by B.B. Pelletier
This is part 2 of the Career Infinity report. Normally, I’d be testing velocity, but something came up. Today I’m going to take you on a short excursion inside a gun, to show you a little about how they work and also how easy they are to repair.
You see, when I tried to fill the test rifle for velocity testing last week, the inlet valve wouldn’t accept air. Then, at around 3,000 psi, the inlet valve suddenly popped open and accepted a fill of about 1,000 psi inside a few seconds. It seemed clear that the inlet valve was sticking.
When I tried to bleed the fill clamp, the air never stopped–a sure sign that the inlet valve was now refusing to close. So, the rifle lost its entire fill. I then sat looking at the gun for many minutes, trying to decide what to do next. That’s not unlike what many of you would do when something similar happens. Normally, I would have boxed up the rifle and shipped it back to Pyramyd AIR, but this time I noticed that the design of the Infinity inlet valve is quite simple and straightforward, as though it was built to be repaired. I partially disassembled it and saw that it was as simple as I had imagined, so I thought this time I would fix it myself and let you see what’s involved.
A call to Boris at Pyramyd AIR got me the parts I needed. They turned out to be a simple o-ring and the inlet valve seal. We’ll do velocity next time (which won’t be long now that the rifle is fixed).
The inlet valve body is aluminum and very straightforward. It screws into the air reservoir tube and two o-rings seal it. Taking it off required one 10″ channel-Lock pliers and a leather belt to keep the jaws from marking the valve body. Everything came apart easily, and I confirmed that the inlet valve seal was the cuplrit.
I’m going to show you the rebuild in pictures.
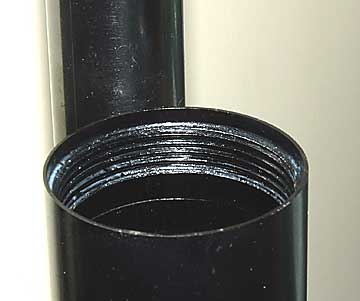
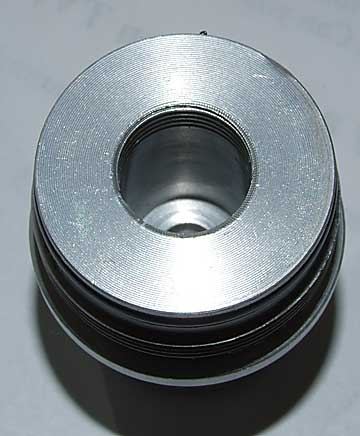
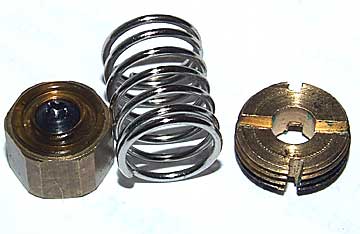
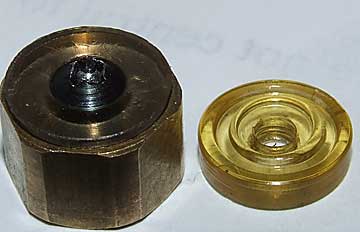
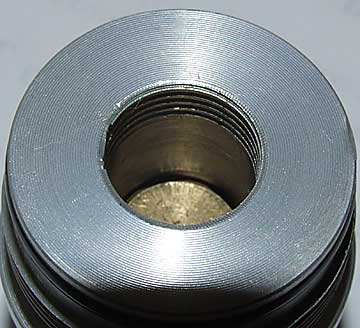
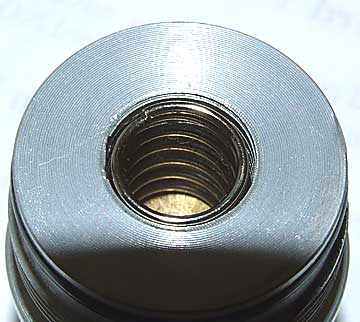
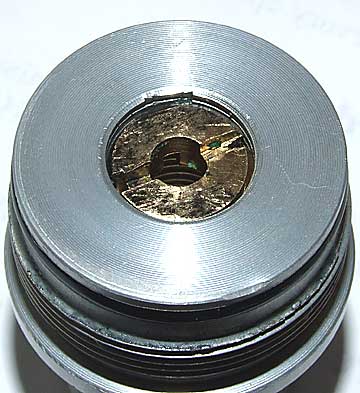
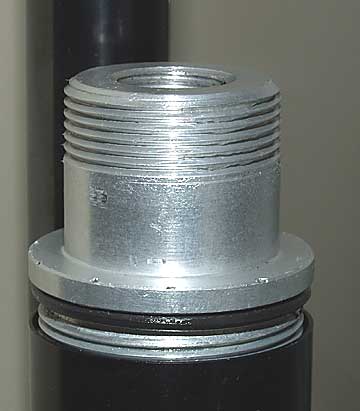
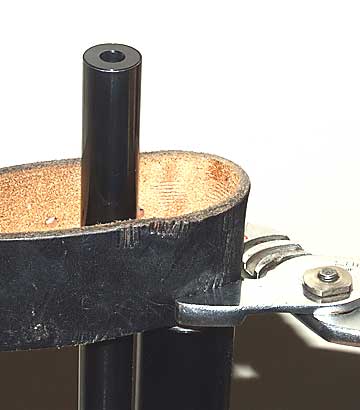
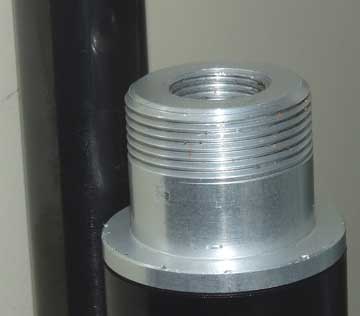
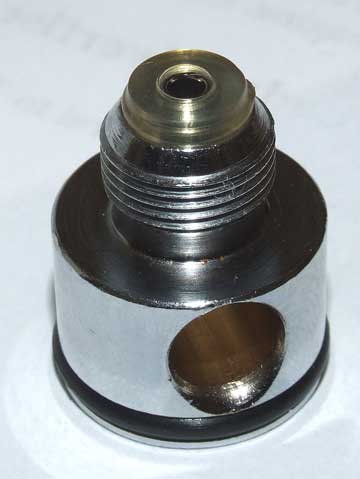
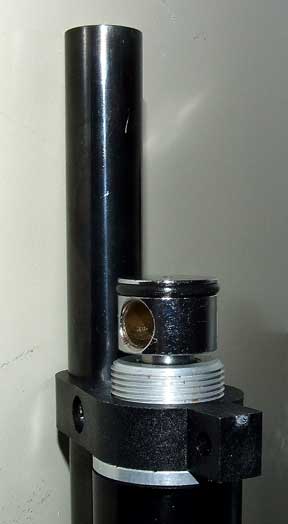
Are we done?
