want one, .. just as a gift or something..and I can’t wait to hear.
don’t forget how you cleaned the floor!!!
Great guest blog!!
Wayne
Dr.G,
Just off the holidays we are all pretty good at stuffing our mouth with pie. Are you sure it is that easy?
DB
B.B.,
A while back you stated PA is getting a lot of scopes returned. So I’ve been watching the used section hoping to pick one up. Not seeing too many scopes there.
DB
2250B review, Part 2
1/10/09, 3 PM: Today I mount a scope, and target shoot at 30’. I am shaky from a cup of coffee, even though it’s decaf, so it’s difficult to work all the small pieces, with their tiny little screws. The rifle comes with Crosman’s 459 MT intermount, which clamps onto the rifle’s barrel and allows you to connect the scope mount to it. It wobbles in place if not hard-tightened with the small hex key that comes with it. I try tightening the scope mount rings onto the intermounts first, but then realize the intermounts open a bit at the top when attached to the barrel first, allowing the scope mount screws to be tightened without stripping them past where they are meant to go. With no scope, the intermounts are low enough to still use the open sights.
Years back I bought a Tasco rimfire 3-7×20 scope for my SSP 250. I prefer the variable for the 2250B, but decide to try both scopes. I start with the Crosman 4×15, because in theory at least it was designed to be used with this rifle. Crosman scope’s rings appear to be soldered to the scope tube; the scope cannot be moved rearward enough for my eye. The Tasco scope can move within its rings so I put it back on. At 7x and 30' the target is a little fuzzy. I decide to use it at 4x, and later I will read the instructions about how to focus the objective. Perhaps I will attach the Crosman 4×15 to my Viper Express, for when I’m not using it as a shotgun.
What was Crosman thinking? Neither scope adjusts far enough back for a clear sight picture; I finally get the sight picture looking barely correct, but the Tasco’s rear ring now rests on thin air, ¼” off the rear Crosman intermount. Also, my head is too low for the scope. I rubber band a double width of hand towel around the skeleton stock, then double it again when my head is still too low. I will replace this with something more permanent later, but for now the rifle and I are still getting used to each other. I wouldn't much want to carry it afield with a towel wrapped around its stock….
I paste a 2” sticky target on a cardboard box and set it 30’ from my makeshift benchrest.
I begin sighting in with a partial tin of Crosman Copperhead Hyper Velocity wadcutters. I nestle the rifle into a beanbag chair atop a folding table. My hand rests lightly atop the small scope. For some reason this reminds me of the movie, Shooter. The crosshairs shift slightly right and left with the beating of my heart.
My first shot is a little low and a foot to the right. I loosen the intermounts and push them a bit to the other side of where they were (I also make up my mind to buy Crosman's long steel receiver; it will give me a mounting surface that doesn’t shift like these intermounts do). This gets my POI closer to the bullseye.
I forget to notice that my CO2 cylinder, left over from last Wednesday's trial run, is running low. I adjust the crosshairs higher two times before it dawns on me that the pellets are dropping to the ground only 10 feet in front of the muzzle. A drop of Pellgunoil on a new CO2 cylinder and I am back in action. Next session I will count my shots, to see when the pellets begin to significantly drop below POA.
I watch my dwindling supply of wadcutters with dismay. I begin to wonder if I can finish sighting in before I run out. I went to my favorite gun store recently to restock, only to find that the only .22 pellets they currently carry are Crosman Pointed Field Hunting pellets. I buy a tin out of desperation. Fearing POI changes, I do not want to switch ammo until I’ve got the scope zeroed with the wadcutters. I wish I had Premiers. In the ‘80s, when I was teaching my kids to shoot and we shot almost every day, the local sporting goods store carried every brand and type of pellet imaginable. These included Beeman felt cleaning pellets, which were great for shooting flies indoors.
