by B.B. Pelletier
Part 1
Part 2
Part 3
Part 4
Part 5
Part 6
Part 7
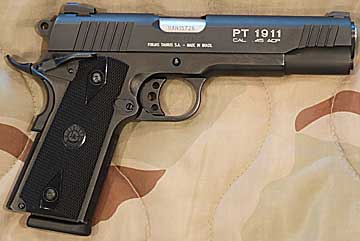
This series has gone on longer (over 2 years) than any other I’ve written for this blog, and it isn’t even about an airgun. However, the main reason I wrote this piece to begin with, was so I could share with you what I did when I bought something that turned out very differently than I supposed it would. Given my experience with airguns, it’s hard for me to be surprised by them anymore, but I thought if I could give you a window into what I do when life hands me a lemon, you might be more encouraged the next time an airgun surprises you.
To briefly summarize, I bought the Taurus PT1911 firearm because it was advertised as such a great value. I handled one at the SHOT Show, but of course couldn’t shoot one until I bought it. That’s not unlike many of you who shop online for airguns, except you may not get the chance to handle before you buy.
When I shot the gun the first time, I was devastated to see it fail to feed 8 times in the first 84 shots! I was angry, disappointed and frustrated all at the same time. I wished the person who wrote that ad about the pistol could have been there to get an earful. After time passed, though, and I calmed down, I decided to make some lemonade from my lemon, so I documented the experience for you readers.
In the beginning of this project, I took one huge fork in the road by deciding to fix the gun myself instead of sending it back to Taurus. Many readers advised me to do that, but I kept it and did the work so I would know for certain all that was wrong with the gun, but even more because in the 1970s I had been a hobby gunsmith for the 1911 pistol. I knew the design pretty well–to the point of building a match pistol from GI parts with a few aftermarket such as a barrel bushing. I installed match bushings for others, did match trigger jobs and stippled the frames of many 1911s for a fee. I felt I knew the gun well enough to take this risky step.
I’ve documented things that happened to this pistol at every step along the way so you could see how things were proceeding. And the pistol did improve once I isolated the problems, which stemmed from a faulty extractor that made the gun fail to feed. That part made the Taurus magazines, which have weak springs, faulty in this gun. But after I installed a new extractor, those magazines performed very well. However for 100 percent reliability, I rely on a special set of Wilson Combat magazines that are truly 100 percent reliable. Or at least they have been for over 600 rounds.
I also cooked up a handload that functions reliably all the time. It has slightly more energy than a .45 ACP factory load. It uses a 200-grain lead bullet instead of a 230-grain full-metal jacketed bullet and it goes faster than the heavier bullet while delivering less recoil.
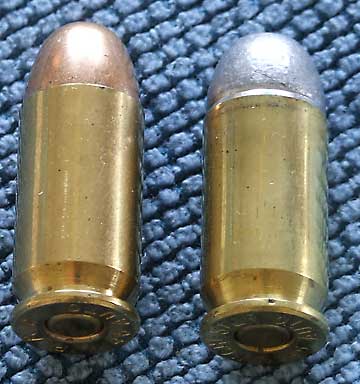
Based on the bullet I like, I bought a 6-gang bullet mold so I can cast my own lead bullets from now on. That cuts me free from everything but powder and primers which I buy in bulk. I can now shoot my pistol for about $8.00/100 instead of paying $80-90/100 for factory ammo. So, I shoot a lot more. In the approximately 1,500 rounds I’ve shot through just this pistol, the savings have amounted to no less than $1,050, or almost double what my reloading press, bullet mold and sizing press cost–combined. An airgun analogy would be buying the best pellets by the sleeve of 10 tins. One-time high cost brings huge savings downstream.
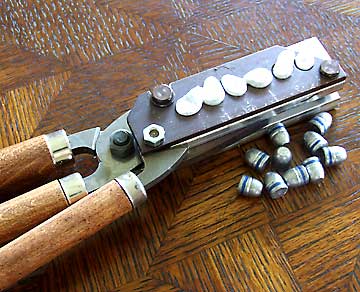
For Christmas my wife got me a Dillon reloading press that cranks out 400 rounds an hour, so now that my load is fixed and the bullet is fixed, I’m ready to crank out thousands of rounds of ammo for this gun. And the gun is ready to accept them.
All the problems I had seem to be in the past. The Taurus now seems to be as reliable as my Wilson Combat CQB I told you about in Part 4. It’s not as accurate as that custom gun, though I’ve learned how to hold it for the best accuracy it can give. And the difference between the $500 for the Taurus and $2,200 for a new Wilson buys a lot of anything!
I received some negative comments while telling this story. People seemed mad because I was speaking against a gun they either owned or thought a lot of. They didn’t understand that I was just pointing out the flaws that I encountered with my gun in the hopes that others would see them and know what could be done. For me, this was an educational journey, but some people thought I was out to crucify Taurus. Nothing of the kind! This is a success story, but we have to examine the failures to recognize it.
In fact, now that I’ve seen the project through to what I hope is a successful end I don’t mind telling you that when I need a .45, the Taurus always gets the nod. I trust the gun implicitly because I was there to see the transformation. No, I made the gun transform, so I know exactly what it can do and where it came from. Out of the box it had faults but today I would put it up against any other reliable semiauto.
So, what’s this got to do with you and airguns? Well, for starters, how about that next airgun you buy that doesn’t live up to expectations? You can trade it away or send it back if you like, but I hope this report has shown you another less-travelled path. You can take your lemon and make lemonade!
And perhaps it’s time to re-evaluate some of those old closet queens that you never shoot. Maybe with the right touches, they could become your favorite airguns. That’s the real point of this entire report.
Essentially, with your 200gr. Lead bullet at about 900 fps you've gone back to the original .45ACP loading. No surprise it works.
http://www.sightm1911.com/Care/45acp.htm
The 1911 sure has a passionate following. Some of these owners seem to have a hair trigger when they perceive the need to defend this design.
kevin
Kevin,
I obviously like the design, but admit it isn't perfect. The Makarov will shoot reliability rings around it. However, for a combination of power, accuracy and low recoil, the .45 ACP is hard to beat in a 1911.
B.B.
This was sent to the wrong address, so I posted it for him:
what are the best pellets for over sized bores? what are some good air pistols for about 15 yard grouse hunting (considering i already have a sheridan eb22, webley tempest and a cz tex mod 3)?
Dylan Blatch
Dylan,
In .22 caliber you cannot beat the Eley Wasp in 5.6mm. In both .22 and .177, the RWS Hobby fits tight most of the time.
A Beeman P1 would be a gun to look at. If you want to push out to 30- yards, get an AR-6.
B.B.