I aired up the rifle to 2000 psi and it held fine, so this job is done. Start to finish was probably an hour, but the reassembly seen here took 30 minutes with the photography. Writing the blog took a lot longer.
Why did I show this to you? Because in all honesty, things like this happen sometimes. I knew this one was simple, and I wanted to show you what that means. The keys here are cleanliness and lubricating with silicone grease.
Since it’s pretty important for PCPs, will PA be adding siicone “diver’s” grease to their catalog?
Morning B.B.: Thanks for showing us this repair, and yes it’s something doable for us also. I went nuts trying to find silicon grease until someone told me that it’s also used by plumbers.
When my Discoveries’s pump died Boris offered to send me the seals to rebuild it, but I chose to have it done under warrenty. Would you please do a blog on pump resealing some time. Thanks much Mr B.
Mr. B.,
I personally dislike repairing pumps, though I did it at AirForce for the returns we got.
I will look into this and do it if I can.
B.B.
ajvenom,
I am working on getting Pyramyd to stock silicone grease and Parker Super O-ring lube.
B.B.
B.B.
Thanks for doing that repair. Examples like that give me confidence to try and fix some little things. When I finally tried to fix the mag advance on my Air Arms S410 .177, I was surprised how easy it was… like 20 min.
“Channel-lock pliers and a leather belt” where do you get such high tech tools? 🙂
I notice the Career Infinity has a “barrel hanger” close to the end of the barrel. Why do some manufactures worry about a “floating barrel” and others do not?
Wayne,
Ashland Air Rifle Range
BB, may I assume that the commonly available silicone dielectric grease would’ve worked as well?
B.B.–Scott298-a little off the mark but I have been reading some of the comments on Pyramyds .177 cal pellets. On my rws 350 mag what are the heaviest pellets I can use without eating up the spring? Are Beeman silver points and Eunjun pellets too heavy to be lauching out of my 350? I have been using cph and baracuda(also Beeman) 10+gr in my rifle -will she take a heavier pellett? Thanks, Scott298–ps the 350 is chambered for .177
Wayne,
A floating barrel is allowed to vibrate the same way every time. A barrel tied to something else with a hanger is not.