I begin to notice the slack in the trigger, and can reliably take it up right to the point where the trigger breaks. This helps, but the gun seems also to recoil upwards slightly with each shot. I will take that more into account later on, as I get used to the gun’s shooting characteristics.
After adjusting the cosshairs up, down, left and right several times, back and forth, they finally settle in to a usable sight picture. I’m not going for Hawkeye accuracy yet; there are still too many variables until I use the rifle day in and day out. But for now, I’m pleased. I switch to the pointed hunting pellets. The POI is pretty much the same as the wadcutters. If I am going to have to adjust my aim each time the CO2 cartridge begins to run out, dropping the POI lower, I believe I'd do better with a mil-dot scope…perhaps Leaper’s Bug Buster that I’ve been eyeing for awhile now.
I am now using The Force, which is a combination of s-q-u-e-e-z-i-n-g the trigger and yanking it as the sights swing past the bull. This is how I’ve always shot and it works well for me now. After a while of hitting the same hole, I content myself by moving the pellets around, trying to create one large orange-colored hole. I pretty much succeed. The whole spread is 1” C-T-C. I have now been at this for two hours. I oil the rifle and both scopes and put them away. I leave the rest of the CO2 in the rifle because B.B. said I can without hurting the rifle’s innards.
Next time I’ll try to come up with some interesting targets, in order to become more comfortable with this rifle by continued practice. I tried my local sporting goods/gun store for swinging metal targets recently but all they had was a heavy one meant for up to a .44 magnum. I doubt if the 2250B would even move the paddles, much less spin them! The goal now is to shoot it as often as possible, until I know it forwards and backwards and inside out. This I’m looking forward to with much pleasure.
I may have to break down and order a variety of pellets from PA, even though a 4-tin, $25.77 order of assorted Beeman .22 pellets (felt, Silver Jets, Crow-Magnums, H&N Match) costs $36.30 to have it shipped here to Hawaii. Until then I’ll shop around locally to see if I can’t find some at a more reasonable price. If anyone wants to suggest the most accurate pellets for this rifle with its 14+” bbl, I’d be much obliged.
-Joe B.
Vince,
Is the Marksman missing a rear sight or never had one? I’m guessing its missing, but your description of its quality construction makes me wonder. 1 1/4″ at 16′ with no rear sight from an oversized bore is pretty good, and its nice to see you happy with 170fps:).
Wayne,
If you were a big airgun company, you would start shipping. Perhaps have some of the gun mags write “reviews” praising the hand-crafted attention to detail and the flat trajectory, raising doubts about the current competition. Then, go off the books and ask some young kids to YouTube a hunt for rabid coons to build the buzz.
Crosman Pulse R72 Black by Crosman
…….Airsoft Adventures (Part 6 cont.)…
Well, I could be a Smart Alec and report to Anon. that the Crossman Pulse R72 Black Electronic Full or Semi Auto Rifle has an “adjustable hop-up mechanism” which makes the plastic bbs underspin (like a fastball) and thus they can shoot high or low (or in the middle) at different distances depending on how you adust it [which is true], but the fact of the matter turns out that he is correct.
I do not know why I shot high earlier (I exclusively use scopes on all my real bb and pellet air guns and am not accustomed to open sights), but when done corrrectly (as I am about to report), the gun does shoot about 1/2″ lower at 15′ than at 20.’
The point that I was emphasizing with my telling of that anecdote was that the Crossman Pulse R72 easily blows a 1″ hole in the target in a matter of seconds…The only real air gun that I know of that can touch this is the Drozd bb machine gun, which sells for over 3X the price (and requires CO2)…and even with that, to blow a 1″ hole in the paper using steel bbs takes a lot longer than a few seconds, believe me! The whole dramatic effect is lost when it takes more than 5 seconds (for example, watch how long the longest continuous shooting scenes last in the movies, even in the extreme scenes directed by Eastwood or in the continuouos fire scenes with Pacino’s “Little Friend”).