Goodmorning B.B.,
Hard to believe that your Taurus Blog was started 2 years ago! Yes that 200 gr. lead bullet @ 900fps has absolutlty past the test of time. Have you ever shot the Norinco 1911A1? Talk about alot of bang for the buck.
I'm sitting here holding a made in China Pioneer KS-2, .177 rifle that I bought new 25 years ago for $19.95. A nice little rifle. Had 4 at one time–wife, daughter, son and yours truly each had one. Son and I still have ours, the girls cann't find theirs???
Vince,
Are you familiar with this gun? I was wondering what, shooting wise these guns can be compaired to in today's market.
Word verification–isphspla–blogger must have had a bad night.
Here's a question from Rand:
Hi all. I found B.B.'s great blog site recently just after purchasing a new airgun, my first in over 40 years. It's a Diana 52, and it is a beauty. I posted about it in the comments following the August 2006 Diana 48/52 blog.
I plan to use the Diana 52 for hunting and for target practice and general fun. I'll be practicing with that rifle mostly at a range, as I feel it is not well suited for indoor or backyard (tiny suburban) target practice. So I'm now considering an indoor plinking or target pistol to have fun with around the house and to help me build up my skill.
My favorites in the multi-pump plinking category are the Crosman 1377C and the Benjamin HB22. I think some of the more affordable Competition 10-meter single-stroke pneumatic target pistols would be fun for indoor shooting too, and my favorites in this category are the Daisy Avanti 747 Triumph Match and the IZH-Baikal 46M Match Pistol.
Now I listed these in order of price ranging from a very affordable $56 for the Crosman to a rather substantial $365 for the IZH 46M. I'm torn. My budget would accommodate any of these. I notice that I could buy all of the first three for not much more than the cost of the fourth. Of course, buying guns one at a time grants repeated exposure to that new gun excitement, so I don't think I'll actually buy more than one right now.
My two main objectives run neck and neck. One is indoor target practice, which I will need a lot of considering I haven't used an airgun in over 40 years. My other objective is to just have fun.
Now all of these are .177 caliber except for the Benjamin, which is .22 caliber. .177 is probably a better choice for my purposes than .22. I'm not looking for a hunting pistol (yet).
I am leaning toward the low end of each of the two types of pistols, either the Crosman or the Daisy, as either of those seem like they would maximize the bang-for-the-buck in the fun category. Yet, the simple classic style of the Benjamin .22 draws my attention more than the Crosman 1377C. Regardless of my attraction to the competition pistols, I don't plan to shoot competitively. So any of the four pistols I've listed seem like they would be suitable for the sort of non-competitive indoor target practice and outdoor casual plinking that I envision.
Eventually I'll settle my mind on these choices. I'm close already. In the meantime, what are your thoughts? Are any of these guns more or less suited to any of my top objectives of non-competitive indoor target practice and just plain fun?
–Rand
B.B.,
I've also heard that a decent set of grips makes a difference on a 1911. ;^)
kevin
Rand,
I don't know if your into CO2… but if you consider it.. then check out the S&W 586
/product/smith-wesson-586-6-inch-barrel?m=115
This is so like the real firearm in size, feel and weight that it's
great for practice if you ever want to shoot the firearm version.. either way, it's very
fun and accurate..
Wayne,
Ashland Air Rifle Range
Mr. B – is it a breakbarrel? If it is, it's probably an ancestor (or relative of an ancestor) of the current B1/B2 series Shanghai breakbarrels. If it is, it's a very simple and crude design that – if it's made well enough – can still work quite decently.
B.B.
This should be a great topic for the weekend!
I wonder if you or/and Matt could give us a history of the semi-auto pistol in the military and police worlds… I can't remember any cowboy shows with semi-auto handguns.. so I know there is a transition in history..
I also know that for some time, the military and police used the revolver.. Was this just until the semi-auto was designed and made dependable?
It seems to me that nothing can be more dependable or flexible with the ammo type as a S&W 27 in .357 mag, which the police used for many years.. (some still do?).. why are they changing to semi-auto?
Wayne
Ashland Air Rifle Range
Wayne,
BIG JAKE! BIG JAKE! BIG JAKE!
One of the characters has an early semi-auto pistol of some sort. I don't remember what kind.
Kevin,
Like a fool I put those grips you gave me on the Wilson CQB. Little did I realize my wife's reluctance to give it up–even though it was a present to me! I do get to shoot it, though, and those grips make a huge difference in how it handles.
B.B.
Wayne,
There have been a few cowboy movies with semiautos in them. I saw one a few years ago where somebody had a Luger!
The Texas Rangers carried 1911s when they came out. But those days (after 1911) were not the high glamor days of the American west. Only Pancho Villa was left at the time of the 1911.
B.B.
Vince,
I just researched Big Jake online and I think that was the one! I remember Bobby Vinton in it, because of his singing career. I think someone travelled around in a Model T that was getting stuck all the time or something.
B.B.
Vince,
BIG JAKE? how did I miss that one?
He couldn't be a real cowboy!! What color hat did he where?
I sort of remember someone with that name.. but, alas.. too vague…
Wayne
Does anyone know anything about the Crossman CB40? Pyramyd AIR is selling this dicontinued pistol. Maybe a collector's item one day. Any information would be helpful other than that which is posted on the product info. Thanks.
Night Owl
just two letters
CZ
great guns.
al in ct
"Discontinued" I meant, that misprint just sounds weird. Big Jake? The John Wayne movie?
Vince and B.B.,
Was the gun a Broomhandle Mauser?
I'm trying to remember, without any success, which bag guy carried a Lugar instead of a Colt SSA. The only thing that, I think, I'm remembering is that the bad guy was a contemporary of Billy the Kid.
The Chinese gun is a breakbarrel.
Big Jake. Classic John Wayne.
It was his son Michael (in the movie and in real life) that had the semi-auto. I think I remember it being a 1911 even though the movie setting was 1905. Big Jake (John Wayne) said, "How can you have a model 1911 when this is only 1905?" Michael said his mother had bought stock in the company and they got the advanced model to try out.
kevin
Mr B.,
Don't know if this is the movie you're thinking of but in Joe Kidd (Clint Eastwood) one of the bad guys had a semi-auto with a detachable butt stock (could have been a broomhandle mauser. my memory is fading). The bad guy was killed by Joe Kidd when he fell through the trap door while he was pacing/keeping watch in the bell tower.
kevin
I was wrong. It was Chris Mitchum that played Big Jakes son Michael.
kevin
B.B.,
Well, at least she lets you shoot the CQB once in a while. Good to know they're getting used. Just sat in a box at my place.
Not sure you're a fool. I've learned if mama's happy, everyone's happy.
kevin
BB,
This is quite possibly one of the best articles you've ever done. It has inspired me to take on the piles of broken guns in my closet and I've learned alot about the Taurus 1911, which still seems like an excellent value at 650$.
