by B.B. Pelletier
Part 1
Part 2
Part 3
Part 4
Part 5
Part 6
Part 7
Part 8
Before I begin today’s report, here’s some news for those awaiting a Benjamin Marauder from Pyramyd AIR. Pyramyd AIR has sold out its initial allotment of guns. If you placed your order by May 7, you’re supposed to receive one of the initial allotment of rifles. All orders placed after that date should expect shipment by around June 21.
Crosman is overwhelmed with orders for the new rifle, plus they’re getting their production line up to speed. Therefore, it will be several more months before they will be able to fill all the backorders. The best we can advise is to order your rifle soon to get a place in line for the next batch of guns.
In this segment, I’ll clean, lubricate and assemble the .177 cal. Diana model 27 I took apart in Part 8. I have a deep dark secret. As much as I talk about Diana 27s, I actually have a slight fear of them when it comes to assembly. Even though I have long since learned all of their secrets, I don’t like the way they go together, and I find the challenge of assembling one unpleasant. Give me an R1 any day!
But I promised this and the rifle was in pieces, so I had to do it. This tune, which is nothing more than cleaning and proper lubrication, differs from what I did to my .22 caliber Diana 27 many years ago. I did that rifle before black tar was discovered, so I used a light lithium-based grease the Army used to supply for M1 Garands. I have a can that I’ve owned for 40 years, and it has served me well for light grease jobs like the model 27. But this grease, being light, constantly migrates forward into the piston seal, keeping it well-lubed all the time. So, my .22 Diana 27 (actually a Hy-Score 807) is one springer that never needs a drop of oil. It has its own reservoir of lube that will probably last a couple more decades.
I wanted to lube this .177 model 27 in a more contemporary way, to contrast with the other gun. I will show you what I did as we go. Of course, I’ve chronographed the rifle very thoroughly with several different breech seals, so I’ll compare the velocity and firing behavior after this job is complete.
First, we’ll clean
You may recall from Part 8 that this rifle was very dirty. I discovered it during the disassembly. The first thing I had to do was clean everything so the new lube wouldn’t contain any abrasive dirt. The compression tube is always the big thing to clean because you have to reach deep inside to remove everything. My approach has always been to wrap a strip of paper towel around a dowel or, in the case of this rifle, a cleaning rod. Use a rubber band to secure it. Then, saturate the tip with rubbing alcohol and wipe out all the dirt and old grease. This way is quick and clean because you can replace the paper towel as many times as it takes. The alcohol evaporates almost immediately, leaving the metal clean and dry.
When you finish, the inside of the spring tube will shine like a mirror–especially if the rifle is a Diana 27. After finishing that task, use the same paper towels and alcohol to wipe all the other parts. The piston and mainspring are the two hardest parts to clean after the compression tube, but they’re really no trouble at all.
I also cleaned the bore with a brass brush and J-B Non-Embedding Bore Cleaning Compound. Before this cleaning, the bore didn’t look very shiny. Afterward, it did.
When everything is completed, it’s time to lubricate the parts and assemble the rifle. The piston goes first.
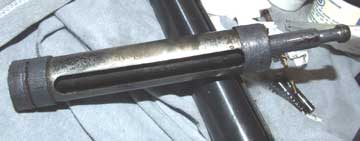
Like many spring gun pistons, the Diana 27 piston only contacts the spring tube at each end. The center is smaller, so only the enlarged ends need to be lubed. I use Beeman M-2-M moly grease for this.The piston seal is leather, as we discussed in Part 8, but I still coated it with moly grease. I know this will be transfered to the compression chamber wall, which is what I want.
I had a hard time finding the moly paste on the Pyramyd AIR website, because they didn’t list it under the lubes (the word paste probably threw them). They put it in the correct category this past weekend. When you can’t find something on the Pyramyd AIR website, type the product name into their search window. That often takes you right to it–if they carry what you’re looking for.