Anyway, to return to reality, with open sights and shooting semi-auto from a bench (and my eyesight is only 20/25 at best with corrective lenses), at 30′ a 6-shot group of 2-2 1/2 inches is easily reproducible. This, by the way, is after my son (completely on his own) put white-out on the sighting posts of all the airsoft guns, or I don’t know how I would have done. This level of accuracy is comparable to an unmodded Drozd bb machine gun.
More impressive, however, is that at 30′ and shooting in automatic mode (about 6 shots per second), the gun easily produces 3″ groups. This is better than the Drozd in automatic mode. Why?…
To answer that question, we move to the attraction of this gun, which lies in its energy delivery system. It uses an electric motor and a rechargeable battery that hides in the stock.
The battery, for some strange reason, comes with (2) directives, one of which is written all by itself on a day-glo orange card warning that the battery must be charged at least 4 hours and not more than 6, while another is prominently displayed in the booklet that accompanies the gun, strongly warning that the gun’s battery must be charged at leas 5 hours and not more than 7.
For what it is worth, there are other strange directives and admonishments (for example warning about the “ill use of shooting beasts”) accompanying some of the airsoft guns, sort of like what you sometimes get when dealing with ShinSung literature or other foreign speaking companies of which that are the Asian.
The electric motor (and everything else about this gun) works as described in the many glowing evaluations of this airsoft gun to be found on the internet. The battery lasts a really long time…probably over 800 shots, mebbe over 1,200.
The gun features really good ergonomics (interface between man and machine). The large switch, for example, which places the gun on safety, semi, or full auto is outstanding in terms of how it feels, how it is shaped (slight curve, slight indent), the amount of force required to move it (enough so that it will never accidentally move, yet not so much that it cannot easily be done with your thumb while your finger is on the trigger)… even the placement is perfect.
And that is just one switch! Loading the rifle is fast and easy, as the bbs are simply poured (about 350) into a cigarette box sized resevoir. The rear sights are adjustable for windage, although the one tiny fault with the rifle is that no matter how I adjusted it and no matter what weight bb I used, the gun shot about 1″ to the left at 20′.
The rear sites are also adjustable by a clever rotating mechanism that gives the user a choice of open or closed rear sight, and size (i.e., 4 different rear site possiblities).
The rifle is perfectly weighted, neutral. Nothing sticks out to make it awkward, such as in the blowback CO2 pistol described (see Part 5) earlier, which has a really long magazine that prevents it from being held as a pistol, yet it is too short to be held as a rifle.
After loading, there is a plastic wheel at the bottom of the loading resevoir, the lower 1/8″ of which sticks out from the box, that must be stroked about 70 times (takes about 20 seconds) so that the bbs get from the resevoir to the barrel. This stroking (winding) must be done about every 220 shots.
The electric motor, as opposed to the Drozd CO2, produces identically powered shots every time. The Drozd, by the 4th shot on auto, is already slowing down and getting less accurate. So, at 30′ and on full auto, this airsoft gun is a bit more accurate out of the box.
At 25′ this airsoft rifle shoots on semi-auto 6-shot groups of 1 1/2″ ; at 20′ the 6-shot group is reduced to 1″; at 15′ the rifle produces 1/2-3/4″ groups (!!); and at 13′ a 12 round burst of 2 seconds prduces a hole of 3/4-1″.
Importantly, the gun makes a really cool sound when it fires…I do not know how to describe the sound of the little electric motor compressing some little amount of air and then sending it out (or however it works, perhaps a reader can tell me), but it is not an instant and abrupt sound, but rather a slower, drawn out sound, beginning with an electic whirring and ending with a slap, almost like it had 2 syllables…
…on the airsoft blogs there are complaints that it is “loud.” Mebbe compared to other airsoft guns, yes, it is loud. But I am sensitive to sound (most of my real air guns are shrouded, inlcluding some of my Drozds), and I assure you that this airsoft machne gun makes a pleasant sound on semi-auto and a necessarily aggressive (yet interesting) sound on full auto – I would not complain that it is loud.
