by B.B. Pelletier
Guest blogger
Vince Brandolini stirred up some interest in a previous blog when he talked about the energy he derived from certain spring guns. Many of us wondered how he calculated spring energy. Today, he shows us how!
If you would like to write a post for this blog, please email me at blogger@pyramydair.com.
Bloggers must be proficient in the simple html that Blogger software uses, know how to take clear photos and size them for the internet (if their post requires them) and they must use proper English. We will edit each submission, but we won’t work on any submission that contains gross misspellings and/or grammatical errors.
Springtime! – Part 1
by Vince Brandolini
When I mentioned a little while ago that I’d been calculating the potential energy stored in the powerplant of a cocked spring gun, there seemed to be some interest in how this information is derived. While there are plenty of shooters who don’t want to concern themselves with the mechanical nitty-gritty of their guns, others might be interested to know a little more about the heart of their weapon’s powerplant.
The function of an airgun spring is simple enough: it stores human-provided energy that is slowly put into it. At the shooter’s command, it releases it quickly. This is something a spring gun shares with the a slingshot or bow. The power that the gun imparts to the pellet is largely (although not completely) dependent on the capacity of the spring to hold energy.
Energy is another word for work, and we commonly express it in simple terms of force x distance. If you lift a 3-lb. weight two feet off the floor, you’ve just done 6 foot-pounds (ft-lbs) of work. When you cock a spring-piston gun, you’re putting a very fixed amount of work (or energy) into the rifle’s powerplant.
If the powerplant were perfect (a physical impossibility), that same amount of energy would be transmitted to the pellet. Unfortunately, most of the energy you put into the rifle ends up going to waste. How much is wasted depends on the gun’s efficiency. The higher the efficiency the more powerful a gun will be for a given cocking effort, or it will need less cocking effort for a given amount of power. Either way, high efficiency is obviously better. Knowing the efficiency of a given springer can be very useful information. In a way, it’s just like checking the gas mileage of your car. On one hand, it gives you an idea of how well the gun is designed; yet, on the other hand, it could alert you that the gun needs some sort of mechanical repair.
First, you have to calculate the energy stored in the powerplant. You’ll need to know four things about the gun and its spring:
- The amount of preload when the spring is installed in the rifle
- The stroke of the piston
- The free (uncompressed) length of the spring
- The spring rate
The spring rate is usually expressed (in the US) in pounds per inch, and describes the amount of additional force required for every additional inch that a spring is compressed. For example, a spring that’s 30 lbs./in. (which, incidentally, is a ballpark figure for many guns) is normally 10″ long and requires 30 lbs. of force to compress it to a length of 9″. Compressing it further to 8″ requires 60 lbs., 7″ requires 90 lbs. and so on. The best way to determine spring rate is with a spring tester, which is a calibrated scale combined with a mechanism for holding the spring while it’s compressed to a certain length. A spring tester is a specialized (and expensive) piece of equipment. We can get around that by making some careful measurements.
To calculate spring rate, we need to know the following:
- Number of coils
- Outside (or inside) diameter
- The actual spring wire diameter
- The modulus of elasticity for the material in question
The modulus of elasticity doesn’t really vary that much from one spring steel alloy to another, so we can use a good compromise figure. It’s very important to measure the spring AFTER it’s been fired several times. New springs almost always take a set after they’re used a few times; that is, they shorten up. Measure a new spring for an RWS 48 and you’ll find something around 11.5″. Install it, shoot it for a while, yank it out and measure it again. You’ll find that the length is now closer to 11″. Shoot it for 1000 more rounds, and you should find that it doesn’t get much (if any) shorter than that. The vast majority of spring set happens within the first few shots
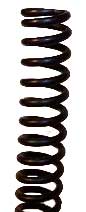
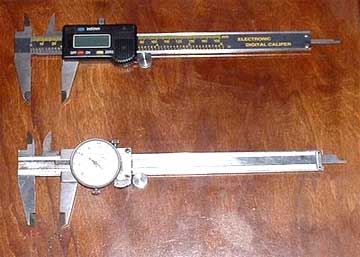
For the other measurements, a dial caliper is required. Thanks to the Chinese, they can be had for very reasonable prices. The electronic one has become very common over the last few years, thanks in no small part to Harbor Freight, where they’re frequently put on sale for about $16. At that, they’re a terrific bargain. It’s not unusual to see other outfits selling the same caliper in the $30-40 range. However, and I learned this the hard way, they’re not perfect! They can drift. I had one that inexplicably lost about .005″ on the low end of the scale. That’s why I almost have a preference for the old-fashioned version, which, oddly enough, actually costs a bit more.