Some makers believe that the floating barrel is best for accuracy, while others feel the barrel is too unsupported without a hanger. Those are the reasons and I suppose they are both correct to some degree.
B.B.
Vince,
When I was at AirForce I sealed all the air tanks with a dielectric silicone grease. So I guess the answer is yes.
B.B.
Scott,
I don’t think heavy pellets damage a mainspring, but the majority of airgunners feel that it does. Speaking for them, I wouldn’t shoot a pellet that weighs more than 9 grains in that rifle.
B.B.
B.B.
My USFT has rings around the barrel that don't touch the barrel. I guess they are for protecting it from getting wacked badly out.
The BSA Lonestar is totally free floated, just hanging out there.
But all three of my Air Arms, the .177 and .22 cal S410, and the older s310 all have a barrel band from the air tank, close to the end of the barrel.
In my hands, the Air Arms are all very close to, if not as, accurate as the USFT in a bench rest or from a FT position… and more accurate than the BSA Lonestar, by 20% or so.
So, I'm guessing that other factors are more important to accuracy, than whether or not the barrel is banded to the air tank. And it might depend on how strong the air tank is made, as well..
I moved the barrel band out to the end on the Discos too, and they are just as, or more accurate than before.
Especially with the Discovery, I think other factors are way more important, like valve lock and pellet choice…
What do you think? How much could a tank move and pull the barrel with it?
Wayne,
AARR&R
Wayne,
That’s what I’m talking about. There are no black and white examples of this.
The same argument has gone on in firearm circles for almost a full century and it’s still raging.
The other side of the argument is that of applying some kind of upward pressure on the barrel. I have a custom .30-06 made by Kreighoff that has about 10 lbs. of upward pressure on the barrel.
I think free-floating is one factor in the accuracy equation, but it’s not the only one. Sometimes it gets supplanted by other factors that are even more important because of the design of the gun they are on.
B.B.
B.B., I am perplexed thinking about too heavy a pellet damaging the main spring cause I cann’t see the how or why of that one. My brain is stuck on maybe an increase in the compresson chamber pressure do to the greater inertia of the heavier pellet, but even then the pellet would leave the barrel before the spring would break. Possibley, if you sealed the barrel at the breach, you could cause the seal to fail, but I cann’t see it damaging the spring.
Help! My brain is hurting thinking about that one. Mr B.
B.B.
It sounds like it’s such a small difference in some rifles. My guess is that if the barrel is really strong in it’s fit into the receiver, and body structure, then it can free float. But if not, then it should be locked to the air tank.
The other factor is how the rifle will be used. If it’s got a light duty barrel and it’s mostly for hunting, like a Disco, then it’s likely to get knocked around and should have a barrel band, close to the end of the barrel.
Thanks for your input on this subject.. It’s been a question for me…
Wayne,
Ashland Air Rifle Range
BB: You indicate in your reply to the question about heavier pellets damaging the mainsprings, that they don’t. I happen to agree with you and have gotten into a couple of arguements with other airgunners and tuners over this. The tuners on the forums insist that springs with wire dia of .128 are necessary if you use pellets like CPH’s and Kodiaks in .177 springers. But I’ve never seen a spring with wire that thick in a .177 yet. My HW (R-10 and R-9) Diana’s (46,48,@34) and Crosman’s (five or of the various Quests now) all have springs that are .118 to .121 and some of these guns have had several tins of heavy pellets through them. I just don’t buy the reverse harmonic effect, due to use of heavy pellets, that some suggest that is causing spring failure. If a gun exhibits hesitation at the end of a firing sequence ,then I feel that maybe you have other issues? When I use a heavy pellet it’s because they are the most accurate in a particular gun, especially at longer ranges.I think that this another one of those airgun myths. Perhaps some of these guns just have poor QC or the springs were flawed from the start and people should accept ocassional spring failure as part of the game? I also have noticed that Gamo products often seem to suffer from broken springs, although Diana’s and some HW’s like my R-10 had some batches of brittle springs in the past. Any other thoughts on this particular question about heavy .177 pellets and why so many well known tuners dis-agree with the above opinion? Robert
B.B.
So what was the problem with the old seal? Was it dirty or dried out?
By the way, I just received my Lyman’s 49th edition Reloading Manual. What a treasure of information including the basic stuff. Thanks.