So there you have it…Oh, those bbs on the floor. It turns out that they can be re-used. It also turns out that they are much more expensive at the local TSA than originally thought (where we ended up going after the first 15,000 were used up and we had no time to wait for PA), so much so that it became prudent to pick up the 7,000 from the floor rather than shop-vac them up as originally planned.
Since they are big and light, they come up easily, and because they tend to pool in groups an adult can pick up 2,000 in only about 10-15 minutes… Kids take longer.
Wayne,
These airsoft guns (the two highlighted in this report) are ideal at your air gun range for introducing children not mature enough for real air guns to the joy of airgunning. As long as one is wearing protective glasses then things are safe. My son learned that when you shoot something you should not hold it…(because you might miss) I am glad that he learned this using airsoft rather than a more hazardoud type of gun. This, by the way, was the 2nd injury sustained in 18,000 shots, and it was a non-crying injury so actually I would not even call it an injury…just a sore red mark of stupidity.
Anyway, Wayne, for the younger siblings aged say, aged 7-13, to set up an indoor 20′ range with these guns would keep everyone happy. Even kids who are 9-13 who are mature enough to handle real air guns will be walking back to the airsoft room to shoot the machine gun…especially if you had fall down targets in addition to paper. You could probably pull a McDonald’s, and advertise an Airsoft Indoor/Outdoor Extravaganza (Birthday Party Theme, Fun for Rainy Days, etc.) simply for the purpose of hooking the family onto the property, where you really sell them on real airgunning.
B.B.,
What do you think of my Airsoft Adventures? P.S. Things seem to be running very smoothly with your commenting less often.
– Dr. G.
RE: “… Beeman felt cleaning pellets, which were great for shooting flies indoors…”
New ideas every day….
Dr. G.
That’s why I was reading along!! It sounds like great fun.. It will come next summer..
Great report.. I, for one want to follow the kids adventures of Cowboy Dad, Volvo and yourself.. and others of course.. it’s late.. sorry if I forgot you..
Keep them coming!!
Wayne,
Ashland Air Rifle Range
Joe B.
Regarding your 2250B.
The current crop of Crosman CO2 guns use the valve stem to pierce the CO2 powerlet, so don’t over tighten the CO2 cap. I heard you mention that you would tighten it with a quarter. Finger tight is all you need. The first shot is weak because it pierces the powerlet and fills the valve with CO2. If you over tighten, you compress the soft seal and restrict the valve stem, resulting in a very small hole in the powerlet, and in most cases, reduced FPS by restricting the movement of the valve stem.
The steel breach is a must have for scope mounting. As long as you’re replacing the breech, replace the breech seal with one of Bruce Cox’s CLPS. The cost is approximately $2.50. You can email him here.
bcox@treerathunter.com
The shoulder stock doesn’t work for me, but there are alternatives, especially if you’re handy.
http://www.network54.com/Forum/275684/thread/1212842461/New+Project+%28pics%29
http://www.network54.com/Forum/275684/thread/1229802196/I+needed+to+scratch+an+%26quot%3BIZH%26quot%3B…
http://www.network54.com/Forum/275684/thread/1229987030/Custom+1377
I’ve found that Crosman Premiers in the cardboard box are the most accurate in my .22 cal Crosman guns with the 14” barrel, followed by RWS Super H-Points.
Kind regards,
Michael in Florida
Success is not an entitlement.
Dr. G.,
Your experience with the Crosman Pulse R72 sounds wonderful. When I tested one a while back, it jammed on the first try and couldn’t be cleared. I had so much trouble with it that I decided not to complete the test.
I’m glad you had a good experience, because for the very low price Crosman charges for this gun, it does offer a lot of value.
B.B.
Vince,
I hope you took pictures of this fix?
Guest blog.
B.B.