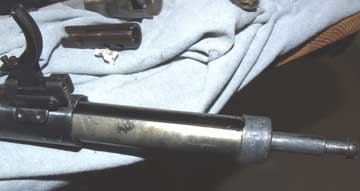
Once the piston’s in the gun, you can connect the barrel to the mainspring tube. This rifle has asymmetric thrust washers between the baseblock and the mainspring tube forks. On the right side, there’s one shaped washer that conforms to a complex shape on the baseblock, but on the left side the washers are mostly flat. One of the left washers has some spring built into it to keep tension against the forks.
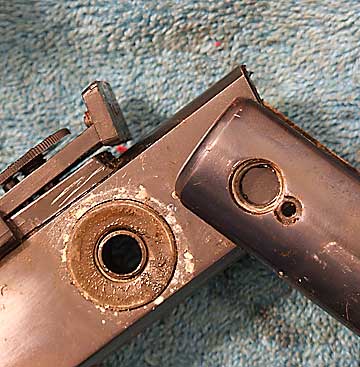
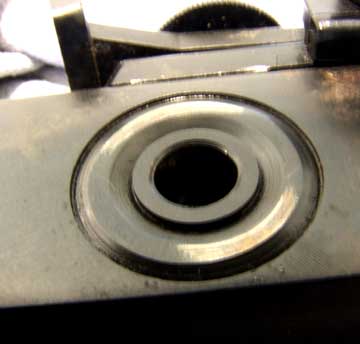
Before fitting the baseblock inside the mainspring tube forks, connect the cocking link. Once the baseblock is in, you cannot maneuver the cocking link to the entrance hole.
I coated all washer surfaces with moly grease. Fitting the baseblock back into the mainspring forks with washers on both sides of the baseblock is somewhat tricky, because those washers will be under some tension when inside the forks. You have to “shoehorn” them in, which means once the edges on both sides of the base block are started, the washers are easier to manage.
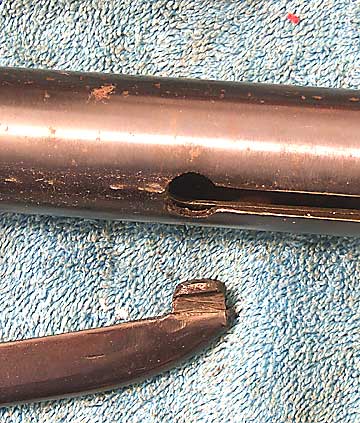
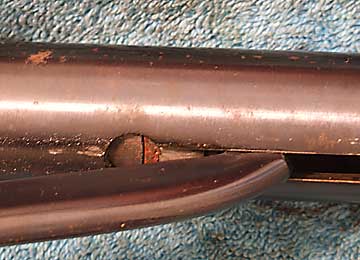
With the barrel in the forks, it’s easy to install the pivot bolt and its locking screw. Put moly paste on the shaft of the bolt before inserting it.
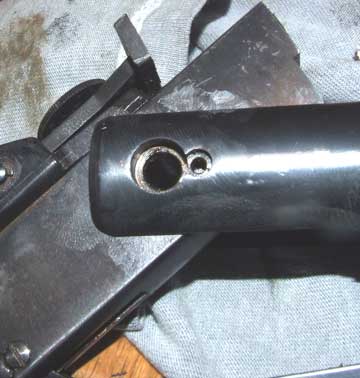
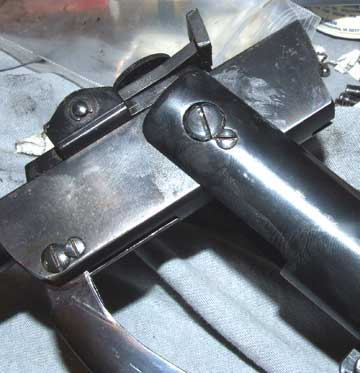
At this point, the mainspring is installed. Although my factory mainspring was canted a bit, I used it because I didn’t have a replacement on hand. I lubed the spring and spring guide with black tar for vibration dampening.