Matt61
BB, I was thinking about the same thing with regards to heavy pellets. For the life of me, I can’t imagine how a heavy pellet would overstress a spring. It seems to me that the only time the spring would even ‘feel’ any difference between a light and heavy pellet would be near the very end of the piston stroke, when the spring is mostly extended and the spring wire is under relatively little stress. I’m wondering if this is one of those unfounded myths that just sorta got repeated because other people were repeating it…
Vince: I think you are right but you will catch hell on some forums if you suggest otherwise. We are only talking about a grain and a half heavier after all. Robert
I’ll vote the contrarian ticket, too. Free-floating the barrel is overrated. Bedding the barrel is better, but a little trickier. The important thing is that whatever pressure or lack thereof is applied to the barrel stay the same.
Heavy pellets: they supposedly accelerate spring failure. Who cares, if they work for the job at hand; the spring will fail at some point anyway.
Volvo,
Thanks for the update on the fx whisper. I’ve been anxiously awaiting your critical analysis. The lack of an adjustment that would allow shots at various fps (like wayne’s infamous s 410) is a turn off. I’d like the ability to adjust low for short range target shooting and then high for long range shooting and even hunting.
RE: psychology vs. physiology spelling. I can only correct single syllable words.
Bob,
I like the sound of your home remedy. “one hot pepper and 20 cups of gin”. One teaspoon a day. Are you kidding?
kevin
Matt,
The old seal had extruded into the valve seat to the extent that it was sticking both closed and then open. That groove in the face of the valve is not supposed to be there.
B.B.
Mr. B.,
The theory about heavy pellets is they don’t move as quickly as light pellets, so the piston rebounds off the high-pressure air it compressed instead of coming to a stop. It causes the mainspring to re-compress somewhat, just as it’s trying to relax. That’s supposed to set up harmful stresses in the wire that cause it to fail prematurely.
B.B.
Bg – farmer,
This part of the FX experience is for you, a quick recap of last evening:
I was just about to call it a night when I glanced over and spotted her again. Nice rack, I said to myself as I walked over. I picked it up at Gander Mountain; it has room for 5 long guns and makes for a welcome addition to the gun safe.
I knew the wife was upstairs in bed waiting, but what’s a few more minutes? There is no mistaking the lines of the Whisper with the other playmates she shares the stand with. Curvy, yet light – very unlike the more rubenesque HW97K next to her or the pencil thin HW30.
A firm grasp and sharp tug puts her in my hands again. Maybe a quick 16? No, I have to admit my muscles are tired from the four fillings earlier in the evening. Not that I couldn’t if I wanted to, but I am in the mood for something different.
I spy my faithful Beeman brass and wood cleaning rod and the wheels start to turn.
I was not the Whisper’s first, not sure I’m even the second, so maybe some additional attention would be in order? How much do I really know about her? I had been so focused on the exterior; I had totally neglected getting to know the inner workings.
The shroud terminates with a threaded muzzle cap. It resists removal at first, but finally gives into my efforts. Once removed, over whelming curiosity makes me peak inside.
In my haste to get started, I leave the simple push attachment on the rod that works so well on the springers. By now I should know that not every technique will work from rifle to rifle.
The first patch passes without issue, the second is not so fortunate. It magically disappears. Frantic, I grab the wire brush attachment and work it feverishly. Nothing.
Time for the regret. I should have called it an evening like I had planned. When will I learn?
It is awkward placing her back in the stand. I know thinks aren’t right, but what else can I do? It is very late now, and I will have to be careful not to wake the wife when I crawl into bed….
Volvo
Correction:
P.A. forgot to ship the CO2 adapter, not the tank…
Jony
here will be a list of features of the new crosman pcp… some facts, but mostly inferences.
-First off,several crosman field target prototype guns have suddenly emerged at competitions. From this, i will infer(WEAK!) that the new crosman pcp will be sold as a field target capable rifle.
-Velocity should not dissapoint us hunters, and because it may be multifunctional, i expect a power adjuster as well.
-Accuracy SHOULD be superb. I expect an all new barrel. We’ve seen what their barrel from a CO2 plinker thats been around for years can do with a PCP, now imagine an all knew one constructed for maximum accuracy! I expect this rifle to rival the accuracy of Airforce rifles and their infamous loather walther barrels.
-Unfortunately for me, most prototypes have had synthetic but adjustable stocks.I think this is the path they will choose with this gun. Also, expect this gun to look more like a rifle than a future weapon (Airforce), and kind of similar to the disco.