The OD of the spring has to be measured, and since the springs are usually not perfectly round, it’s a good idea to measure in several places to get an average. The wire diameter is measured with the dial caliper
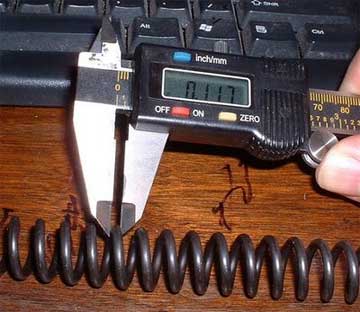
When you measure the wire, MAKE SURE the caliper is NOT held parallel to the spring. It MUST be perpendicular to the wire itself! If it isn’t, your wire diameter measurement will be too great. Since wire diameter is extremely critical to calculating an accurate spring rate, this would throw everything off. When measuring, it’s best to slowly wiggle the caliper back and forth while maintaining pressure on the caliper jaw. Watch the readout while you do this and record the lowest reading. That’s your wire diameter.
The spring rate is calculated as follows:
- OD=outside diameter
- WD=wire diameter
- NC=number of coils
All things being equal, a fatter spring is actually softer than a thin one, and one with many coils is softer than one with fewer coils. Notice how the spring rate goes up proportional to the wire diameter to the fourth power! As I said, this measurement is critical! A 10% error here will result in the calculated spring rate being off by 35% to 45%.
Once the spring rate has been calculated, the gun has to be partially disassembled. The rear spring retainer or anchor has to be removed, and two measurements have to be taken. The first is the free length of the spring. This is simply the length of the spring when it is out of the gun and with no pressure on it. A tape measure is adequate. Get it to the nearest 1/16″.
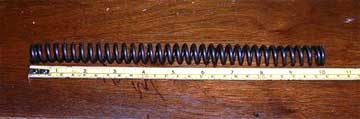
Next, measure the preload (in inches). This is the amount that a spring is compressed when installed in an uncocked rifle. The easiest way is to start reinstalling the spring. Put the rear spring retainer in place, and measure the distance that the spring has to be compressed in order to reassemble the gun. Once the preload is known, the gun can be reassembled.
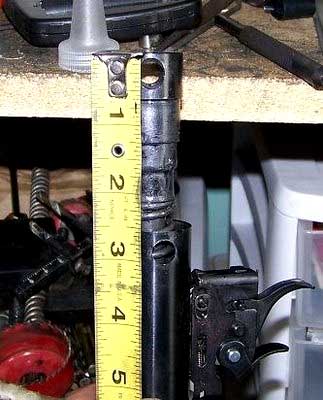
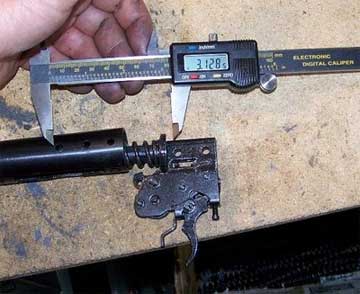
There’s one last step, and you’ll read about that next Monday!
B.B.,
As you are writing about springers, I have a question about whether the power of my .177 RWS 54 is what the factory intended. I have shot fewer than 5,000 shots, yet noticed over the last few weeks that the squirrels arn’t falling as fast as they used to. At 10 yards, domed 10.3 grain pellets are flying at 775 (+/- 25) feet per second (14 foot pounds), while 7.9 grain pellets scream along at 930 fps (15 ft.lbs.).
I understand that the 54 may have the same action as some of RWS other models (48, 52?), and so I tried to find the expected velocity figures on the web in a number of ways, but remain unsure of what the .177 model 54 should shoot. I reread your blog article on the 54 from a couple years ago, but of course that was a .22 which you wrote about. Thanx.
– Dr. G.
hi what titan spring would i need to replace a 34 coil 22 spring
whatmyspring,
Welcome to the blog.
