by B.B. Pelletier
This posting was requested by a reader several months ago, and I think it’s timely now with Christmas approaching. People buying PCP guns for the first time are going to make the choice of whether to use a scuba tank or a hand pump to fill their guns, so the maintenance of scuba tanks should be of interest to many. In fact this information applies to all pressure vessels that have to be tested.
Controlled by DOT
Every country has a national agency that controls the use, transportation and maintenance of pressure vessels. Though the laws differ somewhat, they are all pretty similar because the concerns are always the same. In the United States, the Department of Transportation controls pressure vessels. They establish the regulations for their use, one of which is periodic pressure testing to determine if the vessel is still safe to fill. That test is done with water instead of air and is called a hydrostatic test. Water is much safer because it doesn’t compress; so, if there is a rupture, it doesn’t explode like pressurized air does.
Each type of tank has its own test
The hydrostatic test is peculiar to the type of tank being tested. Not all tanks are hydrotested every five years, though that is a normal period of time. There is a type of carbon fiber tank that has to be hydrotested every year! But the carbon fiber tanks airgunners use need a hydro every 5 years.
Let’s look at a common 80 cubic-foot aluminum scuba tank. It needs a hydro every five years. The testing station has a test chamber, usually buried in the floor or behind massive blast walls. The tank’s valve is removed and a test fixture is screwed in its place. For the 80 cubic-foot aluminum tank, the test is to pressurize the tank to 5/3 of its standard operating maximum. Since 3,000 psi is the standard fill pressure, they pressurize it to 5,000 psi. But they use water, not air, so if there’s a failure, the explosion is relatively minor.
What are they looking for?
They’re not trying to blow up the tank. Instead, they measure the volumetric displacement of the tank when empty and again when pressurized to 5,000 psi to determine if the tank walls still have the required flexibility. After many pressurization/depressurization cycles, the tank walls become work-hardened and are no longer safe. That tank will fail, and failure means it can no longer be filled. No dive shop will fill a failed tank.
How do pressure vessels fail?
I talked to the test engineer at a test station, and he told me a failure during test was rare. I don’t mean a tank that fails to pass the test, I mean one that actually ruptures during testing. The most common failure point are the valve screw threads. They strip out under pressure, and the test rig is blown out. The second most common failure point is the base of the tank. When the tank is stored standing up, water (from condensation inside the tank) runs down to the base and promotes corrosion. Aluminum doesn’t exactly rust in the conventional sense, but it will corrode under the right conditions. These failures are rare, but not unknown. However, a tank that bursts on the side is almost unheard of, though I’m sure it does happen with all the tank testing that occurs.
Tank markings
The top portion of a tank is covered with markings stamped into the metal. Among them are the type of tank, the manufacturer, the max working pressure, the serial number and the dates of all the hydrostatic tests.
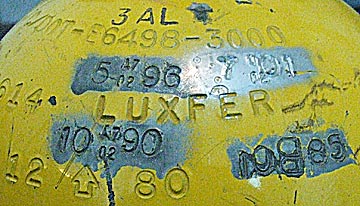
Lots of information on this old tank. It was made and first tested in December 1980. You can read the other dates clearly. This is an aluminum 3000 psi tank, which you can also read, along with the manufacturer.
I hope this posting answers all the questions about hydrostatic testing. If not, you know where the find me!
B.B.,
This is off topic, but I am new to airgunning. Are there any legitimate concerns regarding handling lead pellets on a regular basis?
Just curious…
Thanks,
JRuger
JRuger,
Handling lead pellets can be completely safe if you are careful about what you do. I shoot 25K pellets a year and have been doing so for 15 years and I have low blood lead levels. I also cast lead bullets, which is supposed to be dangerous as well, but isn’t if you do the right things.
The right things include proper ventilation and washing your hands after handling lead. Also taking Vitamin C daily to reduce heavy metals in your tissues.
I should do a blog about this, I suppose.
B.B.
BB,
Some sources claim that lead only lingers for a few hours in your blood so a blood test wouldn’t necessarily rule out mild lead poisoning.