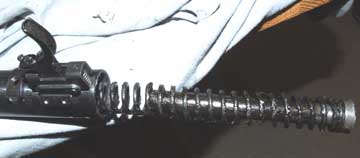
Here comes the hard part
Now, the gun is ready to be closed. The trigger is what holds everything together and in a Diana 27 the trigger is composed of many separate parts. I used to think the three ball bearings were the hard part, but an old mechanic’s trick solves that problem. Simply put lots of grease into each hole in the black cylinder, where the ball bearings ride and stick them in the holes. They won’t move during assembly.
However, the ball bearings are nothing compared to the trigger spring. It fits into a long slot on top of the black cylinder, but it acts upon the larger silver cylinder, as well. It moves the black and silver cylinders apart when the gun is fired. Cocking forces the two cylinders together, putting tension on the spring. This powerful trigger spring is actually held in place by the space BETWEEN the silver cylinder and the smaller black cylinder that rides inside it. The piston rod keeps the black cylinder aligned. It’s a complex arrangement.
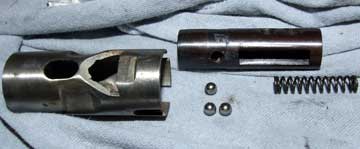
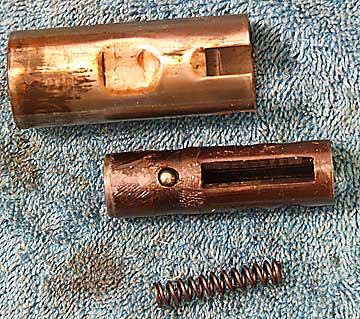
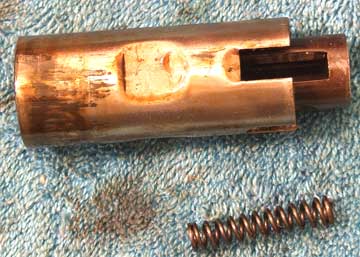
Once the trigger parts are inside the mainspring tube and the long slots in the silver tube are aligned with the two holes in the mainspring tube, you can start squeezing them together with the compressor. Remember that you have to pull the trigger to get it out of the way as the parts go together.
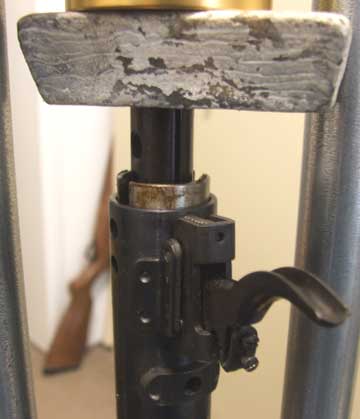
An alignment pin will help you line up the pin holes in the mainspring tube with the slots in the silver tube and the two pin holes in the black tube. Jiggle the tubes until they seem aligned, then adjust compressor tension until they’re aligned perfectly.
At this point, I should tell you that the rear pin is fatter than the front one. So, don’t put them into the wrong holes. The front pin may go in first, but the rear pin has more slop in the fit and usually goes in first. Consider it an assembly pin. After the front pin is in, the rear pin becomes loose and will fall out until you put the end cap back on. The front pin is the only thing holding the action together.
After that, it’s just a matter of installing the action into the stock and the job is done. And how did I do, you ask?
Next time.
BB , how often does this lubrication, tar’ring process have to be administered?
Ishaq,
I don’t know. The guns I did have never needed more. At least a decade, but probably indefinitely.
B.B.
Good Morning B.B.
Wow, that looks like real fun… but I’ve no time for such fun!! I’ve barely got time to shoot one fourth of the guns.. let alone work on them!
And reloading is still on the short list!!
I’m just so very, very glad that Vince likes to do that stuff!!
But thanks anyway for the look inside and how it works.. very interesting indeed!!
Have you ever heard of the “Record Champion Pistol” the “Blue Book of Air guns” says it’s similar to the Beeman P1..
Do you know how similar? Same factory?… It doesn’t look identical, so just wondering..
I got one last night as Dr. G was buying the IZH 46 right below it.. I couldn’t decide which to go for first.. then saw Dr. G’s bid.. so went for the Champion instead.