Chris,
Your hand pump has an internal passageway that’s blocked. It has trapped air in one of the internal stages, and that’s what’s holding the pump handle up.
This happens when dirt gets into one of the several internal one-way valves.
The air will leak out over time and the pump will work again for a time, but if the foreign material isn’t removed, it will continue to be a problem.
Sometimes this clears up, but usually it doesn’t.
Your AirForce pump should be returned to AirForce for repair. As long as you have not disassembled it or wiped off the outer shaft lubricant, this repair will be done for free, if the warranty period is still in effect.
B.B.
Evening Dr G. I too noticed that things were running smoothly without B.B.’s constant comments. I really enjoyed the Air Soft story. Thank you very much for the time and effort. Still waiting for more of the Whischome. Great pictures of a wonderful gun.
The Markham’s rear sight is busted off, it looked like it was simply fixed, sheet-metal affair made that was stamped out from the top of the gun (on 3 sides) and then folded up and notched. But I’m not sure.
Yes, BB, I’m taking pictures.
Vince,
I think you described the rear sight correctly. As you discovered, the gun was made as cheaply as possible with the toy technology of that day.
B.B.
B.B.,
Re. jamming of the Crossman bb airsoft machine gune…
…As it says on some internet posts, when the gun does not shoot, first check to make sure that the wheel has been wound. In our experiences here, 4 of 5 times the wheel simply needed winding (about every 220 shots) and the gun shoots.
About once daily, when the gun does not shoot after winding, simply put it on auto, shoot a short burst, and then its ready for semi auto fire if you want. This is “the fix” that the internet was very helpful with, and it never failed.
This gun just keeps on working…far more so without incident than most of the real air guns that I have owned. I will post when/if it breaks.
Mr. B: I really cannot figure out what else there possibly could be about the Whiscombe that you would like to read that I have not already addressed. If you or any other readers have any questions about any of the air guns or airsoft guns that I have written about please feel free to ask. Now that my computer is back I can read this blog daily.
– Dr. G.
So the only question is this – do I reconstruct a simple, fixed V-notch (easy enough to do)… or do I try to cook up something that’s adjustable?
The first option would keep the gun looking fairly original, while the second would have an obvious advantage. Then again, at 170fps I don’t know that it’s gonna get shot at longer ranges…
Dr. G
I have had my pulse R72 for almost 8 months now. I haven’t put too many rounds through it yet, somewhere around 1700. I find that when using .25gram balls, I can hit cans consistantly out to 35yards. .20gram balls are best for full auto because they are cheap. Never use .12grams, they are too light and will make an effect like dry firing in these stronger airsoft guns.
Joe B.,
One other pellet to throw into the fray for your 2250B is “Beeman Field Target Specials”.
All of my Crosman 13xx/22xx series guns love them the best. This is my go to pellet for pinpoint accuracy.
They are more costly than Crosman Premiers. If you are willing to spring for Crow Magnums, you are almost there. I missed the days when they were $7.25,…they almost swelled up $2 overnight.
Michael: Exceptionally nice “weapons of mass destruction” you are engineering. Very nice!!!
Michael: BB did a blog not to long ago about the ability to modify 13xx/22xx series guns. One blogger questioned why “anyone would go to the extra expense and effort” to modify.
Your unique and awe-inspiring “creations” are the answer to that blogger,…nuff-said!!!
If that blogger doesn’t “get it” now,…he/they never never will…
michael i’ll take (1) of each please
B.B.
Thank you very much for your response about the AirForce Pump. But what can I do to avoid dirt from coming in? I haven’t disassembled anything, so it is still under warranty. It was working perfectly. Must have been during bleeding the valve. Thanks.
Chris
Chris,
Dirt can come in when bleeding the valve. That happened to me on a hunt in Texas a couple months ago and ruined a 11 year old pump in one blast.
Call AirForce on Monday.
B.B.
B.B.