Not a clue which spring you need. Measure the spring and select it yourself. Here’s how:
/blog/2008/10/hw-55-tyrolean-part-5-how-to-measure-a-spring/
/blog/2012/02/the-spring-piston-powerplant/
The spring you need must be no longer than the one you intend replacing, iof you want to keep it simple. If you want the absolute longest spring that will fit, put the piston into the cocked position (outside the gun) and measure the distance from the inside top of the piston to the place where the top of the spring guide is.
B.B.
Dr. G.,
A .177 54 should be in the 17-19 foot-pound region, depending on the pellet. I would expect 7.9s to go 1000 f.p.s., at least.
B.B.
BB,
I have an issue with my Blue Streak. It was new in January, and this past weekend it developed a problem. At pump number seven the gun would ‘sigh’ (it sounded like air was coming out of the muzzle) and the pump wouldn’t offer the usual resistance. An additional pump would behave as normal (that is, it was hard to pump and no sighing).
I thought this was my que to oil the gun. I put some Pellgun oil on the piston groove (Um, is that the correct place for oil on this gun?). But that didn’t seem to correct the problem.
Accuracy is apparently unaffected (I was dinging bottles and cans at 40 yards w/ the Williams peep sight. Whoo Hoo!!!).
What do I do? So far this is my go-to gun, and can’t see living without it.
Thanks!
Nate in Cincy
B.B.,
Are your numbers taken at the muzzle? If so, what would they be at 10 yards (where I measured mine)? Does 1000 fps with that light pellet drop to 930 or 950 at 10 yards? Thanx. – Dr. G.
B.B.
Where can I buy springs for my Air rifle? I have an old rifle and the manufacture said they stop making replacement spring for it and they don’t have any more in stock.
Should I take my spring out and measure it, then use this information to order a steel spring from “McMaster Carr”?
Please help,
Joe
Cowboy dad here with an funny OT item.
In the news today (Yahoo…sorry I can’t get the link to cut an paste) is a story from England.
Seems a fellow had what he thought was an old brass cup his grandfather had given him 50 years ago…turns out to be a 2300 year old gold vessel of Persian origin now valued at $1000000.
Funny part….as kid he used it for target practice with his air gun.
Expensive target practice!
Nate in Cincy,
This would be a great time to own a chronograph. I can’t diagnose your gun from the clue you gave, but are you storing it with a pump of air in the chamber all the time? Because it sounds like you’ve been storing the gun empty.
My recommendation is to keep on shooting the rifle until it develops more obvious signs of a problem. Keep it well-oiled (three to five drops on the pump piston head every month for the next three months), and store it with two pumps of air in the compression chamber.
See if that doesn’t cure the problem.
B.B.
Dr. G.,
Nobody chronographs an airgun at anything but the muzzle unless there is a compelling reason, such as determining the ballistic coefficient. So the answer is yes, my numbers are always from the muzzle, unless I say otherwise.
The only reason firearm shooters do it farther away is to allow the muzzle blast to dissipate.
I can’t say what the velocity drops to at any distance without testing the specific pellet in question. I don’t trust the tables and ballistic programs.
B.B.
Vince,
Excellent write-up. It’s good to see the math behind the data. I did not realize that the wire diameter was taken to the 4th power, and now I see why the range of wire diameters in most airgun springs all fall within a narrow range. It only takes a couple of thousandths difference in dia to make a big difference in force.
Here is a site I often use for theoretical spring rates and force at various compression lengths. I find it pretty handy.
http://www.msdspring.com/springcalculator/compression/Input_round_cyl.asp
Looking forward to the next installment.
pestbgone
Joe,
McMaster-Carr isn’t likely to have the kind of springs you need. But this gentle,man imports more different kinds of airgun mainsprings than anyone in the U.S.”
He knows what springs go in which guns, so you often only have to tell him the maodel you have.
Pyramyd AIR also has quite a few Diana mainsprings.
B.B.
Here’s the link to the Persian gold cup:
http://news.yahoo.com/s/afp/20080528/wl_uk_afp/lifestylebritainauctionhistory
B.B.
BB,
I’ve been storing it with one pump in the gun. I’ll increase it to two.
Thanks!
Nate in Cincy
Nate,
No need to increase the pumps if you’ve been doing it. I was thinking dried out seals.
You possibly have a small dirt particle embedded in one of the seals. Over-lube your gun and shoot it a lot. That may blow it out.
I’d say give it a couple of months and if the problem persists, have it rebuilt.
B.B.