The Champion should be more collectible, right?… but does it shoot as well as a Beeman P1?
Wayne,
Ashland Air Rifle Range
Wayne,
By similar Dr. Beeman means the Jumbo cocks via the same overlever method as the P1. The gun was not made by Weihrauch, as far as I know.
I’ve never shot one, so I’ll be interested in hearing what you have to say about it.
B.B.
B.B.
Great… well.. I guess I’ll do that.. I was hoping you’d say: It’s better than a P1 and the most collectible pistol ever made…
but alas… not today:)
BTW… do you think that there is that much difference between the the older IZH46 and the newer 46M?… the dealer cost at PA has me thinking new one.. but if the older ones are better somehow…..
Wayne,
Ashland Air Rifle Range
Wayne,
The 46M is better because it has longer swept volume. It generates more power easily.
B.B.
Hi BB,
I am betting the 27 likes the regular grease better than the black tar.
I have one hint to pass on during the assembly. I use a twist tie to hold the trigger spring in the slot as I start pushing the assembly back into the receiver. When the spring is a little over half way in, I can remove the twist tie without the spring coming out. I had a heck of a time with that spring before I figured that out.
Keep up the good work!
David Enoch
B.B.,
Thanks for the sabot info. The Wikipedia articles were good.
Been enjoying this Diana 27 series alot. Thanks for the time and effort that you’ve put into this one.
One unrelated question please–your thoughts on a Talon SS with a 24″ .25 caliber barrel for hunting woodchucks at 85 to 110 yards?
Mr B.
David,
Your twist-tie trick is one I’ll have to remember. I’ve been using my thumb, but I run out of hands about that time.
B.B.
Mr. B.,
You are talking about a really long shot for an air rifle. I would first make sure I could hold on an inch before attempting that shot.
The SS would be a little light for chucks at that distance.
That said, with the right pellet and gun the .25 Condor would be abut equivalent to a .22 Long Rifle. That means yes.
B.B.
Yes, yes, yes. My first ever gun arrived today!
B.B.,
Thank you sir.
BB,
Did you do anything to condition the seal? It looked like it was in good condition, but wasn’t it dry after all this time?
BB, Is there a big difference between a BSA 2-7X32 and a BSA 3-12X40? Should I spend the little extra to get the latter? Its not much. Also some guys on an airgun forum were telling me that I should never buy a BSA scope because they are rubbish. Am I better of buying a Tasco scope in the same price range?
Ishaq – I’ve had two BSA scopes and I wouldn’t say they are rubbish, but they certainly aren’t as good as the two leapers I currently own. Have you looked at any of those? On my main rifle I have a 3x9x40 with AO adjustment. I think the AO adjustment is the most important feature you can have on an air rifle because with it, you can use your highest magnification level at nearly any range. I think you’ll find yourself shooting just as much if not more at 10 yards (meters) than you will at 50. The 3x9x40 AO is only 69.99 right now, which is probably a little more than the BSA and Tasco’s you’re looking at, but it is a great airgun scope!!
-Aaron
BG_Farmer,
The seal was conditioned. I had oiled the gun previously.
B.B.
B.B.
I had a dream last night about a post on the Marauder trigger. Did I miss that in the report or do we have another to come on this subject?
BG_Farmer, very funny about the primer.:) Actually, now that I think about it, the shell was probably moving due to the shock of impact nearby. There were only a couple where the shell really went sailing. I’m more intrigued by these 2 inch gongs that people were hanging from the target frames. Also memorable from that day was the large piece of wood that I blew out of the frame while trying to shoot the 1911 rested at 50 yards. What a disaster. Only 6 out of 16 shots even hit within the cardboard backing of the target.
Wayne, I have the Feinwerkbau for you. There’s one called the “Basic” running for a little under $1700. The word is that this is essentially the same as the aluminum one running $1000 more. All that’s missing is one of five options for adjusting the trigger. What a steal! 🙂 After this, you’ll never be able to go back to the S410
Matt61
Ishaq,
I’m using Leapers scopes on 7 air rifles right now. Excellent glass esp at their price points. Leapers also has good customer service replacing one under waranty w/o a hassel, but it took awhile.