Shadow express dude
Re: .25 Kodiak w/Macarri springs.
I was just chronying @ 10 yards the difference between the Eun Jin 35.2 grain and the Beeman FT 21 grain pellet in this extremely powerful spring rifle.
I found it interesting that the Eun Jin went 585 fps and the FT went 750 fps, so that both yield the same power at 10 yards of…26 1/2 ft./lbs.
With many spring guns the lighter pellets can yield more power, the opposite of PCP guns. This was a surprise finding.
– Dr. G.
All,
While were on the topic of handguns, has anyone got any experience with the Ruger KP345PR series? Are they any good? Would you chose that at 400$ over a Springfield GI at 550$ (my predicament). I found it hard to find reviews, which is why I'm asking here.
Shadow Express dude
B.B.
Right on about working on guns to bring them up to speed. If anyone has a problem with their springers, or even if they don't, they should consider sending them to Rich Imhoff or Mike Melick for a tune. Rich turned my B30 that was the source of multiple returns and much grief into a great-shooting rifle that gets 900 fps. Mike's work in some ways was even more magical in taking my IZH 61 that was hardly functional and making it even better than before. Like Herbie in the Love Bug, the IZH 61 has refused to be displaced by the newcomer B30/Red Ferrari and has fought its way back to equality. I think it has benefited from an interference effect by which it makes the somewhat stiff trigger of the B30 appear to disadvantage.
B.B., as I recall, the only problem with the Taurus was a burr which had to be filed off the extractor. Weak magazine springs seem to be a very common problem with semiautos. Interesting that the muzzle velocity is about the same as the B30. Note, Rand, that you can shoot your RWS 52 indoors easily enough by backing your target with duct seal. Just ask if you have questions about that.
All, for once I'm going the route of expense and quality. My SW1911 has functioned flawlessly, and it has been more than worth the 1K I spent for it.
Kevin, let's hear any objections to the 1911 design. I wish to learn. Is it the reliability problems with the 1911 compared to modern pistols like the Glock. This is particularly surprising in view of its history. I've heard that the problems are associated with tightening parts of the 1911 into a match mode. Loosened as they were for GI pistols, it is quite reliable. I wouldn't know from personal experience.
Matt61
Night Owl,
RE: Crosman CB40
I've had a C40 (silver colored version of this gun) for about 10 or more years. It's a revolver disguised as a semi-auto as most are. As one of the Pyramyd customers reported, the right grip is indeed kind of rattly. I cut some walnut grips and tightened up the fit. It's fairly accurate–probably in the 1.75" range at 10 meters. It's not a serious target gun, it's a fast shooting fun gun. Mine wears a red dot–there's a built in 11mm dovetail on the op of the "slide". One thing I haven't seen mentioned about the gun, the serrations on the trigger are very aggressive and I found the gun painful to shoot for long periods. The trigger pull is also pretty high out of the box but did break in and lose about a pound or pound and a half in the first 6 months. I rebuilt my gun a couple years ago swapping to a lighter trigger spring and removing those serrations from the trigger. It's not a gun that lends itself to home repair like a 2240 or even a Crosman 357.
The barrel in my C40 has the nicest bore polish I've ever seen in an airgun. When the gun came out, it was hailed by many airgun writers as a return by Crosman to their quality metal guns of the past.
Derrick
Wayne,
My understanding of the introduction of semi-auto pistols is as follows. First, I had forgotten completely about the broomhandle Mauser of 1895 which definitely precedes the 1911. It worked well enough since it was used through WWII, and both it and the Luger seem to have represented perfectly good semiauto designs that have not been pursued. Perhaps they were undercut by the simplicity of the 1911.
I believe that the 1911 was actually initiated in 1903 in response to the Spanish-American War where American soldiers could not stop drug crazed Filipino tribesman with a stream of bullets from the .38 revolvers they were issued. The 1903 design had some problems that were corrected somewhere around 1907 to create the 1911, and the rest is history.
As far as the police adoption of semiautos, police on this blog have written that semiautos offer improved firepower over revolvers in the form of higher capacity, quicker reload, and higher rates of rapid fire. I don't know if anyone knows exactly why semiautos took over when they did. My guess is that it was in response to the heavier firepower carried by criminals as in some incident in L.A. where the criminals wearing body armor and wielding assault rifles, outgunned the responding police. The plastic pistols may also have introduced a reliability factor that was absent for people who didn't know how to gunsmith a 1911. And I've heard that double-action autos also allowed police to avoid carrying 1911s cocked and locked which wasn't good for their image although I don't know why they couldn't have carried their pistols with the hammer down on an empty chamber.
Matt61
Kevin,
John Wayne as "Big Jake" sounds right… but I just can't remember a semi-auto in any cowboy shows…
I must have blocked it out… knowing I'd have a prejudice 40 years in the future:-)
Am I hearing that the 1911 was developed in that year? Was Browning the first designer of a semi-auto handgun?
Wayne
I am glad to hear about your making your taurus a fully functioning firearm, and I think your lesson of turning a lemon into lemonade can be a good one, but I know by experience that sometimes you just get rotten lemons! many of the guns I have had problems with are cheaper guns make no mistake, such as the crosman phantom, I really got a Friday model with that gun, and like you I also decided to stick it out, and now I'm regretting it because every time one problem is fixed, another one appears. So I think you really need to know how bad the problem is, and really need to know whether it is even worth it. In it's current state, my gun needs over 50$ in parts to repair, and that is quite a heavy repair bill for a 100$ gun.
So be sure you are up to it before you undertake a job like this! because sometimes the end just can't justify the means.
Derrick38
Thanks for info. The idea of getting a discontinued airgun brand new appeals to me. Just to have in my collection. Not so much to shoot with all the time. I'm still making up my mind as to which gun I will be purchasing. But with your comments I will make a better choice either way. I thank you again.
Night Owl
Nick,
You are right, of course. I knew the Taurus was going to be a gamble to fix. What if I had uncovered a host of other problems? I guess my decision wouldn't have been so good in that case.
And with all the MIM parts in the gun I wasn't sure how much would be wring with it. At the worst I guess I would have invested the purchase price again to make it right. Ot even the gun might never have been fixable.
I certainly lucked out, which of course is part of the story I'm trying to tell on that particular model.
B.B.
Wayne,
I believe Hugo Borchardt gets the credit for designing the first semiauto pistol. His gun turned into the Luger.
Browning designed a semiauto conversion of a lever-action rifle well before he got into pistols, and his first pistol was the model 1900, I believe. But with the 1911 he went so far that even today there doesn't seem to be much that's better.
B.B.
SED,
I like Ruger and they do make some nice guns, but the 1911 design is proven over a century of use and modification. I vote going that way.
B.B.