I see Beeman have begun to import the European spec HW80,50 & 30S guns. I was told they are only going to be sold by Pyramydair and a couple of other dealers. I haven’t seen any announcement on this site.
Also presuing the Webley website I see what appears to be a “new and improved” Patriot. I’ve emailed Webley about this but have not received a reply yet. I was wondering if you have any advance info on these matters?
Vulcanator,
I’m not aware of Beeman importing any HW80s or 50s. They have been selling the HW 30 for more than 30 years. Where are you seeing this?
The new Patriot is a Hatsan design that Pyramyd AIR found unacceptable. Too many quality faults. So they returned the guns to the distributor.
B.B.
B.B.,
I checked the muzzle velocity, and it turned out to be 1010 +/- 15 fps using the 7.9 grain. So, it sounds about where you said it should be, or maybe 5% low. I think that you would be very surprised to hear how long this rifle was left in the cocked position, and still apparently be within 5% of its factory specs. This is a test of your expertise: take a guess how long: A.) 6 days, B.) 6 weeks C.) 4 months D.) 2 days. I rechecked at 10 yards and that little bb-weighted (er, lead bb that is) pellet slowed all the way down to 915 +/-15 fps. Looking forward to your reply, and thank you again for your help. – Dr. G.
Excellent post, it will come in very handy over the years I suspect!
Nick
Vince,
Good job; I can’t wait for the sequel. I wonder if there’s a “sweet spot” for efficiency. It seems to me that too high would imply an un-maintainable perfection of components, tolerances, and operating conditions. Something like the way a race car engine puts out much more power than a regular car engine from the same displacemt.
Posted by B.B. Pelletier,
This question was sent to “I want to be a guest blogger”. We don’t take questions there.
I have a few questions I would like advice on. I hike in the mountains of Colorado which are full of mountain lions and black bears. I do not want to own a standard pistol but thought that if ever confronted by an animal like these a high powered pellet pistol might offer some protection (albeit, I admit not a lot).
What pistol would be the best (e.g., highest powered)? What type of pellet should be used (e.g. pointed, caliber or, grain – however it is measured)?
Any other suggestions?
J.
J,
I recommend you carry a .44 Magnum with a 4-inch barrel. Pellet guns are to wild animals as water is to hornets – not a good idea.
Nobody “scares” an animal away. You either leave it alone – something I highly recommend – or you kill it. There is nothing in-between.
B.B.
Dr, G.,
I would guess it was cocked 6 days. Four months would be too long and 2 days too short.
Just a guess.
By the way, earlier you said it was going 930 f.p.s. Was that the downrange thing?
B.B.
J,
I’ve heard some guides recommend carrying a defensive spray to spray in the eyes of wild animals up to Kodiak size…frankly I’d rather trust a heavy handgun. As for using a pellet gun for bears and mtn lion, I’m reminded of the old saying, “Son, if you shoot the animal with that, and he notices it, you are in big trouble.”
–Joe B.
If memory serves me correctly, Beeman use to offer a tool to size pellets. Any idea who made it, what it was called, and if they are still available?
The Beeman pellet sizer was made for them by some small shop – perhaps European. No other name is marked on the tool. It came with interchangeable dies for different sizes and calibers.
They are no longer available because pellet sizing has gone out of vogue. Shooters learned that the barrel automatically sizes the pellet.
B.B.
Thanks for the information. I have an airgun with a tight breech, and thought maybe I could “skinny up” some quality pellets. The only pellets that fit it perfectly are Milbro Rhinos, which are a utility pellet at best. Webley mosquitoes are not bad, but are going to be discontinued.
After getting my new Beeman catalouge picturing the HW80 I called Beeman. They told me that they are only going to be sold by Pyramydair and a couple of other dealers.
As far as the Patriot is concerned I’m aware of its issues, it appeared that Hatsan just dressed up one of its existing models with a Patriot looking stock and passed it off as Webley!
If you look at the Webley website the Patriot pictured looks like its UK made predecessor-a sign of promise indeed?
Vince, nice job. I’m guessing that a lot of the factors you mention are what’s lumped together in what is called the “spring constant” in physics books that measures the spring’s stiffness. Perhaps this is for the next installment, but I’m curious to see where efficiency enters into this. It’s not the same thing as stored energy is it? It seems to refer to how the energy is transferred.