Yes Anonymous has it right about the AO feature!
Mr B.
Matt61,
model number?… is this a 10 meter offhand rifle?.. or a field target rifle.. I hope the latter…
That will be the day!!! “After this, you’ll never be able to go back to the S410″…
fat chance!! …
… as you can tell, I’m open to the idea:)
Wayne,
Ashland Air Rifle Range
ohhhhh…I think the escalation just happened this weekend.
I’ve been happily shooting away for the last 18 months with my pellet guns (plus the boys Red-Ryders).
But this weekend a friend accompanied us to our favorite shooting spot. Brought his Gamo P-23…and CZ75 9mm and Henry Golden Boy (in .22LR).
Nooooooo!!!!!
CowBoyStar Dad
Ishaq,
Get the leapers…
and if you want.. I’ve got three new leapers 3-9x40AO in the box, that I just ordered from PA last month..
I’ll sell you one for $64 delivered..
wayne.burns@naturalyards.com
Wayne,
Ashland Air Rifle Range
CowboyStar Dad,
Yep.. that’s how it happens… turn quick and run like hell!!
or you’ll be gun rich and space poor in no time.. like me!
Wayne
Wayne, Id love to, but I live in South Africa mate. Lol does your offer still stand?
Matt,
There is another Marauder report coming.
B.B.
Ishaq,
HHHMMMM…
well, I guess not!!… shipping will be more than the scope!!
Wayne
Yup thats why we pay stuff like 120 dollars on the cheapest 4X32 scope.
Ok now I really need your guys help. After searching relentlessy I managed to find the only Leapers supplier here in South Africa. Ok so this is what he has for me: 3-9X44 80mm sidewheel, plus 2 piece 30mm mounts, plus flip-up caps. All that for 220 US dollars. But theres one problem. Its not AO. Its sidewheel. Can anyone explain to me what in the world that is? And whats the difference between AO and sidewheel? Should I buy it?
Also can I add that the price is good compared to other scopes here in South Africa.
Ishaq,yes by all means,buy it.sidewheel is the best version of AO and it allows you to make adjustments without having to reach the far end of the scope…so YES buy it before someone else does!!!then we’ll answer any questions that come up! Frank B
To save money, an Adjustable Objective scope works well and compact. It helps keep the crosshairs on target when you look through a scope and you can focus in on your target. Also , can help with estimating your range tot the target. Most fixed px scopes for air rifles are set to 20 yards. Some can be changed, yet not on the fly like an AO or sidewheel px adj. scope.
Sidewheels can help break down these ranges in more minute increments for precision shooting and shooters can make fine adjustment for target shooting at different ranges instead of using hold over techniques in a FT competition etc….
I started out with a 4x32AO Leapers scope and now use a 3-9x32AO scopes on some of my more powerful air rifles. They’ve held up over a few years now, even on my springer. These two I recommend to all new shooter to try.
btw…please excuse my typing…lately, I’ve been working 70-80 hours a week.
Thanks to Frank and Ajvenom. Im just going to close my eyes and buy it. Hopefully I wont see something on the net that will make me think again. Sidewheel it is.
Ishaq,
You also just connected with the person to deal with in the future!!
That’s a decent price here in the US.. and yes, that is a very good scope for the money…
You’re jumping up the ladder and saving yourself a lot of money/time in the future.. like Frank said, buy it and we’ll help you move up the air gun ladder of accuracy mo fasta quicker:)
Wayne
Ishaq,
I think you said you bought the Diana 34..
On the one I had, it was necessary to use special mounts for the barrel droop.. ( that’s where the barrel is pointing down a little in the front), so you have to adjust with adjustable mounts.. some mounts won’t hold up to the recoil of the 34.. so…
B.B. did a blog on them not long ago.. do a search and read it..