SED,
The Taurus IS a great value for the money! I'm not sure that it's any better than one of the other 1911s selling at the same price point, but it's certainly worth the money.
Now that you have watched me test the heck out of this one there should be very little that can buffalo you with this model.
B.B.
Dr. G.,
It has long been the case they lighter pellets do better in most spring guns. Only those guns with weighted pistons do well with heavier pellets, as a rule.
B.B.
Matt and B.B.,
Thanks for the history lesson. I had no idea the semi-auto pistol went back that far. So, then a lot of police depts. stayed with there S&W 27 & 28 revolvers in .357 mag. long after the semi-autos came out..
Matt,
I'll have to differ with you when you say the semi-auto is easier or quicker to load! Forcing the rounds into the magazine has not been easy for me!!! Sure once they are loaded, changing clips is pretty fast… faster than sliding open the cylinder, popping out the empties, and loading up again.. but if one has only one mag. … well no way is it faster to reload that magazine over a revolver!!
And that brings up another issue for me! I hate to go looking for the empty cases that the Makarov throws up to 20 feet away, and not in the same spot.. I always loose 10% or so of the empty cases..
But with the revolver, I just dump the empty cases into my hand …
Wayne
Hey BB..where in the heck are you getting your primers from? Since the schmuck hit the white house I can't find primers and many kinds of dies.
Primers are hard to come by, but I have standing orders at several gun stores. I buy by the thousand and carry cash.
B.B.
Wayne,
I had assumed loaded mags. Otherwise, you're right; they are a pain to reload.
All, on the subject of ammo, Magtech .45 ACP with a 230 grain bullet goes for a little under 40 cents not including shipping. It's awfully dirty but shoots fine according to many reviews. I can't figure out why it is available when just about everything else seems backordered.
Matt61
Annon,
It's not the "schmuck" as you call him, fault.. the FEAR a year before he took office is what has emptied the shelves of ammo and reloading supplies…
that fear was promoted by our old buddies at the NRA in order to save the election.. which didn't happen anyway… so get your anger aimed at the right spot…
we got a real big backfire.. IMHO
Wacky Wayne
Actually, Wayne – remember that the 2nd Amendment was intended to make it difficult for an onerous government to oppress the liberties of the common man. In that light the reaction of many gun owners was not entirely without reason.
The current president promised (and is pursuing) a significant expansion in the scope, authority, and reach of the federal government. Many people believe this is a good thing, but many do not. And in any event it can reasonably be argued that this expansion is not particularly conducive to liberty.
At various times the president has issued conflicting statements do not reveal a consistent attitude with regards to the 2nd amendment. When the Supreme Court decided that it did indeed confer an individual right, he said that he agreed with that ruling. But at another time he wants to 'get guns out of the inner city', which implies revoking that very same constitutional right on the basis of geography. Not on the basis of 'due process of law', but on the basis of where you live. Many people don't believe that the application of constitutional right should be quite that arbitrary.
For those who are interested in simulating airgun performance on a computer, I just ran into this.
http://trettel.org/bags/
A.R.
Funny how other topics get discussed here on an Airgun Blog! LOL
Anyway, just for ya'll debating the semi-automatic in "Big Jake" it was a doctored Walther P-38, dressed up.
Here is a pretty good web site that deals in Movies/Television and our favorite subject, Guns!
http://www.imfdb.org/index.php/Main_Page
http://www.imfdb.org/index.php/Big_Jake
If you were not aware of the site, do take a look around and enjoy, they update stuff every so often.
You'll see it listed as
"Movie prop: "Bergmann 1911" "
🙂
Vince,
You're right,
All leaders on the way up say what they think people want to hear…
So he was talking to his base on one hand, and glad not to half to do anything that would shake the middle and any of the right he collected from default of a terrible prior job..
That same tactic got the prior leader elected.. and a second term
IMHO they all have to play games to get elected and stay in office.. nothing they say they will do.. gets done… on either side..
that's why I'm an independent.
and believe in small business.. and very small government…
and a peoples well armed army..
and no government army..
That's what I think the Second Amendment is saying.. smart people well armed in their homes and ready to protect themselves and their neighbors.. and maybe called further.. with a well thought out and considered act of congress..
Wacky Wayne
And the since the history proves the leaders mostly do the opposite of what they say.. I as a gun owner and collector, feel encouraged!
And by default or design.. who knows.. the people are now armed and well stocked with ammo!!
And one of the strongest elements of the economy is now the retail arms business.. which is a good thing..
Why would the leaders mess with that..
They won't.. count on it!
But also count on paying higher prices..
Wacky Wayne
Why is the dearth of ammo and loading supplies continuing more than a year past "the fear" that spurred increased demand? Increased demand usually results in increased supply, at least to the extent that it is profitable for the suppliers.
The level of demand over the past year suggests that ammo manufacturers could have reaped major lucrative revenue by ramping up production starting over a year ago. The continuing shortages suggest that they have not done so, or that the demand is even greater than anyone could reasonably anticipate. Frankly I doubt that. Can it be that they lack basic business savvy? Or perhaps they can't get funding to increase production capacity. I can't venture another plausible explanation for it.
–Rand
Hey guys, I have a quick question about multi-pumps. The comparison is between a multi-pump rifle and multi-pump pistol. Would a m-p pistol be easier to pump than a rifle? or would they have the same resistance on higher pumps. also, either on high power or low, which would be shooting louder? definitely, the rifles are more powerful than pistols. thanks very much!
Rand,
How about this one..
The price is high because of the shortage.. Just fill the shelves enough the keep the two or three shift production going… no new plants.. reap profits from existing capital… keep the shortage going as long as possible..
Didn't you watch the oil prices?
It's a combination of greater demand than planned for.. and not adding production capacity..
If the supply came back to normal.. the prices would drop.. and the cost of their new production capacity could put them into bankruptcy..
I really do believe it's Fear..
Fear that the laws would change…
..and Fear that the price would keep going up… so buy now..
and Fear that you won't have it when you want to shoot something… (that was mine)..
So I stocked up every time I got a chance at what seemed to be the best price at the moment!!!
The average price I paid the last 6 months, is twice what I paid when I started into firearms about a year ago.. (other than shooting my Dad's .22 LR 550-1 semi-auto rifle since I was 8 years old)..
Here is where Tom says I told you so!!! and was he right again!!!
Well at least I have a very large and growing supply of empty cases!!
Business savvy they have.. count on that one too!
Wacky Wayne
Multi-pumps:
A multi-pump rifle is typically easier to pump as it's longer giving you more leverage.
The rifle wins on the low sound front, too. Longer barrels on multi-pumps, CO2 guns, PCP guns are quieter.