As to the question of how to deal with dangerous wild animals, I would say, having no experience at all on the subject, that no pellet gun would do for the kinds of animals mentioned. As long as you are going for firepower, you might consider a slug gun although it would be less handy than a .44 magnum handgun. I’ve heard about defensive sprays too, and I must say that the theory is appealing. It makes sense to me to attack the animals’ weakness in the form of its mucous membranes of eyes and nose rather than bone and muscle that is supercharged with adrenaline. Only a fantastic shot could hit the eyes and nose with a gun but with pepper spray you could hardly miss. Some of my experiments with pepper spray for humans indicate that it hurts like hell even when it doesn’t go into the eyes, and there are plenty of anecdotes of a comparable effect on animals. Some have reported stopping a charging grizzly in its tracks. I’ve also heard testimony from guides who say that the mere carrying of guns (compared to pepper spray) seems to make animals behave more belligerently as if they can sense a more aggressive attitude from carrier although that would be hard to verify.
Maybe a bear spray would be good as a back-up for a hiking partner which would be a good idea anyway in tough country with bears and mountain lions. As you pull your firearm, the partner could hose the animal down with the spray.
Matt61
B.B.,
It turns out that it was cocked for 6 weeks, perhaps a little longer. So that just goes to show! The fps that I documented were intially based on sets of 3 pellets, whereas the second time I made sets of 6 pellets, as there was quite a range of about 5% (30fps). – Dr. G.
Vulcanator,
Okay, now I’m with you on the HWs. I didn’t know that.
As for the picture Webley has on their site, I hope, like you, that it is a promise of a return to the Webley quality standard, and not just a lazy IT person at Webley forgetting to update the website.
B.B.
Dr. G,
Well, six weeks surpasses the one month test I did on four different mainsprings for the R1 book. Those Diana springs are really something!
B.B.
Glad to hear Beeman will be importing the HW50S and HW30S. The HW30 they currently import does not have the Rekord trigger as the “S” denotes. This will make it as close to an R-7 as you can get, without the added cost. The HW80 seems to be available on a pretty regular basis already.
Matt61, efficiency has nothing to do with how much energy is stored in that spring any more than gas mileage has to do with the size of the tank.
Efficiency is merely the percentage of that energy that ends up going into the pellet by the time it leaves the barrel.
J
If your first priority is really “how do I best stay alive if I encounter a dangerous animal”, I think the real world answer sort of takes care of itself. A .44 mag or larger is really considered the minimum. A 12 gauge with slugs is better yet.
D
BB and Mr Vince,
I really love this kind of technical blog on airguns not so much because of my academic training but simply because I am a natural born tinkerer. It is very educational and helps me understand airguns better.
Spring energy calculation helps us understand the science of the otherwise secret knowhow of tuning gurus.
I hope to see soon a discussion on determination of volume(v) and pressure(psi) of air needed to propel a particular pellet weight(grains) through a certain barrel length(inches) some specific muzzle velocity. Including caliber, that is a formula with at least five parameters. This applies mainly to pcp and co2 guns though.
These kind of formulas and numbers in a way provide technical map in tuning/tinkering activity rather than a trial and error process.
I am looking forward to your next post. Thanks a lot.
Dave
any body, is the benji discovery n the same class as rifles like the evanix and sumatra, career? you catch my drift. how much more powerful is it than the 392? what’s the largest animal you could shoot with it in the head at 25 yards? coyotes, fox, bobcat maybe. would it hhave the power to do this?
Hello all! Good to be back.
Matt61,
Regarding this sharpening monstrosity…
you should get a set of Norton stones. Thats what i use for most of my sharpening. They do not get give you the finest edge but are very forgiving (look at shaptons if you want the finest edge)! I would recommend the dual grit stones, they are thin but you wont wear em out!
All i said is “not the finest edge” as in – yes, sharper is posable – but were still talking tree toping sharp (not shave against skin, ABOVE)!
98$ for all four grits + base. You do need the flattener. Totals like 120… Heres a link.
http://www.craftsmanstudio.com/html_p/N!LWS.htm
-Henry
MONTANA DEPARTMENT OF FISH AND GAME ADVISORY ON BEARS
Helena Montana, January 31, 1999 – In light of the rising frequency of human/grizzly bear conflicts, the Montana Department of Fish and Game is advising hikers, hunters, and fishermen to take extra precautions and keep alert for bears while in the field. “We advise that outdoorsmen should wear noisy little bells on their clothing so as not to startle bears that aren’t expecting them,” a spokesman said. “We also advise outdoorsmen to carry pepper spray with them in case of an encounter with a bear”.