Well, now I know!! But you were right, when I checked the pump today the air leaked out overnight. I will use it again before sending it to AForce. If it gets stuck again, I’ll send it!! Thanks
Chris
Mr. Anonymous,
I am interested to hear from you whether you measured the accuracy differences using the R72 with .2 vs. .25 weight bbs., and what they were if you did.
I don’t think people measure accuracy differences in airsoft, nor do I think that they weigh bbs (I did, and the results were interesting to me). My sense is that it is more of a seat-of-the-pants community, in which people judge accuracy by how far away can a human be nailed and judge power and bbs by how much they hurt when you are hit, and whether they curve.
Being more scientifically oriented (I actually read all of Cardew’s book, and even was able to read several entire pages of Mann’s ‘text’), I prefer to use numbers when describing things like machines and performance, rather than subjective adjectives…
…Speaking of which, which # anonymous are you, as I suspect that you (all of you anons.) are more than one person? Thanx in advance for your answer.
– Dr. G.
Dr. G.,
Hello. What were the ‘interesting results’ you achieved by weighing your plastic BBs, if I might ask?
Joe B.
Dear Michael in Florida (and Anonymous),
Thank you so much for your kindness in suggesting pellets and further ideas for modding my 2250B.
Michael — I have a date with a local dance floor shortly but I will look at the network54 sites you gave me as soon as I get home.
Again, thanks,
-Joe B.
Joe B.,
While there were several different brands and weights of airsoft bbs, and I did not keep many notes when I weighed and chronied them, here are some of my observations and notes…
The weight of the hollow plastic bbs is greater than one is lead to believe by what is written about them and what is on the cover of the bb containers.
First of all, they are not hollow, they are solid. Secondly, the weight of .12, .2, etc. does not refer to grains, but to grams. I am sure that this was done to give the impression of lightness and safety.
So, rather than designating them .12, .2, and .25, it may be more descriptive for reader accustomed to real airguns to think of the plastic bbs as… 1.7 grain; 3.1 grain; and 3.7 grain.
For reference, a metal bb weighs 5.2 grains, and of course you all know how much your pellets weigh, including the ultra light .177 pellets (e.g., Crossman Silver Eagle h.p. = 4.8 grains).
So, in actual fact [Correction to Part 3, above, which apparently nobody including BB read and caught and corrected), these plastic bbs weigh on the order of 1/2 of a steel bb and 1/3 of a light pellet. Little wonder that they hurt worse than a bee sting for about 5 seconds when hit from 20 feet while wearing one laye of clothing.
I wonder if any of the readers have been shot by a steel bb or by a pellet gun, and what their experience was. I suspect that it does not hurt much worse than airsoft (viz., a wasp sting), but probably lasts a lot longer than 5 seconds!
One of the patterns I noted regarding airsoft bb weight was that the .12 g bbs actualy usually weighed .11 g. Also, the .25 g bbs tended to weigh .24 g. The .2 g bbs tended to weigh .2g
Anyways, at 5 feet the R72 very reliably shoots 3.1 grain bbs at 230 fps. Very reliably means little, but when I say 230 +/- 3 fps more than 85% of the time, then you must be impressed. This yields .36 ft./lbs. energy.
The non blowback CO2 pistol at 5 feet shot the same weight projectiles at 305 fps for much of the CO2 cartridge life, yielding .64 ft./lbs.
I am surprised that so little energy can produce so much pain. I cannot remember what weight bb hit me, but I am interested in experimenting (this time starting with 3 layers of clothing and working down) with the .30 aluminum airsoft bbs (sounds oxymoronic, or perhaps just moronic) that BB wrote about in his airsoft blog in 2005.
– Dr. G.
BB,
Uh oh! My Benjamin pump has acted the same way as Chris’s from the first (the handle stays up after bleeding). I haven’t done anything to it and it has always pumped fine. Should I keep using it or do I need to call Crosman (I bought it from Pyramyd August of 2008)?