The rifle typically also delivers more power in fewer pumps than a pistol. Some of this is due to the efficiency of the longer barrel. Some is design as the rifles often have a longer pump stroke and can thereby push more air into the valve.
Have a great Saturday Everyone,
I off to Salem, Or. for the first Field Target contest up there. They are getting a club started there too.
It should also be fun to meet some folks from up North in Washington who are coming down to help the Salem folks get their club started.
I hope I didn't get anyone angry at me with my comments earlier.. it's only one man's observations..
I'll let you know how bad I got waxed on Sunday..
Wacky Wayne..
Wayne,
Safe travels, buddy. Have fun.
Derrick
As I remember, a policeman was charged and killed by a bad guy's semi-auto as he tried to reload his revolver. I think that was the LA incident. I do know that the police (in the media) blamed the movie, HEAT, for giving the bad guys the idea of using assault rifles, body armor, etc. I was grimly amused when new legislation was passed that provided longer prison terms for perps who wore body armor in a crime.
The 1911 is superior to the Glock in one aspect that I know of: this may have changed, but once upon a time the Glock refused to function reliably with cast-lead handloads. It may still, for all I know.
The choice of a sidearm can be completely serendipitous. I once fired a police friend's .357 Taurus revolver. Use of the ejector rod tore up my left hand in ejecting the spent cases. Now, this may have been the fault of hot handloads or even +p+ ammunition, but the fact is, ever since this negative experience, I have steered clear of the Taurus brand.
When I lived in predator country, I carried a .44 magnum with heavy handloads. Never had to save my life with it, but it made me feel a lot safer carrying it.
Wayne,
NRA is not in the fear business. Most of their time and money is spent in education and training of military and police. It was founded for this reason after the Civil War.
The ILA portion of NRA is in the political business is not very good at it (IMHO). They try to tell the truth most of the time… and the truth is seldom as powerful as a well told lie. But they are evolving and getting better at mass media delivery of a message.
Our current President and Congress does worry many. The President is rather a radical person and a typical elite liberal that thinks everyone else needs to be strictly controlled; but he and his buddies are above the law.
For proof look no further than his "stupidly" comments concerning the poor maligned police officer. This is what makes people worried. The pattern is obvious.
No it is just the DEM's; there are many elitist liberal REP's too. Thus the need for a third conservative party. Too bad none are emerging.
Sorry Ron Paul supporters; he just a bit too odd to capture the support of the middle class voters.
DB
p.s. I still think this is the wrong place to discuss politics. Just had to defend the NRA and then it just grew.
Wayne,
Is this your first field target competition? Are you going to use the S410 or the USFT? Let us know the outcome.
On the subject of politics, there is a range of opinions out there about Obama which is as it should be. But whatever his views and intentions may be about gun control, I have a little trouble believing there is going to be any action on that front in the immediate future. He has to worry about North Korean nukes, the economy in the tank, health care under siege, the Afghanistan War, the transition of Iraq, the army falling apart, the abortion question as well as every single thing that comes out of his mouth in front of cameras. How he even functions I have no idea, and that goes for all the presidents. For him to open a new front to increase gun control I think would be the act of a complete madman. Anyway, the message is to stop hoarding all of your ammo–at least until I complete my hoard. He he.
By the way, one interesting front to watch in firearms development is the advances in super-long range sniper rifles. I just read about the Remington Modular Sniper Rifle (MSR). It is a bolt-action with an AR type stock and can rapidly change between .308, .300 Winchester, and .338 Lapua. It is supposed to shoot MOA at 1 mile. However, my money is still on the Ashbury International Group AIG Asymmetric Warrior another bolt-action AR in .338 Lapua only which can go half minute at that distance!
David Tubb has a video called The One Mile Shot where he gets in the black on a 1000 yard target at one mile (shooting a 6mm BR). That would be lame compared to these rifles.
Matt61
Wait…the Army's falling apart? When did that happen (and where was I at the time)? I knew they were unable to get the armor they need for their battle vehicles, and I knew about the high suicide rate.
Wayne,
You should be getting home anytime now. Hope all went well and that you shot extremely well, beginger's luck! How about a preview before you call it a night?
Derrick,
Beg to dffer with you good buddy, but my 1377 is much, much easier to pump than my 392.
To all,
I am a 65 year old conservative white guy. Got a free trip to South East Asia in 1967. Worked, paid taxes, raised two families, retired and for the first time in my adult life I am afraid for and afraid of my wonderful country!
If someone says that they are a Christian and believe that marrage is between a man and a woman they are vilified and personall attack for simply expressing their belief–like Miss California. The absolute basterdizing of the Constitution. The Second Amendent means that you can cary a gun period.
The corruption that lead to this administration's election, the taking over of the auto industry, by what athority?! That's not in the Consitution.
Sorry folks just got all wound up tonight.
Mr B
Well, good guess on the timing!
Just got back and had to check in.. to see if I was kicked out for starting the political discussion:)
I had lots of time driving by myself up there, to think it through.. Still feel the same.. but it's just my humble opinion.. so I should just keep it to myself.
but before I do..:) let me say I'm in no way defending the actions of our leaders.. present or past.. I feel we have the best government money can buy.. period.. it's bought and paid for.. Dem or Rep.. bought and paid for.. and not by small business and the people I'm afraid.
Now, I'll start a report on another comment.
Very Wacky Wayne..
Mr.B,
Agreed. Lots of scary things going on. Hate Crime bills are very scary. Seems to me we already have laws to protect people from violence.
Why do we need new laws? Only one reason seems logical.
DB
Mr B,
I do not see why you are "afraid for and afraid of my wonderful country." I don't say this to instigate trouble, instead, I hope you can elaborate. I understand that there is a lot of controversial legislation in Congress, but the greatest thing about this country is nearly all legislation passed during one administration can later be undone. Not very time-efficient, but if you want a quick decision, you need a dictatorship.
Additionally, though I believe the Second Amendment is an individual right, I don't see why any civilian would need an automatic weapon. Not to say they should be illegal, I just don't see their purpose.
Finally, I am curious as to what corruption you are referring to, and what you believe should have been done with the banks, auto industry, etc.
I like the airgun discussions better,
Jake
I got up at 2 in the morning, drove and slept a little in the car and got there at 7 am to help Darren set up.
Darren is a custom pistol maker.. looks like mostly crosman. He and his buddies shoot pistol contests, and don't even have a basic FT rifle.. most of their group shot field target with their pump or CO2 pistols!! They are going to be great competitor when they get setup.. they did very well with the pistols!
Rick Knowles and I think 4 others came down from Washington State.. sorry I can't remember their names now.. It seemed like about 30 people total and about half had rifles..
I had brought the 12 ft lb USFT and the Air Arms S410 with a single shot tray.. I threw caution to the wind.. pun intended:).. and used the USFT… while offering the S410 to folks who had pistols.. but no one took me up on it.