-The reciever will be aluminum.
-Prototypes have had both plastic and metal triggers…I predict Metal
-Bolt-action, with a repeater!
-BB says shrouded so, so do i.
That about wraps it up. When it comes out, i plan on revisiting this post and calculating my percent of accuracy (~25%?)
John from Jersey
Jony,
Sorry to hear of your difficulties. I know how frustrating it can be when things don’t meet your expectations.
I’m sure B.B. or someone at PA will work with you to get things back on track.
Goodluck,
Volvo
One more thing so i can say i’m on topic. BB, it looks likecrosman wanted a floating barrel, but couldn’t go all the way. It appears there is now one barel clamp at the end of the stock, and one by the muzzle. This may change because the prototypes i saw were not shrouded (only compensator/weight).
btw verification code was
theshak
john
Jony,
There is something fundamentally wrong and I don’t think it is your scope.
Let’s get off the middle of the power band and go up to number 12 on the adjuster. Shoot at that setting and tell me what happens.
Please leave your scope settings alone or we will never know when you gun starts shooting right.
You spoke about the screws yesterday. Are they fully seated and tight? When you close the bolt do you rotate the handle into the notch on the right side of the receiver?
This sounds like a loose barrel or a bolt that’s no locked in the notch, but work with me and we’ll find out for sure.
What pellet are you using?
When you screwed the tank in was it in all the way?
DO NOT tune the rifle until you get it running right.
Have you called AirForce and asked them about this?
B.B.
Volvo,
Now that’s what I’m talking about! Better than most of what’s on television these days…”Desparate Airgunners”:).
Bg-farmer,
This is when I wish I was you. I spoke with the vendor today and the technician told me I need to remove the shroud and I will find the patch caught in the baffles.
The baffles need to stay in the correct order also. Based on my previous experience, I can almost see the box of parts I’ll be shipping for reassembly.
To bad I don’t still smoke, I could use a cigarette.
Volvo
Jony
Possible problems…single or in combination….
Barrel touching endcap.
Barrel not mounted right….binding or loose setscrews.
Breech end of barrel not lubed.
Pellets not seated well.
Really wrong pellets.
Breech not locked and pulled fully to the rear.
Valve tophat loose.
Power wheel too low….set to 10 or so.
Scope loose or FUBAR.
Check these things.
twotalon
Thank you B.B….
1) Yes, the screws are seated correctly
2) Yes, I turn the notch every time I pull it bach…
3)I am using .22 Crosman Hollowpoints
4) Yes, the barrel is screwed in completely
5) and nope, I haven’t called AirForce….
AND YOU KNOW WHAT I JUST FOUND OUT about two minutes ago!!! the open rear sight won’t fit in the rail!!!!!!!!!!!!!! My God!! Unbelievable… jajaj… The open front sight fits perfectly, but the rear sight won’t even enter the rail… Damn… ABSOLUTELY NOT MY DAY…
Jony
Thanks Twotalon… I will also verify those details one by one…
Jony
Jony
If you are going to shoot crosman pellets, they need to be lubed or they will lead the barrel so fast you won’t know what happened.
twotalon
Volvo,
You forgot the “I never thought it would happen to me…” preface.
ll Bruce,
I’d guess a lot of guys would be surprised by my evening, but just a little more of the same for me… : )
Volvo
Volvo,
You might fix it a little faster if you were me, but the jet-setting and glamour wear thin after a while:). Just take your time. Try to understand how it goes together and take pictures or make drawings before you even attempt disassembly. Then and only then should you take it apart slowly, documenting each step with a note or picture, nothing elaborate, but spending this time will save time in the long run. Also remember, most mechanical assemblies (with a few exceptions) do not require much force to take apart or put together in the correct way:).
I got into big trouble on my clunk trigger (36-2) because it was so simple I didn’t note the trigger spring orientation. Luckily, I found a picture on line; if I had just taken things a little more slowly, I would have saved a day of panic and research.
Bg farmer,
Good advice, I will get my camera and photo it as I go along. My problem is usually in the patience attention category. I would have had a very short career defusing bombs.
Unfortunately, since the rifles are only a couple years old I can not find any detailed instructions. Not even a schematic.
Thanks – Volvo
Bg farmer,
Looks like some other guy is experiencing a similar issue as me.
http://www.network54.com/Forum/79537/message/1228945967/Pics+of+FX+Whisper+Internals
I don’t think I’ll need to take as much a part.
I had thought the shroud was just an empty tube. Who knew?