Thanks,
.22 multi-shot
.22 multi-shot,
First try leaving it alone for a day, then trying it again. If that doesn’t fix it, call Crosman. They are the ones who handle the warranty service on the pumps. Pyramyd AIR may just slow you down in this case.
B.B.
DR.G,I’ve never had the displeasure of being hit by a bb or pellet.however;I purchased a box of Beeman felt cleaning pellets[.177]years ago and the enclosed instructions said they were also good for shooing unwanted cats!? now being an animal lover(The domesticated kind)I thought that sounded very inhumane…then,not being the sharpest knife in the drawer,I decided to see for myself how much this would hurt the afformentioned cat.I proceeded to load and shoot one felt pellet at my shoe-clad foot.Holy bleep did that hurt…at only 400fps!maybe they should tell you to make sure there is plenty of distance,now that I know that for sure! thank you for ALL your airgun insight. FrankB
Chris,
I’d send the pump back now while it was still under warranty. Easier for dirt to get into something rather than out.
Wonder if you could get a rebuilt one swapped out. I remember days of replacing alternators where parts store held credit card number. If you didn’t return bad one in a couple of days you got dinged an extra charge. They send you a rebuilt one, and then you send yours back.
Herb
Dr. G….
You need to ask the guy in NJ who shot and killed his wife with an airgun this week if it only stung her a little.
twotalon
Dr. G
Sorry, I forgot to key in my screen name, shadow express dude. My R72 will print 10rounds of .25gram in an inch at 10yards. .30grams will do better with an inch at 15-20yards (usually in vertical strings because of the hop up). Today was nice in Virginia so I went out with some of my guns. I tested the S&W sigma .40, and used the R72. The R72 was great at hitting 12inch targets out to 50 yards. More on the sigma after I put 300 more rounds through it:)))))
P.S. just an interesting tidbit, the R72 is a copy of the Mauri G3A3 socom.
Shadow express dude
OFF TOPIC,
Gran Torino –
Saw the new Clint Eastwood movie last night. Very sweet. Especially to a mid westerner whose old man worked in a steel mill. I can smell the lighter fluid in the Zippo when Clint uses it, and I am familiar with most of the other “props” which were real life for me.
God Bless the rust belt.
Dr. G,
I will try one of the Crosman’s you recommended. As far as the anonymous thing at the top I think it shows up that way for every one without an account?
Bg Farmer only,
Stop reading this if you are not big farmer. I can see you. How do you get your name instead of anonymous at the start of a comment? I figured you understand that I’m challenged and won’t laugh – at least not too hard. I have always been envious of those with fancy posting abilities.
I still like the QB-78 a lot. I counted the shots and I get 32 from a fill. Unlike with a PCP, it peters out quickly when low. The claim in the factory handbook is 60 shots, but I’m sure that is the price I pay for the extra power. Ordered some more pellets to try in it, I believe the silver bears were claimed to hit 800 fps.
Volvo
Volvo,
No problem. When you post, select the Name/URL “radio button”, then type in “Volvo” (no quotes) in the Name box, leaving the URL box untouched.
RE: Gran Torino. You’re the second person I know that’s given it a rave review — he’s also from Ohio, although probably nowhere near you (or many other people, as far as I can tell:)).
I’m looking forward to the QB78 blog. Maybe the flying dragon will stop by (he’s posted a few times) and tell us the breakdown on shots vs. power. By the way, Meisterkugelns (heavy/rifle 8.4?) and Superdomes seem to work well in Industry barrels, if you haven’t tried them yet.
Hey. BG_Farmer–it works!
“I wonder if any of the readers have been shot by a steel bb or by a pellet gun, and what their experience was.”