I saw a Marauder, R-9, two AAs400s, Ricks EV2, Terry, who shot with Rick and I, used an 8 ft lb. 10 meter FWB.. and twice I saw him hit the kill zone and the target still stand..
Then, his rifle slid off the tree he had leaned it on… and he lost his scope settings. we let him reset up.. but he wasn't the same… very sad!
So, the contest became between Rick and myself…
Poor Rick was at a handicap, he was wearing a shooting harness, and sweating like crazy in the heat.. He had to take it off and on all the time…
Too much work for me.. I'm not going to get one now that I see what it's all about!!
It turns out I was the only one of the semi experienced shooters not wearing a harness.
Rick got ahead of me early on the second kneeling lane in the open field, where the wind was gusting to maybe 10 mph.
I misjudged the wind and scored one for a target hit, instead of two for a knockdown.. (we were using "hunter class rules", since we had such a wide range of guns and shooters)
Finally, we moved into a small patch of 8" doug fir trees.
Darren and his brother were in the process of clearing this patch for their FT Course.. They had worked very hard for a week getting it ready, but it was still a mess of fallen trees and branches.. which sort of made it more fun.. shooting.. not setting up!! But it's going to be great when they're done!
Well "Clicker" Rick and I didn't miss many more.. and I stayed on his tail and ended up second.. to my "Holdover" amazement!
I'm sure it was because we moved out of the wind into the trees.. and most targets were under 35 yards .. The ones I only knocked down once were 15 yards with a 1/2" kill zone.. With my zero set at 25 yards, I'm still not holding over high enough!!
I guess I'm going to have to put some time in learning and setting up the "clicking thing"..
Rick said he would post the results on the FT forum.. I'll post a link when I find it!
Lucky Wacky Wayne
Ashland Air Rifle Range
DB,
Let's add open borders and the incredabely expensive, expanding illegal alien population, lying politicians like Barney Frank on O'Riley saying that he'd warned Bush about problems with Freddie and Fannie, where did the hundreds of millions of dollars, raised by President Ombama really come from,…..Wayne you're right in that we have the "best" govt that money can buy.
Mr B.
MrB,
Sorry, You're absolutely right. I was taking broad sweeping generalities about multi-stroke pneumatics.
Pneumo guy, please defer to Mr B on this one–he indeed knows whereof he speaks. There are some pistols that are easier to pump than some of the rifles.
Derrick
Just saw this one.
DB,
I don't think that President Obama's comments on the Harvard professor arrest (what you were referring too, I hope) show him to be elitist. I think they show that like all of us, he came to an initial conclusion based on personal history. As such, I believe he spoke before knowing all the facts. A mistake, but I believe we're all guilty of it. The only difference is that he's on TV 24/7.
Jake
PS – I agree with your last statement completely.
It would be fun, or enlightening, to go back through the news tapes and put the quotes from leaders, and next, the news report of the bill passed much later.. then the results of the bill much later still…
Do that process, over and over with each key promise.. and each leader… from about 1950 when corporate Americas' plan started, to buy America's leaders and sell off it's stolen assets…
..and invest the ill gotten bootie offshore..
I'm sure we'd see a pattern..
Now that I've dumped:)… can we go back to air guns and firearms and anything but politics… 🙂 just let me do it… you guys stop:)
But really folks.. I think we have been pretty civil… good job! and all good points of view to be considered… thanks
Wayne
Jake,
I am fraid of our country because of the control that the government is obtaining over all aspects of our lives and I am also afraid for my country becasue of what they're turning her into. No more Home of the Free and the Land of the Brave….at least that's the way read things right now.
Full auto guns are alot of fun to shoot, but the reason can be as simple as I want to own one. By the way, if my memory is sorta working, no legally owned Class III weapon has been used in the comission of a crime in this country.
Mr B.
Jake,
Anyone should be allowed to own any weapon they want that is suitable for self-defense, including so-called illegal knives, nightsticks, or automatic weapons. A nuclear bomb is not suitable for self-defense. A fully automatic weapon is. The bad guys have 'em, why shouldn't the good guys? Where is the sense in handicapping people who respect the rights of other people when everyone knows that there is no law that can possibly handicap the ones who don't?
The government has no business restricting the right of anyone to own any weapon suitable for self-defense; period.
–Rand
Wayne congrats on the #2 spot!
Sounds like alot of fun with pistol or
rifle.Sure wish i coulda been there even
just to watch:)
My 1377 is very easy to pump even to 12
pumps(only done this a coupla times to
see if it would dump the full charge,
it did:))so the short pump lever is not
a problem on this one.
You all probly know I like the 1911
but my usual choice for carry is still a revolver,normally a Taurus .357.
I'd still like to get an S&W in .45
so I can go from Long Colt to .45 auto
rounds in a revolver:)I just really
like multi purpose guns.
I guess on the political stuff I'm gonna
keep my Individual,conservative leaning
non Dem. or Rep. too big nose out of it
tonight.Most of you know how I feel
about it anyway:)
Safe and Happy Shootin to all
JTinAL
Mr B and Rand,
I understand that you should be allowed to own anything you want to, because you have the right to do so. But I also believe that you also have the responsibility to treat anything you own appropriately. No, the government should not force us to store firearms in a gun locker or with a trigger lock. But it is a good idea, for basic safety's sake.
I also believe the government shouldn't legislate things that should be common sense and what we can and can't do in our own home.
As far as Class III weapons go, I am aware of their lack of a criminal record, and I believe the current system is quite effective.
On a seperate note, does anyone have any suggestions on how to improvise a benchrest for stabilizing a CO2 rifle for zeroing?
Jake
Jake, use an ironing board,quick and simple
just don't tell the better half till you're done:)
BB I have a question for you. When shooting my crosman 1377 pistol pumping requires almost no effort at all. Crosman says the gun produces around 5-6 foot lbs of energy. I purchased a 760 thinking it would be even easier to pump only to realise it was twice as hard while producing the same energy. I also tested a benjamin pump pistol which was also much harder to pump. My question is why is the 1377 so easy to pump compared to other guns and why don't companies catch on to this and improve their designs?
I don't know why your 1377 is so easy to pump. I have one and it's harder to pump than my 760.
Have you checked the velocity over a chronograph?
B.B.
Jake,
You must be kidding right? Reason for owning a full auto today is the same as for owwing a low powered airgun. Fun plan and simple fun.
You can not defend your home with a 5fp airgun nor can you hunt with it. So why do you need one? Answer it is fun to shoot. Same for the full auto.
Full auto may not be your cup of tea… but why would you want to prevent someone else from enjoying it?
Yes full auto is more dangerous… thus the heavy regulation on them that has been in place for about 50-years. And it works.