Wayne,
Ashland Air Rifle Range
Wayne,
The Feinwerkbau is a 10m rifle. I think that’s the only kind they make. I didn’t see a model number but it is fourth on the list of Feinwerkbau rifles on the PA listing and it’s going for $1772, a savings of 11%. 🙂 Careful, pal, it’s your money.
All, the verdict of reviews seems to be in, and the Savage 64 rimfire looks like it’s upholding the Savage name for accuracy and reliability. Too bad it doesn’t have the AccuTrigger but it’s listed as $152. Also, the good news continues to roll in about the Savage BTVS. A guy posted photos of sub half inch 5 shot groups at 50 yards.
Matt61
Ishaq,
Welcome to the wonderful world of air guns! Use this blogs search engine and read all about mounting scopes. There are some work arounds there to keep the scope from moving under your gun’s recoil and shimming the rear ring to correct for the dreaded Diana Droop.
You’ve got alot of knowledgable people here that are in your corner–ready, willing and able to give you a hand’s up.
B.B.,
How about using the Talon SS and its optional 24″ .22 caliber barrel for the woodchucks at the 100 yard mark? Shooting MOA from a rest isn’t a problem for me.
Mr B.
Ishaq,
most RWS rifles suffer from what’s called “barrel droop”. It’s exactly what it says – the barrel points down. You sometimes have to put a shim in the rear mounting ring or, the fellow that sells you the scope should sell you what are called adjustable scope rings – you can raise and lower the elevation of the rings to suit the droop or, you can buy a UTG scope mount base by Leapers. It’s not expensive, at least here in the States and it really helps keep the scope from moving from the recoil of the RWS 34.
Have fun – shoot the rifle with the iron sights first.
/product/utg-scope-mount-base-fits-rws-diana-34-36-38-45-with-to5-trigger?a=2298
Fred
(say hi to my cousin in South Africa – Avroy Schlain)
Matt,
Don't be so hard on yourself — you hit all those shells right where you intended:).
At my recent range orientation, the range safety officer (USMC ret.:)) had only one thing to add to the official rules: DON'T SHOOT THE &*&^ TARGET FRAMES! Apparently, the rifle shooters aren't bad, but they have to replace several frames a week due to weekend pistoliers:). I've half a mind (so my wife says) to give it a try, but I haven't shot a powder-burning handgun in 20+ years:).
BG_Farmer,
Well, I’m demoting myself back to the 7 yard range, so the target frames should be safe….
Go ahead with the pistols, but I would invest in an air pistol first. The powder guns, of high caliber anyway, take some time and expense to master.
Matt61
Thanks Wayne, Mr B and Frank B. Il be sure to ask questions when the scope arrives. Fred, the UTG scope mount base costs about 130$ here in SA. Thats too much for me man.
He told me that yes they are adjustable scope rings. Should I buy a one piece scope mount or a two piece?
BB,
Off-topic:
As I begin to fully grasp the importance of properly mounting scopes and realizing that it is almost impossible to find a rifle whose dovetail rails are perfectly aligned with the bore, I was considering the purchase of an adjustable scope mount.
My search narrowed down to the BSA Adjustable mount you have reviewed for us sometime ago.
At the last minute, I canceled my order. Nowhere on the details page indicate what scope objectives this will fit, whether this is medium or high mount. I have a 56mm objective lens.
I am here in SEAsia, and my friend in the US was supposed to buy it for me since ordering by mail is too risky for being stolen on the way.
I am still need of an adjustable scope mount. Imagine my regret canceling my order. Life lesson, it is not easy pondering on the “what ifs”.
I have heard of the complexity of the B-Square adjustables and I am not happy with my B-Square #25020. Sportsmatch adjustables are way off my budget. (They are the same as Beeman adjustables)
Is there a better adjustable scope mount there?
I have seen the Nam era Marine snipers fabricate gimballed adjustable mounts on an M2 cal 50 machine gun.
Thanks.
Daniel
Mr. B.,
Instead of you and me going back and forth about possible ranges at which woodchucks might be engaged, why not just take a shot? Then you’ll know for certain.
Use the most accurate pellet you can find, which is always the JSB 15.8-Exact for me. The new 18-grainer might also be good.