Well, I’m no expert when it comes to lead in the body, but my blood level was tested by an insurance agency to determine if I had any long-term risks from lead poisoning. That was done because I told them I cast lead bullets and I shot many lead pellets each year. Their determination was that at the age of 55, my blood lead level, which they felt was indicative, was below what was expected of a 30 year-old man who never came in contact with lead.
I have used vitamin C is mega doses for the past 20 years. Since C is a recommended suppliment for the removal of heavy metals from the body, I assumed it had something to do with my test results.
B.B.
B.B. How often does the Carbon Fiber (88 cu ft) that Pyramyd sells need to be tested. Is it once a year?
Don,
Pyramyd’s CF tanbks get hydroed once every five years. The CF tank that need a hydro every year is very exotic and hard to find.
B.B.
BB,
You said vitaman C helps remove heavy metals from the body. Have you ever heard of milk? That’s what I heard. Did I hear right?
it hadnt crossed my mind at the time, but is propane safe to use indoors? my research tells me it is heavier than air and will pool on the ground. i’ve also read propane is nontoxic; but humans dont run on air (or helium! =)). also, while i trust propane is very safe, wouldnt shooting sufficient amounts cause perhaps an inch worth of propane? at that quantity, i dont think it would be unreasonable to think that something flammable dropped into the cloud would combust it. what are your thoughts?
Speaking of hydrostatic testing, what about the air tubes of PCP rifles? I’ve often wondered about this, and have never found a knowledgeable answer. Will a PCP rifle become dangerous to charge over time? And how would you know? Are they supposed to be tested periodically (and does anyone actually do this)?
baldtrucker,
I have heard nothing about milk. There is a suppliment caller “Metal Magnet” that does even better than vitamin C.
B.B.
dm29,
I used to heat my water and run both my stove and clothes dryer on propane. The tank was in the basement and so was the water heater with its pilot light.
Yes, sometimes accidents do happen, but hundreds of thousands of homes are using propane this way.
B.B.
Hydro airguns,
The DOT requirement is to hydro all vessels over 2 inches in outside diameter, so most rifles do not qualify. Only the AirForce air rifles have a hydro test. They also have a safety burst disk.
All 10 meter guns with removable reservoirs have dates after which the tanks should not be used. This is in the owner’s manual. They do not get hydroed.
B.B.
This comment has been removed by a blog administrator.
Thank you B.B.!
The original post didn’t answer all my questions, but your last comment about the DOT requirement for vessels over 2 inches pretty much answered the rest. Is the requirement based just on diameter or is there a length limit (e.g. what about a 2 inch tank 2 feet long)?
I do have one concern. Since you mentioned that the threads are the most common place for a hydro blowout, it seems like this could be a problem with 2 inch or less tanks (they generally have the same threads as larger tanks [5/8-18]). It seems like this might happen unless the threads will always hold at 3000PSI but not at 5000PSI.
Thanks,
.22 multi-shot
dbarr,
Length doesn’t matter, only diameter. I’m not that familiar with removable air tanks. The ones I do know have finer threads than you mentioned.
I’m sure the threads have to meet good engineering practices for the pressure they have to restrain.
B.B.
B.B.,
The 5/8″-18 threads are standard tank threads for a paintball tank regulator to screw into. They also seem to be standard for other small pressure vessels.
I don’t know anything about standard threads for airgun tanks.
Thanks,
.22 multi-shot
if I read your comment about PCP rifle cylinders correctly, they are exempt from testing but should not be used past the expiration date.
If I have my PCP cylinders tested and date stamped, will I be able to refill them from another persons system? Such as if I was at a match and needed a cylinder filled.
Thanks for the article, it is timely and informative.
Felton,
Yes, YOU can fill anything YOU want from any source. But getting someone ELSE to fill it might be a problem.
The reservoir won’t be, because dive shops aren’t involved in that process, but the bulk tank that is used to fill the reservoir can’t be refilled by a dive shop if it doesn’t conform to the law — which means being properly tested.
B.B.