More laws are not going to stop the crooks from owning illegal guns. Only law inforcement can achieve this goal.
About corruption… again you are kidding right?
DB
Jake,
We are not President of the USA. He is and should be much more careful.
His words can start riots and wars.
DB
About 1377 pumping. I've owned a two and both are smooth and easy for an adult or large child to pump.
A normal 8-year old should be able to get 4 or 5 pumps into it – and that is plenty of power for that age bracket.
DB
Well, back from my MC trip to NH and VT. Great roads and riding. I took my friend from NZ up there and he had a ball.
BB – I re-read part 2 on your review on the suped up 78G but you didn't mention the grouping sizes you achieved. Just curious what they were so I can compare to what my 78G achieved?
The Roanoke Airshow in Oct. I hope to be there again and perhaps purchase that Crosman Nitro from PA. Look forward to saying hello to you again, BB and Randy in VA.
Fred
I don't believe this – word verification is supingr!
1377 pump,
My 1377 has very consistant pumping (much more easy than my 760s). My 1377 shoots close to 510-520fps with Crosman Premier pointed pellets.
Shadow express dude.
DA TINGS I DO FOR YOUSE PEOPLES!!!
I KNOW that lots of youse are loosing sleep over that question – "How good IS the Chinese copy of the Diana 34?". And my sense of Christian Charity will NOT let me turn my back on my fellow man.
So I just ordered a B25S (synthetic stock) in .22, so that I can tear it down side-by-side with the Panther and shoot it side-by-side with the Panther. And so we'll all know what there is to know – and we'll have no more wailing and gnashing of teeth over the question "The Diana or the cheap knockoff?"
I spends my money so's YOU don't HAVE TO!!!!
Wayne: all I can say is "Keep 'em coming, my Sugar Daddy – I gots ANUDDER gun to pay for!!!"
($140 with 3x9x40 AO scope with target turrets and a 1-piece mount. Like I could pass that up anyway)
After much deliberation, I ended up buying a Crosman 1377C and a Benjamin HB22.
I bought the 1377 because of the classic appeal, the many positive comments, the capability to customize it and mod it if I choose to later on, and because it just looks like a fun gun to shoot.
I bought the HB22 for much the same reasons, but also because it looks like a pistol version of the old Benjamin rifle I had as a kid. Mainly nostalgic appeal, in the case of the HB22.
I've now got two orders pending at PA. One is from a week or so ago, because of some out-of-stock .22 pellets that I ordered for my Diana 52. But everything in my most recent order shows to be in stock, so hopefully it'll all ship soon and I'll have it by the end of the week.
Ooops – that last post about the 1377 and HB22 was from me – I forgot to sign.
–Rand
Fred,
The best one was just less than one inch.
B.B.
–Rand,
Waiting for the UPS truck for me is like waiting for Santa. I really appreciate the on line tracking of my package. I enjoy shooting my 1377 which is 100% stock.
Let us know what mods you make and how you like them please. Saw a picture of Derrick's 1377 with wood grips and pump lever which rally looked nice and also very functional.
Vince,
You're The Man! Thanks from all of us.
Wayne,
Congradulations on your 2nd place finish at at the FT. How did the guys do that were shooting the AAs400s?
Mr B.
BB,
Glad you got the Taurus to your liking — its always more fun when you can fix something:).
Wayne,
Great job on the FT. Ranked no. 2 in the Pac. NW FT conference isn't bad:). More glory and adulation for me when I beat you to the 200 yard bucket prize:). I agree — no more politics. Better yet, no more politicians:).
Vince,
No problem.. I'm too addicted to this airgun world to quit now!!
Since you asked, here is one for you right now.. Have you got a front sight that would work for a RWS 46 Stutzen? Or could you rework or fashion one? I sold a new one to someone and it must have got damaged shipping or I didn't notice it, when I opened the box to check it.. Anyway I want to make it right for him.. and I might have to have him ship it to you, if you can't send him one, he can put on himself.
Wayne
Mr. B.
I just got this email from Rick Knowles who was the acting FT director for the match.. since Darren is just learning..
"We started with a little clinic from Rick, he managed to shoot a perfect clinic; but used up too many of his good shots. We helped people get through the various positions and explained that if they couldn’t do a position there were options; but they didn’t get easier.
After a few teams had gone through the mandatory positions Rick suited up to shoot for points, missed the first target, close and huge KZ.
We didn’t figure out the difficulty rating but guessing it was mid to high 20’s.
Rick, shooting his EV2, missed another shot, forgot to click to finish with a 66/68.
Second place was first time FT Shooter and top Oregonian, Wayne Burns, shooting his USFT, for 64.
Wayne’s USFT is a former National Champ rifle, from the 2005 FT Nationals in Tacoma. Wayne had thought about getting it pumped up; but must be happy with it’s shots per fill ratio. (I just don't want to change the settings LD and Tim did to get it ready for the 2005 world championship.. and it didn't win the 2005 championship, it was the "prize" for a crack at the world championship)
Third was Carl Rettice, shooting his QB for a score of 60, tuned for at least full power.
In forth place was JD Dodge, with his S400SL ERB, scoring a 58, shooting around 15 fpe.
The remaining places were; Martin Cooney, Ralph Cooney, Terry (I droped my rifle and clicks are off) Cooke, Jeff Thatcher, Johann ?, Darren Thatcher, Josh Thatcher, Reed Thatcher, Loren Thatcher, Morgan Thatcher, Chris Thatcher, and John Mickel.
John finished last because he kept forgetting to write things down- he’s used to his Grand Daughter keeping score and keeping things honest.
The After Match feed was good too!! A good spread and smiles from everyone. Overall a fun road trip.
BG_Farmer,
Don't call it a NW conference.. I'd call it a fun shooting session.. Rick is "one" of the top shooters from Washington.. just one!!
But thanks anyway.. I did gain some confidence, and will compete again!!
And I'm ready when you are for the 200 yard bucket contest.. I just haven't decided whether to use the Diana 27 or Winchester 27… both are "Vince tuned" and set up with nice peep sights…
..oops forgot.. Vince set up the Diana 27 sights special for those long shots.. so I'm decided..
I Better set up a place to try and do it!! How big was the bucket we decided on?
Yep.. my lips are sealed on politics.. (sure you say):):)
Wacky Wayne
Jake,
Your benchrest position will improve with both front and rear bags like the Beeman version they sell at PA. You can also find a lot of variety at Cabelas.
Wayne, great job with the field target shooting.
Joe B., I was thinking of reports that the army was strained with multiple deployments that wer causing people to leave the service. Hopefully that has been allayed with the draw-down in Iraq and the increase in the size of the army by the Secretary of Defense.