V
Jony,
That pellet not being seated deep enough was a good tip. That was the way people used to lose all the air in their Condors. If the pellet isn’t seated deep the end of the skirt can fold over and lock the pellet in the breech, causing low velocity or worse – a complete dump of air. That works on most powerful PCPs, by the way. It’s just that not many of them have you seating the pellet with your finger. Most of them use the bolt to seat the pellet.
The rear sight won’t fit the rail? That’s impossible, if we are talking about an AirForce sight. They are fully adjustable. Have you unscrewed BOTH screws? Those sights HAVE to fit.
Is there a burr in the sight dovetail or on the rifle dovetail?
Back to the gun:
Jony, if you were to call me when I worked at AirForce, here is what I would have had you do.
First I would have had you reinstall the 12-inch barrel on the gun and shoot it at a target. Don’t sight it in. I just want to know if the gun still shoots. I want to know about the size groups you get at what distance. I also want to know what pellets you are using.
If the gun shoots well with the 12-inch barrel the problem has to do with the 24-inch barrel – either the barrel itself or the installation. If it doesn’t shoot well the problem is in the valve or the firing mechanism.
Can you do this for me and tell me how the gun shoots?
Believe me when I tell you I have talked other new gun owners down off the ledge after they had an experience like yours. I have never lost one yet, and I’m not starting with you. We will find out what is wrong and we will fix it.
Please tell me how much shooting experience you have with your SS, and what that experience has been.
B.B.
Okay, this is so off topic it’s ridiculous.
But it is the funniest thing I’ve ever seen…if you’re at all into cameras it will crack you up. But just imagine he (Hitler) is talking about an overpriced air gun:
http://www.youtube.com/watch?v=tnwf2RShNV0
CowBoyStar Dad
Sure thing B.B. Thank you very much.. I’ll keep you (and everyone who can pitch in) posted…
You know?? About seating the pellet correctly, I will try to seat it deeper to see what happens… I will also change the barrel…
About the open sights… The rear sight has only one screw in the side and two in the top… I took off the one in the side, and it won’t even fit the bottom rail, the upper accessory rail, nor the upper handle bar… I saw the DVD and it is supposed to slide in the handle bar very easily… My rear sight won’t even enter… It must be a factory defect.. I already called P.A. for an exchange… Its weird isn’t it???
I’ll do everything tomorrow…
Cheers,
Jony
P.S.: I know that the rifle has potential because 5 out of 25 shots hit exactly were I positioned the sight… LOL… I just need to figure out what’s causing the other 20 not to….
Jony,
You should never miss a dime at 20 yards with that rifle – EVER!
When we finish, your rifle will be able to shoot like all the others.
B.B.
Jony,
I don’t remember all the facts about the gun you are shooting. Is the 24-inch .22 caliber barrel sticking out of the frame 6 inches, or are you using a bloop tube?
B.B.
Robert,
My Beeman R10 used to eat mainsprings, too. I used an old metal R1 guide and the problem stopped. I think the extra half-inch or so of length gave the spring more support. I’d assume that the new synthetic spring guide for the current R1 should work as well.
Heavy pellets damage the spring? Put me on the “doubt it” list, too.
Ultralight pellets damage the piston? That one I’ll support.
Derrick
By the way, dielectric / silicone grease makes an excellent spring damping compound if you don’t have any Maccari tar. Thin coat of moly or copper anti-seize goes on the spring first.
Derrick
Jony,
Welcome to the Airgun World, specifically the Special Service Division known as Extreme Frustration. This Division only becomes activated during the first few hours/days/weeks of new airgun ownership. After at most a few weeks, they are called back, and what you will likely be left with is either a really fun airgunning experience or, at worst, knowledge of what airgun or dealer to avoid (e.g., Airguns of Arizona is such a troublemaker that they are known to the Attorney Genral of Arizona).
I have owned about 12 air guns of varying costs, and have found that Extreme Frustration can make its presence known even with really expensive rifles like yours or like the $3,000 Whiscombe 80 that I was trying to make work today after having received it in the mail yesterday (waited 1 3/4 years…the rifle had better work…imagine how long the repair wait must be?!!)
Despite the clear directions in both BBs blog and the enclosed instructions with the Whiscombe rifle, as well as the presence of a personally handwritten secret note by The Master Himself, I had to make 3 phone calls to David Slade (I was not about to bother Whiscombe simply because of my ignorance) in under an hour until I got everything to work right.