B.B.
Daniel,
The B-Square adjustable mount used to be the finest in the world. Now that they are being made in China, I can’t say that anymore.
But I have seen people with B-Square mounts who had not installed them correctly. They always argue about this or that fault in the mount, but when I take the mount off their gun it clearly was installed incorrectly. I have never seen an old American-made B-Square mount that I could not fix except when the screw holes were stripped by over-tightening them.
The BSA mount works except that it doesn’t have a scope stop. So it has to be butted against a stop, and when you do that you lose the vertical adjustability. To adjust it you have to push it forward and that loses all zeroing work that’s been done to that point.
The Sportsmatch also works well.
But are we trying to solve a problem that has not yet occurred? Do you own an air rifle with a droop problem, or is your concern the fact that you may own one someday?
You know, two-piece rings can easily be turned around and swapped back and front and that fixes many droop and sideways alignment problems.
B.B.
BB,
I own a pcp whose bore and dovetail rail are not looking at the same plane. I think I do not need a scope stop for a pcp. I do not have a problem with droop on this one.
I am zeroed at 30 yards, poi is up and right at 20 yards, left and down at 40.
Is the BSA Adjustable Mount ok for 56mm objective scopes? I wish Pyramydair mentioned that in their website whether it is high, medium or low mounts because that is very important in choosing a mount.
On my B-Square mount, it could be the new chinese production. My friend has brought it from the States. I will just keep it as souvenir. It is useless for the dovetail I got in my rifle. It cants to the one side as soon as I tighten the clamp.
Thanks.
Daniel
Daniel,
A PCP makes all the difference in the world! Get the BSA mount. It should be perfect for you.
B.B.
BB,
That is my one huge regret now. I cancelled my order at the last minute.
I cancelled it because I did not know if it will fit my 56mm objective. PA did not mention it in the product details. I ordered another mount instead. And I still have my mounting problem.
I cancelled it because I am not sure if it will work.
My US based friend is already here. He could have brought for me. I just can not safely order it by mail.
How I miss my younger years when I had an APO address.
Daniel
B.B.,
I came across your website looking for information on my old sheridan air rifle and it seems that you’re the go-to guy on air rifles.
I’m trying to repair my old rocker safety style sheridan silver streak c-series air rifle. It no longer holds compression, so I’m trying to disassemble it to change the gaskets.
Using advice from one of your previous posts,I got so far as to grind down a socket to make a square tool to unscrew the valve guide retainer nut. I removed it along with the lead gasket behind it, but now I dont know how to remove the remaining valve components. Does that vavlve guide behing the lead gasket have to be unscrewed or should it come out with a good bang?
Also, if I manage to remove all components and get my hands on some replacement parts, how do I reinstall the lead gaskets?
Hope you can help.
Thanks,
Devin
hi i have a diana model 27 i live in venezuela and i want to know if you can tell me where to find a barrel for it please send me the answer to mail adress araujo380@yahoo.com if there is a place in the us i can buy on line and use my po box to get it here and you know what it is please tell me thank you. The caliber of my diana is .22
Jose,
¿Por qué usted piensa que su diana 27 necesita un nuevo barril?
kevin
Jose,
You might be able to get a barrel from this man:
B.B.
Has anyone had any experience with Umarex USA? I have a brand new RWS mod. 48 that broke the first time I tried to cock it. The hinge post at the front snapped as I was pulling back on the side lever. Sent umarex an e-mail and they said they would repair it and pay shipping both ways. A week after I shipped it to them I got a phone call,and was told that the gunsmith determined that I had broken the rifle “probably” by pushing the anti bear trap release as the rifle was being cocked. Absolutely not what happened. The mechanism wasn’t even back far enough for the anti bear trap to grab it when the part snapped. No matter how many times I tried to explain what happened, I was told that I broke it. Rifle is being shipped back now at my cost.i felt like the yahoo at Umarex was calling me a liar. Left a very bad taste in my mouth. Warning to everyone. Don’t buy RWS and don’t deal with Umarex!