Dr. G.,
I have a friend, now 36, who as a 12 yr old shot herself in the hand with a BB from a Crosman 357 pistol (it was the older model that fired steel BBs), thinking it was unloaded. She didn’t tell her parents for fear they and the neighbors would forbid their kids from using BB guns anymore. She had that BB in her palm until last year (you could see and feel it; it was inert all that time), when she finally had it removed (it began to move around and hurt, that last year). She’s a massage therapist, so she insisted that a nerve specialist remove it, fearing a non nerve specialist might accidentally cut a nerve and make her unable to earn a living (the BB had lodged underneath the nerves in the middle of her hand). She flew from Maui to Oahu to do this. It was a nightmare, where no one seemed to know what they were doing. But she did have it removed finally. She brought it home in a small bottle so we could see it. All the copper had worn off and so had some of the steel, it looked like. She’s fine now, still practicing massage therapy.
-Joe B.
When I was young I shot myself in the leg – with blue jeans on – with a Daisy 1179 pistol. Just wanted to see what it felt like.
The 1179 was a joke of a gun, it used a catapult mechanism to flick a BB at about 90fps. And it STILL hurt like the dickens.
Dr. G., Frank B., TwoTalon, and Vince
I imagine how hard a felt cleaning pad, steel or plastic BB or pellet would feel depends on the mv it exits the gun at. That’s the reason I was wondering about which pump airgun the NJ man shot his wife with. When I accidentally shot myself in the inner thigh at point blank range with a green gas PPK/S and a .2 gram plastic BB, it hurt quite a lot, but the pain left within 20 mins and the resulting blood blister wasn’t much larger than the size of the BB itself. PA advertises its Walther PPK/S as 280 fps, which is relatively weak. Had I managed to wedge my 1911A1 gas pistol between my legs, at 360 or so fps, I believe I would have seen blood (mine).
Go to youtube.com and do a search by entering “airsoft”, then look at some of the movies by teenaged boys deliberately shooting themselves and each other with airsoft BBs from powerful AEGs, springers, and sometimes at point blank range (the shooter was drawing a happy face on his friend’s stomach with the airsoft gun). Really interesting reactions from the kids who are shot. These are definitely home-brewed coming of age ceremonies.
I just tried what I described in my prev. post. The people shooting each other doesn’t really start until page 25, after entering ‘airsoft’ in the youtube search window. I suggest you try entering ‘shot by airsoft’ (no ‘ marks). The ‘airsoft’ entry btw will get you tons of interesting stuff too, as will entering ‘airgun’ or ‘shot by airgun’.
Warning, some of this stuff may be a little hard to watch, like the teen shooting his Darth Vader helmet-wearing little brother with a 500+ fps airsoft rifle and laughing at the kid’s pain.
Bg Farmer,
Many thanks on the posting tip. Who knows, I may have met your buddy in Ohio. I have a fairly large circle of acquaintances from all walks of life.
Anyone,
As a kid in the 60’s we played Army with the lesser of our BB guns. Needless to say I don’t endorse it. I can’t recall the model, but I had a Daisy SA replica that had to be the least powerful BB gun I’ve owned. The BB’s went about 15 feet. The point is having shot myself in the hand to see what an airsoft gun was like, it was much worse than that Daisy Peacemaker. So be very careful, I think the term “soft’ is a little misleading.
I believe the guy who killed his wife did it with a G1 Extreme, and he had shot her in the back. The pellet apparently entered her lung.
It sounds unlikely that he did it on purpose. Apparently he was getting ready for some squirrel elimination and he had the gun loaded and cocked in the house. Needless to say, the guy was being careless with it.
I’m half waiting for the calls for mandatory automatic safeties on airguns, but in NJ airguns are legally no different from firearms.
Michael in FL,
Yes, I had seen these before…except for the new 1377 mod with the white stock. Very nice work, all!
“’ve found that Crosman Premiers in the cardboard box are the most accurate in my .22 cal Crosman guns with the 14” barrel”
Are those the domed ones? I couldn’t find wadcutter Premiers in a cardboard box on PA’s site, but then there are a number of items on the site that I know are there that a simple search doesn’t reveal.
Kind regards,
Joe B.