It is also a good idea to watch out for fresh signs of bear activity. Outdoorsmen should recognize the difference between black bear and grizzly bear paw prints and scat.
A grizzly’s paw is larger and its claws are longer than that of a black bear. Black bear scat contains lots of berries and squirrel fur. Grizzly bear scat has little bells in it and smells like pepper.
B.B.,
The Daisy 499 arrived today. Included in addition to the gun with std sights: a Daisy 5899 receiver sight, black fabric sling with an Uncle Mikes quick detachable swivel, swivel stud, an envelope with 5 insert for the front sight, and the normal variety of literature.
While all this is appreciated, I could not help but recall what you said in your blog about the concerns Daisy had over the price point. My thoughts would be that other than two or three front sight inserts, the rest could be options or part of a deluxe package. This could put the gun under the $100 mark, and make it affordable for more families.
The difference between this and the Red Ryder is night and day. Sure, you could replace more of the plastic with metal, but then it only gets further out of reach.
I was able to get one-hole groups at 5 meters, albeit ragged – but 10times what the Red Ryder was capable of. The velocity was actually above the stated 260fps and averaged 317fps for a still safe 1.21 ft lbs.
But none of this really matters, because then the real tester came downstairs asking if I had bought another gun for myself. I told her no, this was for her. An early birthday present. I held my breath as she tried to cock it. No problem. “this one is easy for me” Then I explained the peep sight. (I put a small drop of orange paint on the tip of the post insert earlier) Shooting off hand, she hit the target on the first try. No, not in the ten ring. But it still gave her a huge smile (and me), and then she ran off to tell her Mom about how great her new gun was…..
Thanks,
Dad
Dad, well-done.
Matt61
henry, thanks, do these go along with the super-fine sandpaper and strop with green compound or replace some or all? Were you off hunting in Africa or doing something exotic?
Matt61
vince, thanks, I thought so. So, do you get the efficiency by taking the difference between the stored energy of the spring and the muzzle energy of the pellet? One then wonders at the likeliest cause of inefficiency–especially those that can be corrected. I like very much the notion I got from Clint Fowler, M1 Garand gunsmith, who writes that he tries to ensure that the parts of a gun do not have independent angular accelerations which could cause the barrel to deviate upon firing. I’m reminded about the story of the first British battleship (in a book called Dreadnought by Albert K. Massie). Apparently, a test was run between the previous top capital ship of the Royal Navy and the new dreadnought design which featured an electronic firing control to synchronize all of its guns. The old ship popped away at a target with all of its guns and didn’t hit anything. Then someone depressed the firing button of the dreadnought and blew the target away within a few salvos.
Matt61
Dad,
That’s the kind of result I was hoping for! You just made my day.
May your daughter and you have many years of shooting enjoyment with that airgun.
B.B.
Matt61,
It replaces the paper (with a catch). After the 8k stone the the strop will further improve the edge. Heres the catch – a convex edge is easier to sharpen by using abrasive paper on a computer mouse pad.
Bobcat,
When was the last coyote you dropped with an air rifle?
The Benjamin Discovery is a 20 foot-pound rifle. The AR6 is a 50 foot-pound rifle. No, they are not in the same class. You will get more accurate shots from the Discovery per fill and greater power from the Sumatra/AR6.
You can shoot a blue whale in the head at 25 yards, if the opportunity avails itself. What you should have asked is what game is the Discovery suited for?
The answer would be squirrels, rabbits, nutria and up to turkeys, if the hunter is a good shot.
The Benjamin 392 is a 12-13 foot-pound rifle. The Discovery is a 20 foot-pound rifle.
Determine the maximum range at which you can place all your shots inside one inch. That’s your maximum range with the Discovery, or any air rifle.
B.B.
Vince,
Very nice article! I love the technical stuff, too.
One question – you stated that the formula for spring rate included the modulus of elasticity for the spring material. The modulus of elasticity for steel is about 29 million psi, yet this does not show up in the formula. 11.5 million is shown, which is only slightly above the modulus for aluminum.
Perhaps the term was modified before being plugged into the formula? What is your understanding?
Thanks in advance,
Mike