BG_Farmer, that is some nice shooting you reported with the Savage rimfire. Sub-minute at 50 yards is as good as the Anschutz 1907 can do. Have you modified the protruding clip or gotten used to it?
Matt61
Matt61, BG_Farmer or whoever…
Is anyone else out there shooting the old remington .22lr rifles..
Like the 550-1, 541T, 513T, 511 or similar.. only a few of the ones I've collected have a scope rail, so those are the only ones, I could compare to 1/2" groups at 50 yards… guess what… they can come close.. and I've not tried any good ammo yet.. the best I've found for sale is Federal "Champion" .22 cal long rifle 40gr. solid nose 1,240 fps.
I read that most of these models have the same or similar barrels..
Even the open sight ones I've got group real well..
Anyway.. just one more gun to try if you like.. I like… you might too!!
Wayne,
Wayne,
I think I shot one of those when I did youth rifle shooting at a gun club several years back. I'm not sure the exact model, but I know it was a Remington .22LR. Lot of fun.
Jake
Thank you, BB. That matches my best as well (resting, not off-hand 🙂
Jake,
They made so many slightly different models, some bolt action single shot, bolt action with a tube magazine, bolt action with a clip magazine, and semi-auto (550-1) and others with a tube magazine..
All I seen have a plain but very comfortable walnut stock.. I'm up to six now, and haven't been disappointed yet… Real fun rifles as you said!!.. and I'll add accurate too!
The military ordered a lot of them for training the troops.. I think it was the 521-T and 541-T.. I've got one of each and they are real fun with the peep sights.
I'm probably bias, because of my Dad's old 550-1 being the first firearm I shot as a kid…
fulablob was the word verification
Wayne
Wayne, all I really remember is that it had a semi-pistol grip wood stock, right hand bolt, and I believe it was single shot, as I don't remember a detachable magazine.
It was quite a few years ago, though, and I remember the shooting more than the gun. I know it was a Remington, though.
Wayne,
Thanks for the detailed reults of the match . Seven Thatchers wow, but no Margaret.
Didn't we agree to use a tomato paste can for the bucket?
Try some standard velocity .22 long rifle ammo.
Mr B.
Wayne,
Those Remingtons sound good. Incidentally, that Federal load seems to spec. out close to the 40g RNCP MiniMags I've been using for breakin. Apparently CCI and Federal are under joint ownership, now (ATK?).
I've already bought my 1 firearm for the year, but it looks like I may be getting an exemption and a blackpowder kit for my birthday in a bit (fingers crossed). My five year old — who helped me tear down (up?:)) the 36-2 — is really excited about helping with a muzzleloader, and our boss surprised us both saying it was OK. Another rimfire would be pushing it though:).
The last list of buckets from you was drink can at 100 yards, 3 lb. coffee can at 150, and 3 gal. bucket at 200. I still like the tomato paste can at 100 that Mr. B alludes to, as well, but since I intend to win, I don't want to set the rules:). Of course, this is just bravado, now that you are ranked:).
Matt,
The BV has made me happy since its first shot, and I'm almost hopeful it can hit 1/2 MOA with some match ammo and a little more practice on my part — there have been quite a few 2 or 3 shot bugholes. Just for full disclosure, these are rested groups — my offhand groups haven't improved that much:)!
I've seen several reports that show other BV's shooting as well or better than mine, but I'm guessing they vary quite a bit more than Annies, and I've heard/seen a few MkII's with real problems and/or mediocre accuracy.
I'm still putzing around with ideas on the magazine. Since I only use it single shot, I can shoot without it (and unscrew the retaining clip), but the feeding ramp on the magazine makes loading easier. I think I found a single shot adapter, but you may know I'd prefer to make it myself:).
The real surprise I had recently was my other savage, the 111 .30-06. I was happy with 1.5" groups at 100 yards with it, but last time out with it I noticed that the groups from a cool barrel had a consistent pattern, two shots close (from touching to 5/8") and a third "flier" to the left. I had been suspicious of the forearm clearance on the right side, but the heat that day must have exaggerated its impact so that I noticed what was going on more. I relieved the forearm some (and may add a stiffener) and can't wait to try it out.
One of the BR regulars that was there seemed pretty impressed that it was shooting as well as it was, but I would love to get it sub-MOA, too, although I think I said I wasn't going to worry about it:). My elk lottery submission didn't get me picked, so I've got plenty of time for practice:).
One other way it surprised me was that I used a different rest with it (I mostly use bags if rested) and the height was wrong, leaving me with a nasty aching shoulder:).
BG_Farmer,
That encourages me about the Federal .22lr. I went all out and bought a case of 10 bricks of 500, since it was a no reserve auction.. I lucked out, and got the case for $265… $2.65 per 50 box is not bad for this ammo world..
They sure have been the best so far in all my .22 rimfires.
What rounds are you shooting in the savage 111 30-06?
I'll be suckin hind tit on the 100 yard tomato paste can and no scope… I'll be lucky to see it with my eyes!!! let alone hit it!!
but launch a volley just the same!
Wacky Wayne
Wayne,
If they shoot that well, its a pretty safe deal. I'm sucking it up to order an assortment of match ammo, but the pricing and variables these days makes me a bit queasy, and "testing" just isn't as much fun as shooting with something you know. MOA is good enough for most things, in my opinion.
.30-06 = 150 gr. CoreLokt PSP's. Nice light load for plinking:). Given the thin barrel and intendend purpose (field only), I'm thinking 1" 3 shot groups at 100 would be a more than reasonable goal:).
Bucket shoot — the tomato can is tiny: aim small, miss big:)? I'm happy with your target list.
Factory ammo costs about $85/100 right now. I reload for about $8/100.
such a bs
$8/100 is a factory price for primers only
and $85/100 is price for Golden Ammo with Swarovski
Hi B.B.
I got some convincing groups with Gamo Pro-magnum (7.8 grains, 0.177) for my Diana 350 Magnum. Howevre, I am worried this pellets do NOT cushion well. Will you please guide me if this is so?
Thanks,
Sasan
Sasan,
Go by how the gun feels when it shoots. If this pellet doesn't change the way it feels, it's probably good. But observe for more vibration, different sounds and more detonations. That's the sign the gun isn't happy.
B.B.
I love my 1377crosman stock, whats all this modification talk, Yeah less plastic would be nice, This gun screams. I have knocked squirrels off the ground and into a spiral with this baby at 30 to 40 yds with 11.5 grain beeman pellets, thats 9.2 ft lbs at 600 fps although with this heavy pellet maybe less.I have owned crosman rifles and pistols thru my life but none as powerful as this gun. NOT FOR ANYONE UNDER 16 IN MY BOOK.Will get wood grips only. what a sweet gun and very accurate, just dont overload on the coffee before you shoot. Thanks to B.B Pelletier for all his informative talk on issues.