By the way, in a springer related blog the other day someone was surprised that the Whiscombe vibrates. Mine, #056, when using the correct weight pellet, after having adjusted the HOTS for perfection, and with no air restriction, does not “vibrate” in what is usually understood to be the meaning of the word. With air restriction there is a slight hint of vibration, and with a pellet that is not the one Whiscombe recommends there is the mearest suggestion of vibration. But when set up properly, it is quite a remarkable piece of kit, and vibrates to my way of thinking more like a firearm than a springer.
I think that the more money one spend the higher the expectation and the greater the potential for Extreme Frustration (defined as feeling the most angry/frustrated/helpless that you have felt all year).
The rifle that you own is the most reliable, simple, straightforward designed rifle that I own as well (I own a .25 Condor which I use with air and with CO2). In over 18 months and 3,000 shots it has never failed to shoot or shoot accurately, and I am completely confident that BB will be able to fix your problem over the email.
Of course, when I first got the Condor it would not work for me either, and I had to call Van once or twice for him to educate me. That did not hit Extreme Frustration, as the “problem” (me,not the gun) was addressed at once and I only suffered a non-working gun for under an hour.
I think that when testing an air rifle for accuracy in the beginning, one should use the best pellets. H.P. usually are not as accurate as solid points, and almost always so past 30 yards.
However, the difference with your gun between h.p. and solid point is perhaps 1/4 ” at 25 yards, and not the larger groups that you are suffering with. I am curious what BB diagnoses…my guess is that the barrel connection(s) is off, but I am really terrible with these things and am the last person to know. I suspect that your pain will be short-lived, however.
– Dr. G.
Volvo,
You’re right — that doesn’t look so bad. Look at it like the first year of marriage: a lot of silly problems, with some nice incentives thrown in. If the FX works out, you’ve gotten to know it better.
I would have died young on the bomb squad, too:).
Derrick,
I didn’t know that about dielectric grease. Of course I was always using ite to lube AirForce guns, and the stuff isn’t cheap, so I guess it’s just as well I never found out.
B.B.
Jony,
Based on B.B.’s advice, I purchased the Talon SS in .22 along with the 24″ barrel, but I included a bloop tube for each. When B.B. finishes, you’ll be shooting 1/4″ dots at 20 yards and being surprised when you miss one using either barrel, running HPA or CO2 at low, high or some where inbetween power. That’s the light waiting at the end of your short, but frustrating tunnel.
Dr.G. Thanks much for naming my nemis the Special Service Devision. Please keep us up to date on your Whiscombe rifle. Thanks
Volvo: just a question, does your shroud require an alinement tool when putting the baffels back in? Mr B.
………
Surprisingly… I was changing barrels from the 24″ to the 12″ barrel… And guess what… To make things worst… The end point of the tool I was using to insert the front screw that attaches the SS End Cap broke inside the screw, which was more than halfway in… IN OTHER WORDS… i am F#*%# up………….
There is no way I can take it out… I am way above frustration… I’ve tried already using a wrench to grab the little end of the screw to see if I can unscrew it, but nothing… What I have achieved is scratching the bottom’s rail surface…
Everyone has been very helpful… You have all cheered me up, but in less than one day I just give up… Probably I’ll just sell everything in Ebay or something… Except the rifle’s stock… Or probably I’ll just call AirForce to see what can be done… Oh whatever.. I don’t know what else to write, good night…
jony
Mr. B.
I have no idea. Now I’ll a glass of wine before I start.
Volvo
Jony,
Don’t think about it and don’t touch it again until morning, at least.
BB won’t forget about you in a day or two and Air Force along with PA will still be in business; the warranty also is not just 72 hours. You bought what you wanted and what you thought fitted your needs, so you need to get it working before you change your mind, but a night or even a day or two is not going to make a difference long term.
BB,
Yep, dielectric grease might not be cheap, but at least you can get it at an auto parts store on the way home from work.
Jony,
It’ll work out. I can’t tell you how many times I’ve been working on a customer’s $4,500 bicycle that they need RIGHT NOW for a race when the unexpected happens. It’s ALWAYS worked out. Time and patience will get you through this.
Derrick
BG_Farmer,
There’s INCENTIVES?
Derrick
Derrick,
Lack of penalties may be the best incentive one can hope for in some cases:).
B.B.:
I finally managed to unscrew the front setscrew, but now it will not go entirely down… And I won’t force it!! LOL… I don’t want to break another of my tools… Do you think that AirForce can take a look at it??? It has to be the hole the one damaged, not the screw; since I tried to screw in the one near the handle (which is longer) and it didn’t go in either… You know, this hole also gave me problem the first time I changed barrels, it was stiffer than the others…. Well, sorry for my stupid attitude, writing sometimes helps to relief stress… Thank you… AND I WONT SELL ANYTHING… yet… LOL…
Cheers,
Jony
Jony, Are you a man or a woman? Either way, probably best to give upon this gun.lltthere ar many signs that it is not for you. Not necesary to read between the lines. Return it where you got it while you can!
Wow, quite a day with airguns. Volvo, you’re in a new realm I have yet to experience with airguns….
Jony, good man to pull things together and not do something desperate like sell your equipment. I would really enjoy an Air Force gun if I could ever afford one so now that you have one, don’t sell it. I can very much identify with your predicament. It reminds me of the time I pulled my $1600 Garand out of the box which I had waited for for almost 8 months and couldn’t get the safety to work. Or the time I traveled an hour to pick up the Savage police rifle I had ordered (and paid for) only to find that that the dealer had closed up his business. It will all work out.
I will even go so far as to say that you are lucky. You’ve got a direct line to the former technical director of Air Force rifles. I have no doubt that B.B. will identify your problem just as my M1 gunsmith did with me over the phone. And the repairs at Air Force should not be a big deal, especially if you’re under warranty. The only way you could mess things up is by doing something that could void the warranty. Hang on and wait for B.B.
Matt61
Jony
If you were shooting bad groups with the bloop tube then the tube could be the problem. I could get 1 inch or just over 1 inch 10 shot groups with my Talon at 50 yards. After I put a bloop tube on the groups increased to about 6-8 inches at 50 yards.
Jeff
Bg farmer,
Thanks for the encouragement. Much to my disbelief, I did it. The shroud came off, the offending patch was removed, and while I was inside I gave every thing a good cleaning. Not sure if it is lead dust or graphite as you suggested – but everything was coated with it.
Couple of tense moments (I had the photo backwards from the rifle).
But once back together she shot an outstanding group. I won’t go into details, as I don’t want Wayne upset this close to Christmas. Bad enough the S410 makes more noise.
Anyway, thanks again.
Volvo
BG_Farmer,
Nice! Sadly, I can relate!
Derrick
Volvo,
Bro… thanks for thinking of me again..
Good job, but watch out, your turning into a techy… don’t be spending too much time fixing, instead of shooting now…..
Of course, think of the down time in shipping….. OK, ya done good..
Sounds like your about ready, should I start up the copy machine and run out a few pages of 25- 1/8″ dots, to swallow some .177 pellets? ….For your whisper of course..
Wayne
Jony,
Okay, I would normally have answered your first post about breaking the Allen wrench, but I waited and read all of them before I answered. After reading everything I see that you solved that problem, but gained a new one.
This rifle is clearly frustrating you. Today I want you to call AirForce Airguns and speak to them. They are aware of the problem, because I sent all of your other comments to them. They have suggested things you can do, but I still want you to call them and talk to them about returning your rifle for an examination.
The number is 877-247-4867.
The screw holes you are having trouble with sound like they are cross-threaded, which means the screw threads in the holes have been damaged by the screws. That can be fixed, but not by you.
Please hang in there. As so many readers have told you, this rifle is wonderfully accurate and you will be happy with it once we get it working properly again.
You never answered my question about using a bloop tube. If you are using one, and if the pellets touch the side of the tube on their way out, that can easily explain the inaccuracy. My Daystate Harrier came with a silencer that was misaligned with the bore of the barrel (a common problem with Daystates) and the gun wouldn’t shoot at all until I got rid of the silencer.
B.B.
Hello B.B.:
Thank you once again for helping me… Today I feel more relax and ready to work on things… Its good to know that the damaged hole can be fixed… I will call AirForce now and see what happens… About the bloop tube… nope, I don’t use one… Yesterday I only used the .22caliber 24″barrel, nothing else… Take care sir!!
Cheers,
Jony
Jeff,
I’m sure you read what I wrote to Jony about bloop tubes. What you can do to correct yours is drill out the muzzle just a little. My bloop tube has no affect on the accuracy of the rifle I put it on.
B.B.
BB
Yes I read what you wrote. The bloop tube from Airhog I had was made for a Condor. I sold it to Wayne instead of drilling it out. I will probably get another one from Airhog made for the Talon and if it has an accuracy problem I will drill it out.
Thanks,
Jeff